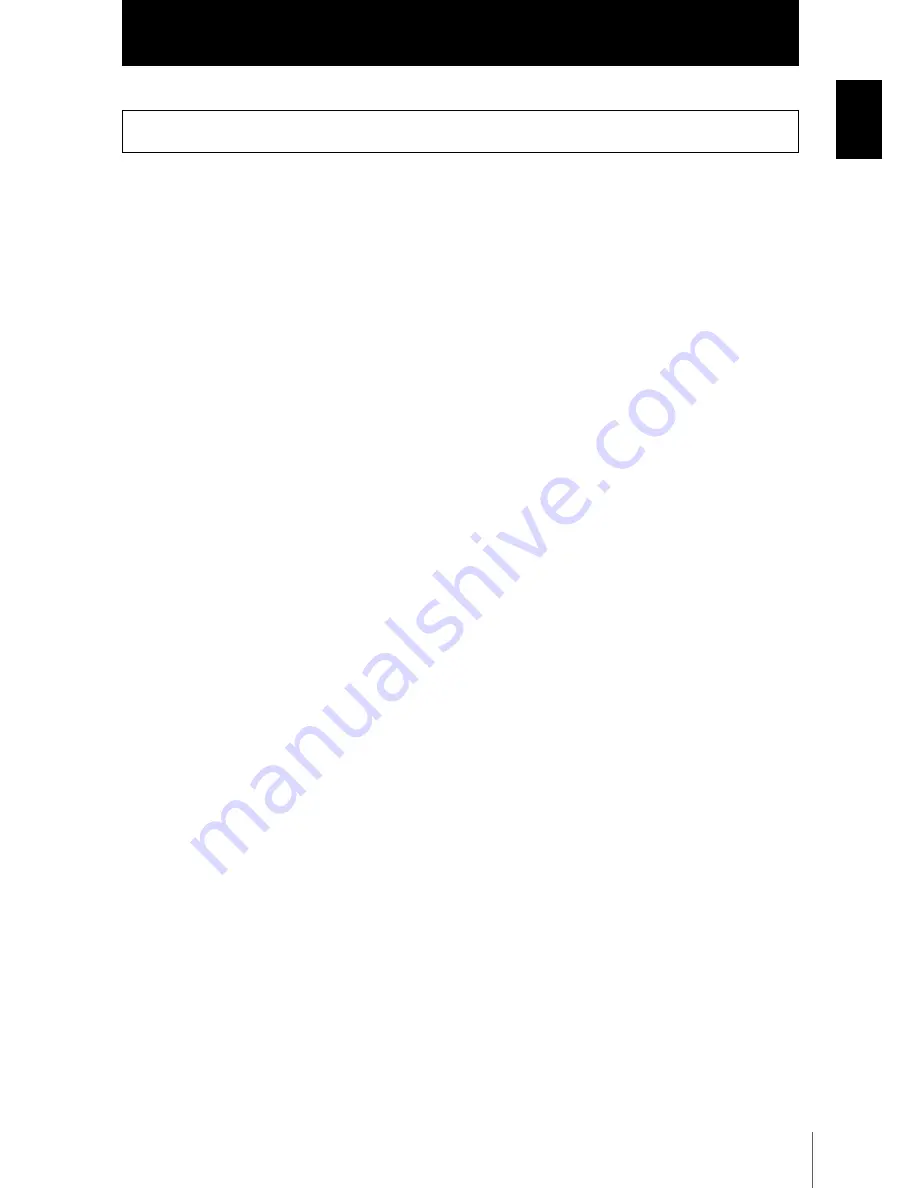
5
ZS-MDC
User’s Manual
In
trodu
ct
io
n
Introduction
Precautions for Safe Use
Please observe the following precautions for safe use of the products.
(1) Installation Environment
• Do not use the product in environments where it can be exposed to inflammable/
explosive gas.
• To secure the safety of operation and maintenance, do not install the product close to
high-voltage devices and power devices.
(2) Power Supply and Wiring
• The supply voltage must be within the rated range (DC24V±10%).
• Reverse connection of the power supply is not allowed.
• Open-collector outputs should not be short-circuited.
• Use the power supply within the rated load.
• High-voltage lines and power lines must be wired separately from this product. Wiring
them together or placing them in the same duct may cause induction, resulting in mal-
function or damage.
(3) Others
• Do not attempt to dismantle, repair, or modify the product.
• Dispose of this product as industrial waste.
Precautions for Safe Use
Summary of Contents for ZS-MDC
Page 12: ...10 Introduction ZS MDC User s Manual Introduction Editor s Note MEMO ...
Page 24: ...1 10 Section 1 FEATURES ZS MDC User s Manual Section 1 Part Names and Functions MEMO ...
Page 56: ...3 18 Section 3 SETUP ZS MDC User s Manual Section 3 Setting I O Assignments MEMO ...
Page 91: ...5 15 ZS MDC User s Manual Section 5 APPENDIX Section 5 Index MEMO ...