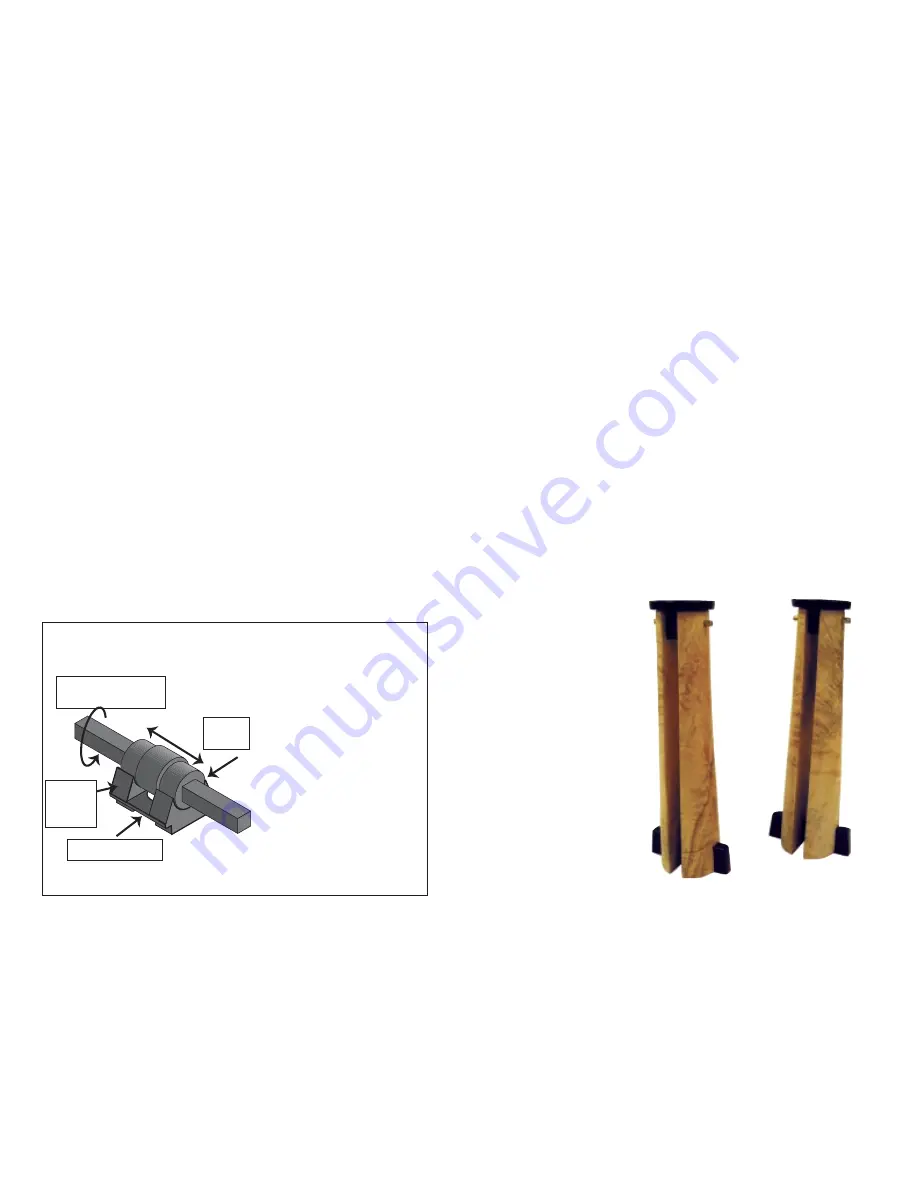
5
6
The BANJO/TOOLREST BASE is
ONEWAY's
own proven design that
assures even, powerful locking anywhere on the bed (patented feature).
The sliding cam is supported by a cam support block which rests on a
ledge machined in the toolrest base. To ensure continuing smooth oper-
ation, lubricate the mechanism whenever it seems to be getting sticky.
The banjo handle will clamp either to the left or right. Generally the
handle is adjusted so that when it is clamped, the handle is clear of the
bed. This allows the banjo to be clamped in all positions over the bed.
The clamp handle position can be adjusted via the Nylock Nut, under-
neath the banjo.
How do I adjust the Toolrest clamp lever?
The toolrest clamp lever can be adjusted to clamp in any position. To
change the position of this lever, unscrew the four screws that hold the
clamp nut in place, rotate it to the desired position and re-fasten the nut
with the screws. Note that there are eight holes in the clamp nut, allow-
ing adjustments of 1/8 rotational increments. The handle clamp position
is an individual preference, but the 4 O’clock position is a good place to
start.
Banjo - Toolrest Base
What is a sliding Cam assembly?
This assembly consists of: a rotating square shaft, a short sliding cam and a
support block for the sliding cam. The square shaft rotates the sliding cam.
The cam is supported on a cam support block
which in turn is supported on a
ledge machined in the tool rest
base. The block moves with the
sliding cam and supports the
shaft. Deflection of the cam shaft
is eliminated and there is no
longer a clamping difference
anywhere on the lathe bed.
Unclamp is always at the 12
o’clock position and clamping
may be adjusted to be repeatable
anywhere between 10 & 6
o’clock with RH and LH clamping always at the same angle.
Cam
Support
Block
Rotating Square
Shaft
Sliding
Cam
Support Ledge
There are four spindle bearings in the headstock. These bearings are sealed
and lubricated from the factory and should never need adjustment or lubri-
cation. The bearings and the spindle in your lathe are designed to take nor-
mal woodturning forces for a long time. The best way to ensure long bearing
life is to never hammer against the spindle.
Due to the size and the preload on the bearings the lathe may run quite warm
when it is new. As the bearings break in they will run cooler but will still get
warm. Each lathe is run in at the factory and checked for excess temperatures,
but it is a good idea to keep the speed below 2000 rpms for the first 30 hours
of operation. This allows excess grease in the bearings to escape and for the
seals to break in. When replacing the bearings it is best to replace the front
bearings with a matched set from ONEWAY Mfg. The rear bearings can be
replaced by any equivalent bearing.
Replacing the Bearings
To replace the bearings you must remove the spindle. The first step is to take
the belt off the motor pulley. Remove the nut on the back side of the spin-
dle and slide off the pulley. Remove the six bolts in the spindle nose cap. Grab
the nose cap and the entire
spindle assembly should
slide out. If it is tight, take
two of the bolts you just
removed and put them into
the two tapped holes in the
nose cap. Tighten them alter-
nately and this will jack out
the spindle. If you do not have
a proper set of bearing tools, it
is a good idea to send the spin-
dle back to ONEWAY to pre-
vent damage to the spindle
and to the new bearings.
Bearings
Candle Holders
by Christian Burchard