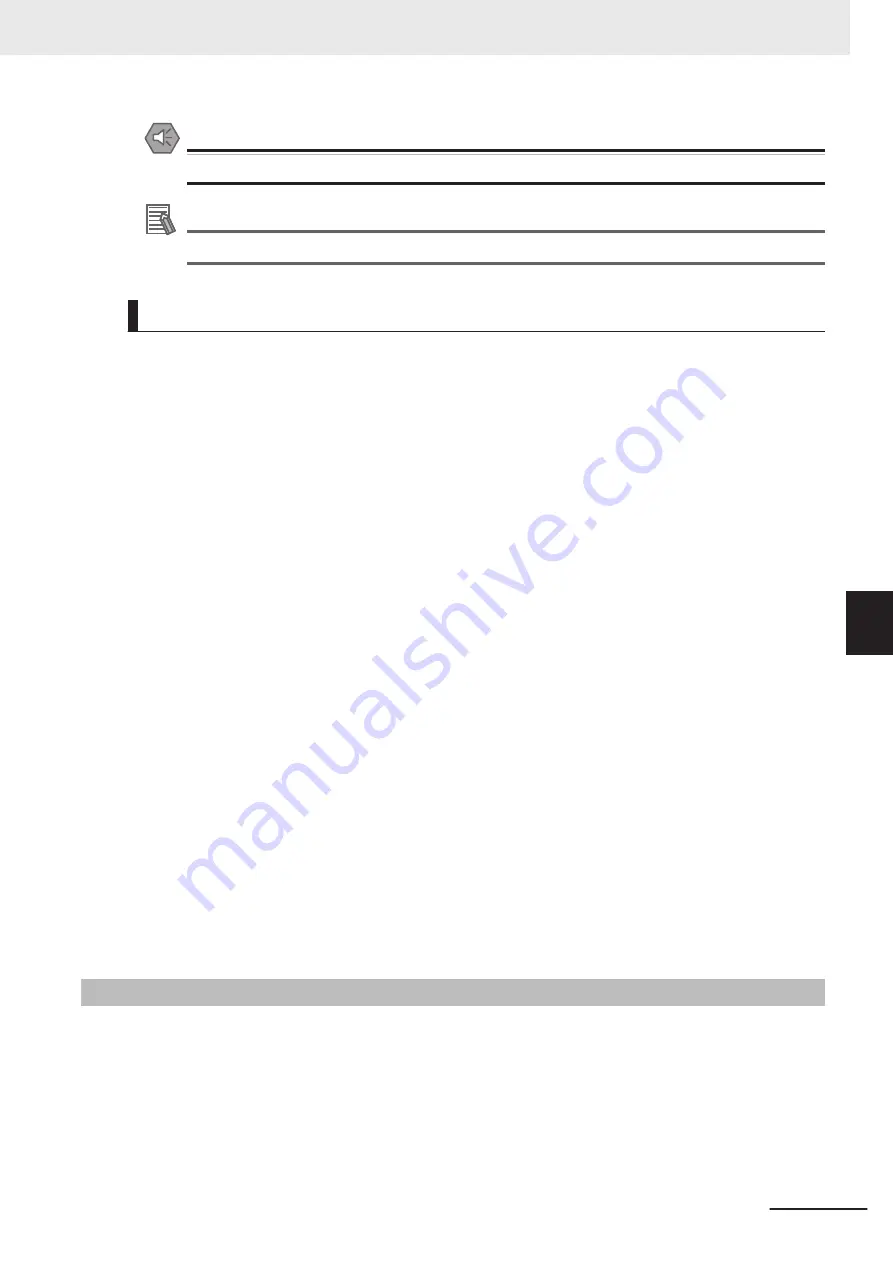
Precautions for Safe Use
The High Power indicator must be operational to satisfy safety requirements.
Additional Information
Refer to
3-11-3 Safety Equipment Checks
on page 3-47 for more information.
High Power Indicator Check
The robot monitors current used by the High Power indicator. This is to ensure that a High Power indi-
cator device is connected and functioning properly to satisfy safety requirements.
If the robot does not detect a current between 10 mA to 500 mA when High Power is requested, an
error condition (-924) *Front panel HIGH POWER lamp failure* will be present and High Power will not
be enabled.
The High Power indicator needs to be periodically checked for correct functionality.
The following considerations should be made before beginning the High Power indicator check proce-
dure.
• Control power and High Power supplies need to be available.
• All connected safety devices must be capable of providing signals for a safe state.
• The robot High Power needs to be disabled and robot motions will not execute during this proce-
dure.
• High Power safety timeout must be enabled to allow the indicator to flash after a High Power re-
quest is made. The recommended setting is 10 seconds. Refer to
Sysmac Studio Robot Integrated
System Building Function with Robot Integrated CPU Unit Operating Manual (Cat. No. W595)
for
more information.
High Power Indicator Check Procedure
Use the following procedure to verify that the High Power indicator is working correctly.
1
Apply Control Power to the robot and disable High Power.
2
Make a High Power request using one of the methods described in
3
Check that the High Power indicator flashes. After the High Power request is made and the in-
dicator is checked, the procedure is complete.
6-1-3
Checking Fastener Torques
The following fasteners must be periodically checked for proper torque.
• Mounting screws: 30 to 32 N-m
• External equipment mounting fasteners (if present): 2.5 N-m (M4 screws), 4.5 N-m (M5 screws)
• Hardstops:
• Joint 1 hardstops: 17 N-m
• Joint 2 hardstops: 17 N-m
• Joint 3 hardstop (clamp collar socket-head screw): 4.5 N-m
6 Maintenance
6-3
i4L Robots with EtherCAT User's Manual (I659)
6-1 Periodic Maintenance
6
6-1-3
Checking Fastener T
orques
Summary of Contents for i4-350L
Page 1: ...i4L Robots with EtherCAT User s Manual i4 350L i4 450L i4 550L I659 E 01...
Page 6: ...Manual Information 4 i4L Robots with EtherCAT User s Manual I659...
Page 54: ...1 Overview 1 26 i4L Robots with EtherCAT User s Manual I659...
Page 72: ...2 Specifications 2 18 i4L Robots with EtherCAT User s Manual I659...
Page 122: ...3 Installation 3 50 i4L Robots with EtherCAT User s Manual I659...
Page 138: ...4 Operation 4 16 i4L Robots with EtherCAT User s Manual I659...
Page 169: ...I Index I 1 i4L Robots with EtherCAT User s Manual I659 I...
Page 172: ...Index I 4 i4L Robots with EtherCAT User s Manual I659...
Page 173: ......