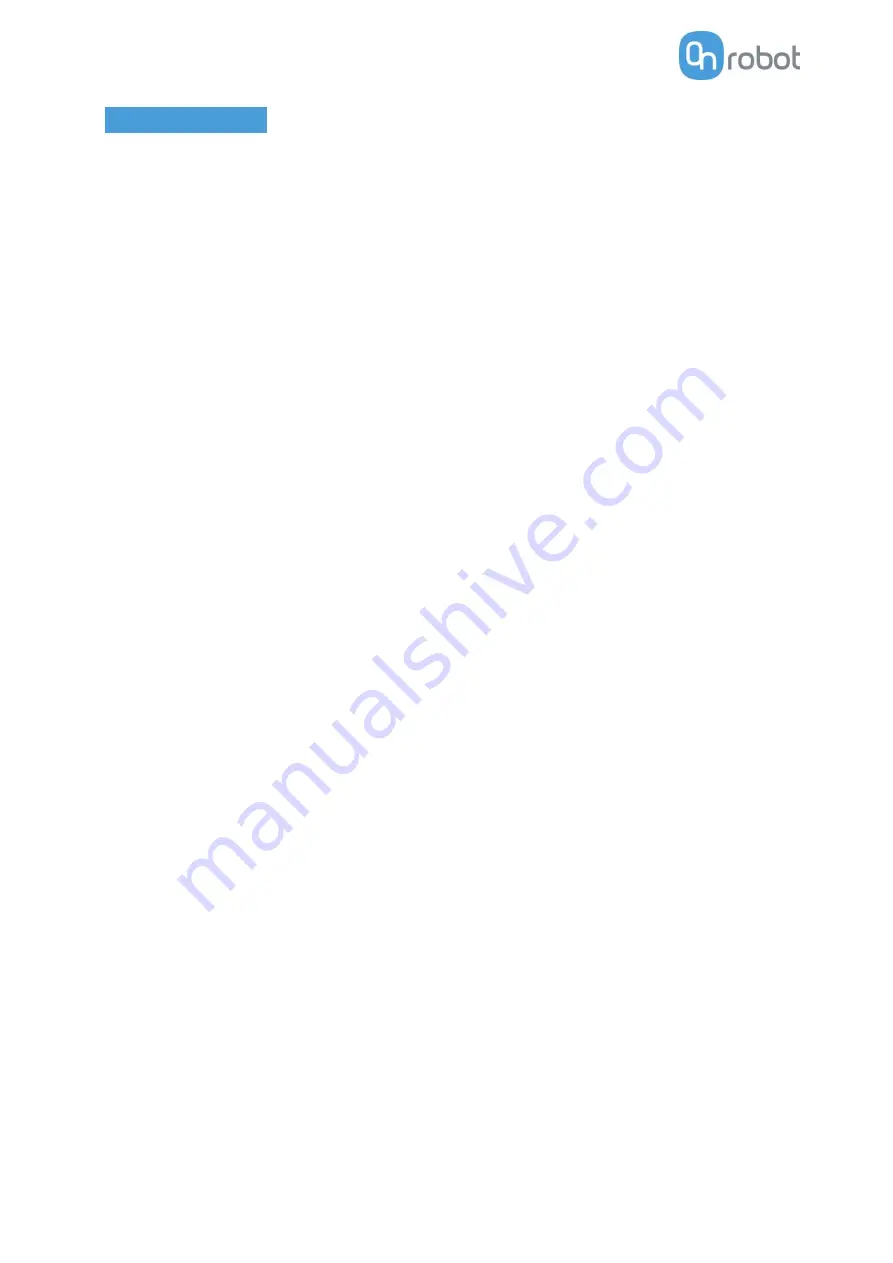
Operation
45
Screwdriver
Commands
•
Pick up screw
: Picks up a screw from the presenter. After moving the screwing tip above
the screw, which is in the presenter's pickup position, the Screwdriver pushes down the
shank with the given force and pulls it back with the given screwing length. The simplest
method to find the precise position is to move out the shank entirely, lead the tip in the
screw head, move back the shank, and move down the TCP vertically closer to the screw
pickup position.
•
Tighten
: The screwdriver drives the screw in the threaded hole with the given force and
torque in the given screwing length.
•
Loosen
: After positioning the screwing tip above the screw, the SD pushes out the shank
to search for it with the given force and drive it out.
•
Move Shank
: The screwdriver moves the shank to the desired position.
•
Stop
: The screwdriver stops both the linear and rotating movements.
•
Error and Result Evaluation
: Evaluates the occurrent errors without carrying out any
movements. In this command these options can be selected: popup window, log message,
and program stopping.
•
By clicking the
Execute
button, you can execute the command immediately.
If the
Wait for finish checkbox
is checked, the program will stop until the screwdriver finishes
the process.
If the
Error handling
checkbox is checked, the program will show a popup window, make a log
entry, and halt in case of an error.
Queries
•
Get Busy State
: (Boolean type). This is true when the shank or the screwdriver is in
motion.
•
Get Safety Trigger State
: (Boolean type). This is true when the safety switch is triggered.
•
Get Status
: (Number type) Returns states and error codes.
•
Get Error Code
: (Number type). Returns error code. The error codes are as follows:
0x004: Z-axis safety activated
0x008: Device Not calibrated
0x010: Init: Shank stall current not reached
0x020: Init: No shank index mark found
0x030: Init: Unable to home shank
0x040: Init: Invalid shank index placement
0x050: Init: No torque index mark found
0x060: Init: Torque difference overflow
0x070: Init: Index mark value has changed (clean encoder disk)
0x100: Wrong Quick Changer type
0x200: Wrong power supply type
Summary of Contents for 3FG15
Page 1: ...USER MANUAL FOR HANWHA ROBOTS ORIGINAL INSTRUCTION EN v1 1 6...
Page 28: ...Installation 28 Then click Apply...
Page 91: ...Hardware Specification 91 RG2 Gripping Speed Graph RG2 Work Range...
Page 94: ...Hardware Specification 94 RG6 Gripping Speed Graph RG6 Work Range...
Page 134: ...Hardware Specification 134 3FG15 All dimensions are in mm and inches...
Page 135: ...Hardware Specification 135 RG2 FT All dimensions are in mm and inches...
Page 136: ...Hardware Specification 136 RG2 All dimensions are in mm and inches...
Page 137: ...Hardware Specification 137 RG6 All dimensions are in mm and inches...
Page 138: ...Hardware Specification 138 Screwdriver All dimensions are in mm and inches...
Page 140: ...Hardware Specification 140 VG10 All dimensions are in mm and inches...
Page 141: ...Hardware Specification 141 All dimensions are in mm and inches...
Page 142: ...Hardware Specification 142 VGC10 All dimensions are in mm and inches...
Page 143: ...Hardware Specification 143 All dimensions are in mm and inches...
Page 144: ...Hardware Specification 144 Quick Changer Tool side All dimensions are in mm and inches...
Page 154: ...Certifications 154 9 Certifications...
Page 155: ...Certifications 155...
Page 156: ...Certifications 156...
Page 157: ...Certifications 157...
Page 158: ...Certifications 158...
Page 159: ...Certifications 159...
Page 160: ...Certifications 160...
Page 161: ...Certifications 161...