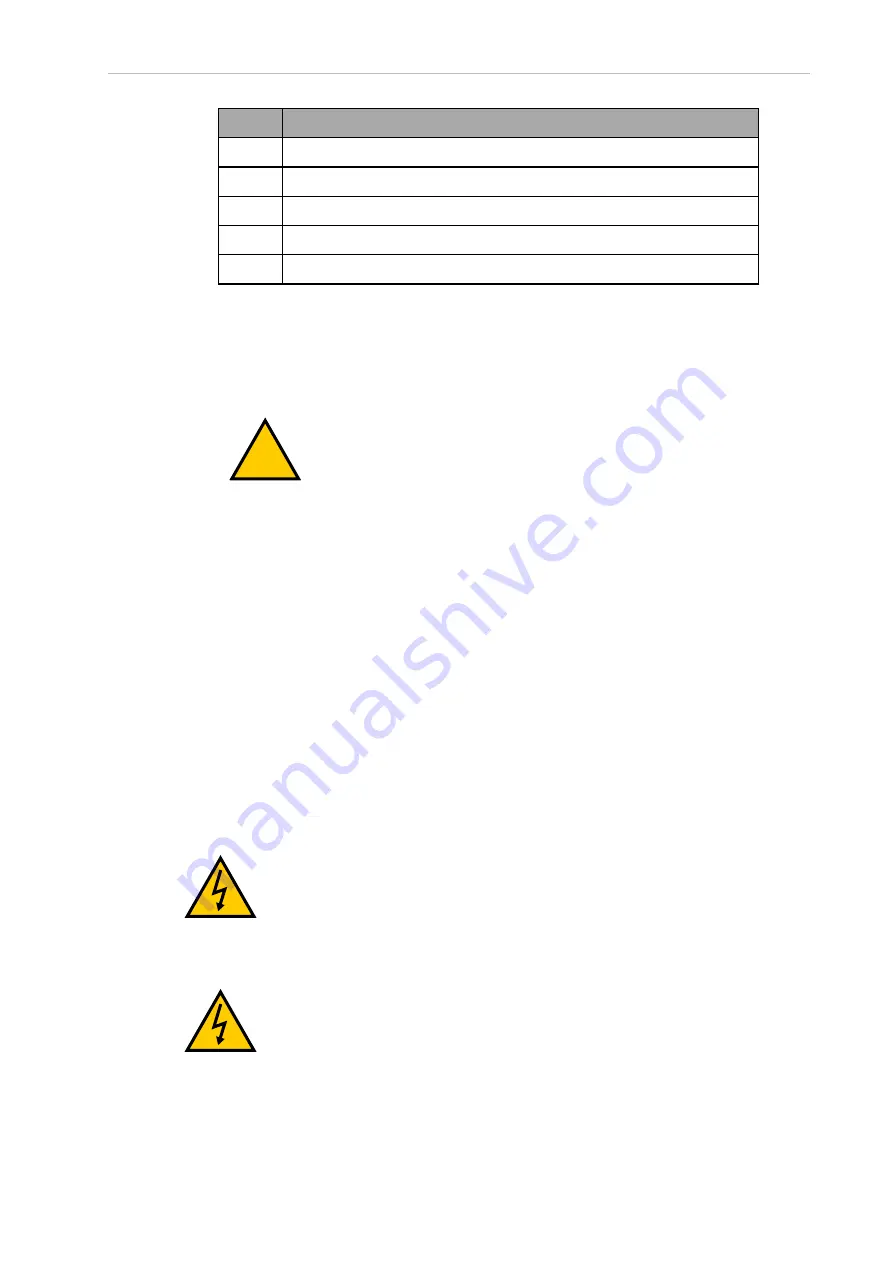
Chapter 4: System Cable Installation
Item
Description
C
Power Supply frame ground
D
8 A (max) in-line circuit protection
E
User-supplied 24 VDC (14-16 AWG) Shielded Cable
F
Molex Saber 18 A, 2-pin Connector
G
Ground screw on robot interface panel
NOTE:
To comply with standards, DC power should be supplied over a shiel-
ded cable with the shield connected to frame ground at both ends of the cable.
1. Connect one end of the shielded 24 VDC cable (E)to the 24 VDC power supply (B)
observing the correct polarity.
!
CAUTION: PROPERTY DAMAGE RISK
The 24 VDC output must be less than 300 W peak or 8 Amp (max) in-
line circuit protection must be provided for each connected robot. Refer
to (D) in Figure 4-10. .
2. Connect the cable shield (D) to frame ground on the power supply (C).
3. Plug the mating connector end of the 24 VDC cable (F) into the 24 VDC connector on
the robot interface panel(A).
4. Connect the cable shield (G) to the ground point on the robot interface panel (A).
4.4 Connecting AC Power Cable
Use the following procedure to connect the 200 to 240 VAC cable from the power supply to the
robot interface panel.
Additional Information
: Refer to External Connection Specifications on page 132
for more information.
IMPORTANT:
Do not apply AC power until all installation steps are complete
and verified and all safety measures are in place.
WARNING: ELECTROCUTION RISK
National Electrical Code (and/or local codes) require that you provide an appro-
priately sized branch circuit protection and lockout/tagout capability. Ensure
you comply with all local and national safety and electrical codes for the
installation and operation of the robot system.
DANGER: ELECTROCUTION RISK
ISO 10218-1, Clause 5.2.4 mandates that, during installation, you must provide
a fail-safe lockout to prevent unauthorized third parties from turning on power.
22792-000 Rev. A
iX3 565 Robot with EtherCAT User’s Manual
79