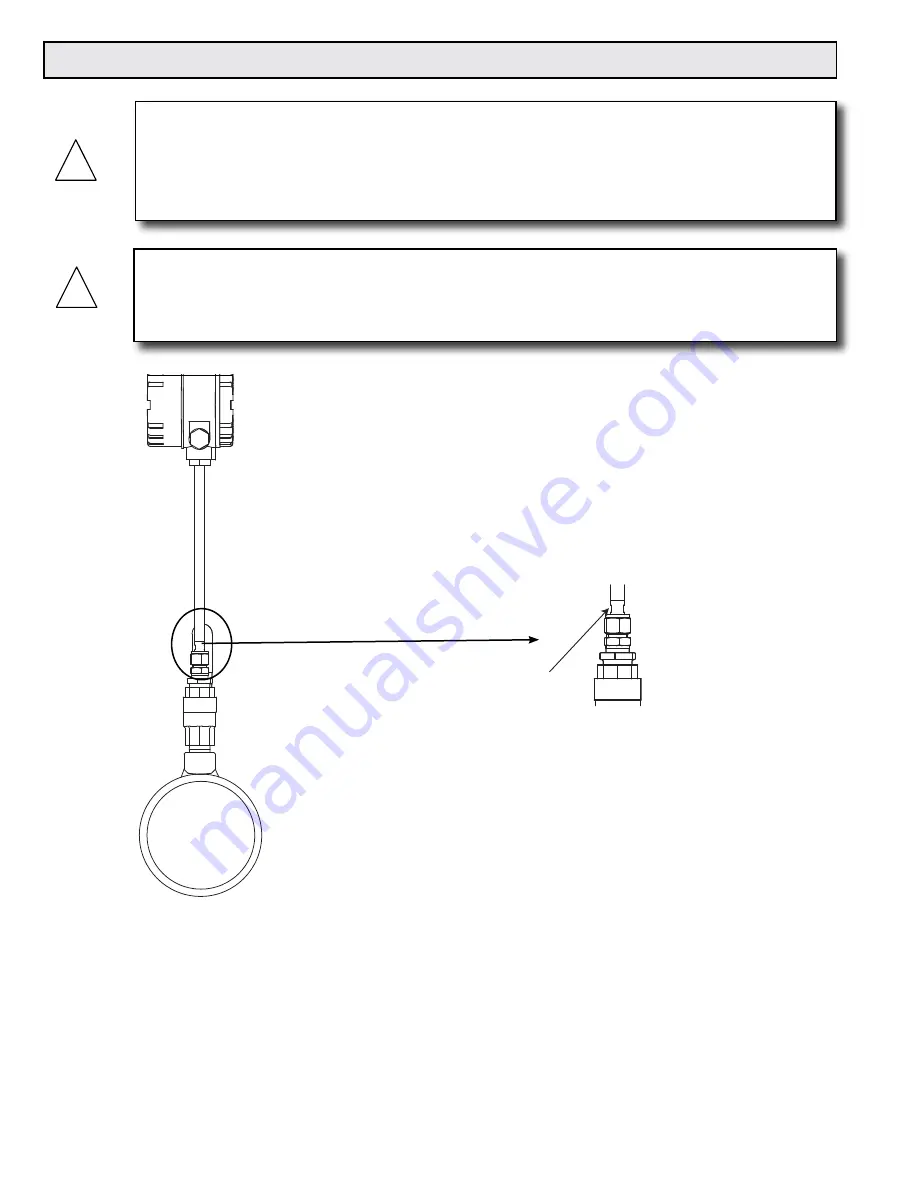
3.4 REMOVING THE FLOW METER
WARNING
SYSTEM MAY BE UNDER HIGH PRESSURE. When removing the flow meter, be sure to grasp
the electronics enclosure firmly by hand before slowly loosening the compression fitting. Failure
to do this will allow the pressure in the pipe to suddenly and rapidly force the meter from the
pipe causing serious injury. The hand effort required to hold the meter will be 0.2 times the pipe
pressure.
!
WARNING
Do not attempt to remove the meter from a pipe pressurized to greater than 200 PSIG. For pipes
pressurized above 200 PSIG isolate flow and relieve pressure in the pipe before attempting to
remove the meter.
!
Removal instructions for standard meter installations.
1.
While firmly grasping the enclosure,
loosen the compression fitting.
2.
Slowly withdraw the stem until the
flats located on the sensor are exposed.
3.
Close the ball valve and fully withdraw
the flow meter.
Stop here at the
flats on the sensor
Removal instructions for meter installed with safety cable and retaining collars.
1.
Confirm that upper retaining collar is installed at the top of the flow meter stem. If it is
not reposition the collar as shown in the drawing on the preceding page. Make certain
this collar is tightly connected to the stem.
2.
Loosen the lower retaining collar.
3.
While firmly grasping the enclosure, loosen the compression fitting.
4.
Slowly withdraw the stem until safety cable is taut.
5.
Close the ball valve, loosen the upper retaining collar and remove the flow meter.
| sales@mvandc.com | Phone: 877.566.3837 | Fax: 925.407.2903