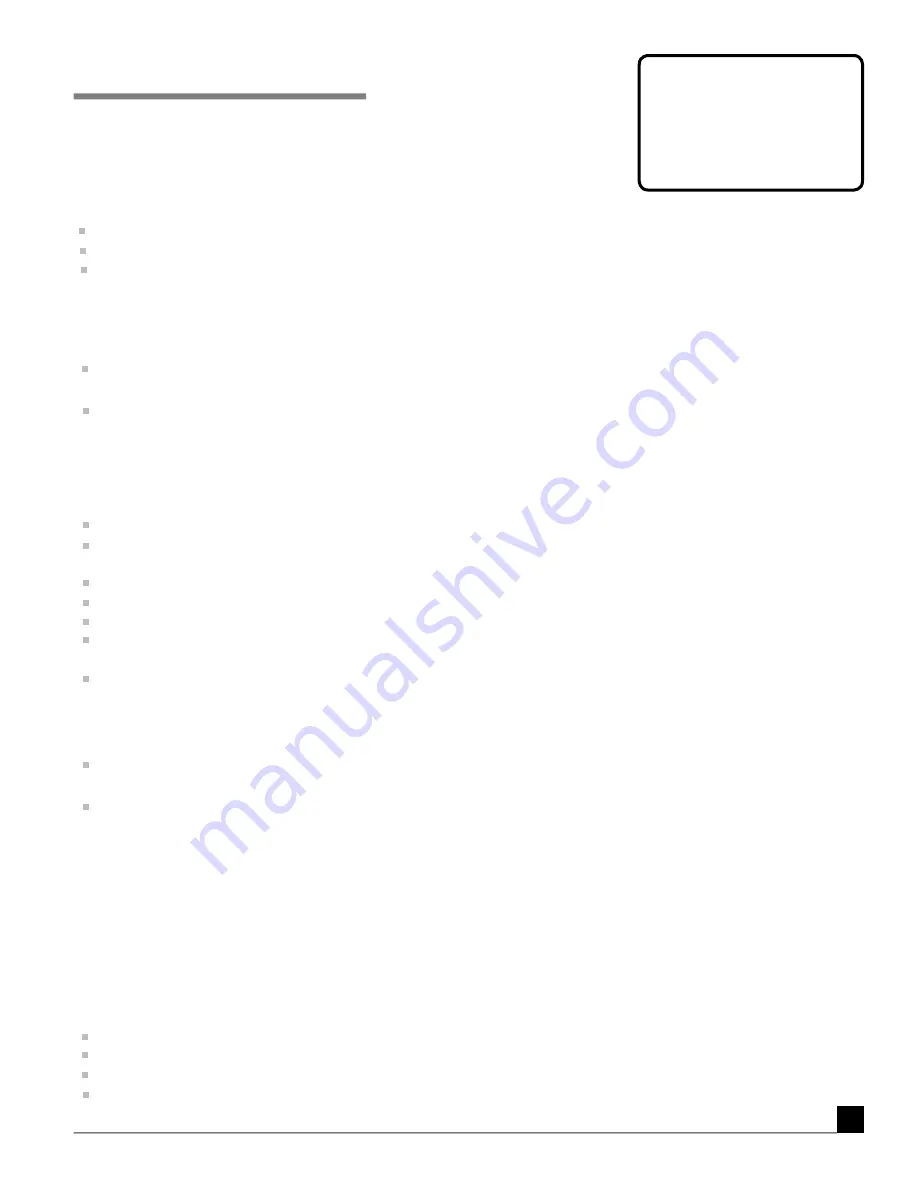
10hp Direct Drive © O.A.S. 2010
13
XII. Troubleshooting
Motor Overheating
Poor Dust Pick-Up at Woodworking Machines
Filter Clogging
Excessive Vibration
The motor’s internal circuit breaker will trip if the motor is overheating.
System should be completely bolted and sealed together.
Ductwork should be completely installed and sealed with sealant.
Air leaks between the collector and dust bin.
Motor not properly wired. Check wire connections.
- The lid of the dust bin and the cyclone must be in place and sealed when operating the dust collector.
- Make sure flex hose is not torn and the hose clamps are tight.
- Check drum lid; cover should have a foam seal and be well seated.
- Check for holes or leaks in the dust bin barrel.
Motor amperage too high - Shut system down.
Caused By:
Caused By:
Caused By:
Caused By:
- Check motor rotation - See wire diagram
Check breaker box. Make sure incoming power supply matches motor specifications.
Improper motor rotation - Running backwards will reducr suction by 30%.
Check length of duct runs and duct diameters compared to ductwork design guideline.
Make sure all ductwork is sealed. Large air losses will occur even through small cracks in the ductwork.
Use silicone, duct tape or duct mastic compound as a sealant.
Check for air leaks between collector and dust bin.
Close all unused blast gates at your woodworking machines.
Examine hood design for weaknesses according to the ductwork guide.
Check for a restricted pipe, too small a hood port or too small a branch line. See branch line diameter chart
in ductwork guide.
Be sure that your filter is clean. See filter cleaning directions.
Air leakage between cyclone and dust bin. Cyclone and dust bin must be air tight. Even small leaks can will cause
poor pre-separation in the cyclone.
Large chips clogging the filter:
- Check for a leak in the dust bin, flex coupling or lid. Check for split or torn flex coupling. (See also: Motor Over
-
heating Section above.)
- Make sure dust bin has not over filled. Dust bin should be emptied before dust reaches top of container.
- Interruption of air flow, such as vacuuming chips with a flex hose connection, will increase filter maintenance.
- Minimum 4” diameter pick up at tool location. Less than 4” will restrict air flow into collector and will increase filter
maintenance, If there is not enough air entry in system, open more blast gates.
- Make sure clamp around cyclone is tight and sealed with silicone.
Loose mounting bolts.
Excessive system pressure or restriction of air due to closed blast gates.
Accumulation of foreign material on the fan wheel.
Inadequate support structure.
Note:
If you continue
to experience difficulty
with your collector, call
Oneida Air Systems at
1.800.732.4065 for assis-
tance.