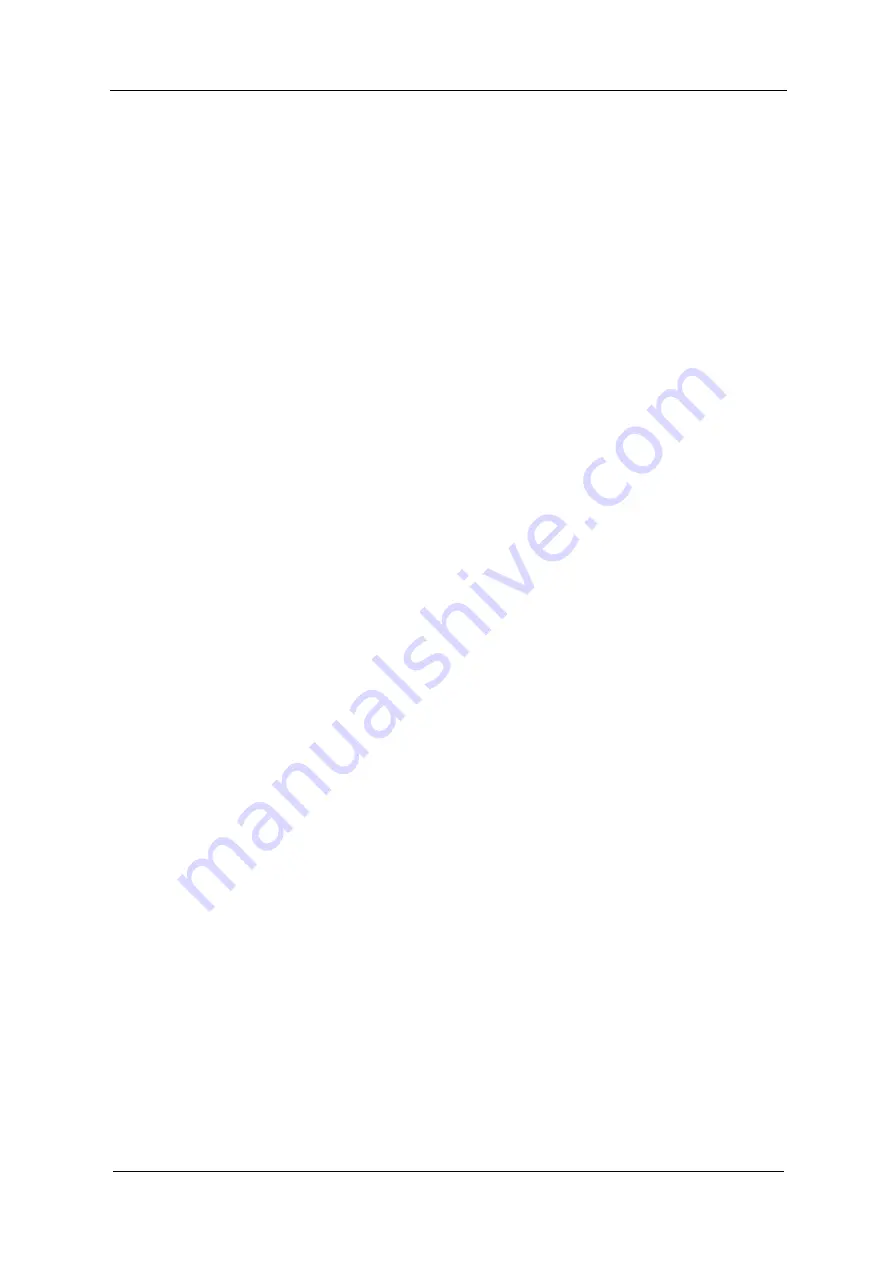
Description PROFIBUS
®
- 7 -
optek-Manual--1004-1010-02--ProfibusPA-US-2017-06-23
4
Description PROFIBUS
®
Introduction
Constant availability of information is one of the most important characteristics
of today's corporate communication. In the fields of production processes
(manufacturing, process and building automation), PROFIBUS
®
provides the
basis for networking.
PROFIBUS
®
is a digital communication system between the control system and
the measuring and control elements. It is the leading open fieldbus system in
Europe.
PROFIBUS
®
interconnects decentral field devices via one cable and integrates
them into a control system. Here, "real" process values are transferred instead
of mA-signals as in the 4–20 mA-technology.
In the following, the variants with their basic characteristics are listed:
PROFIBUS
®
DP
(Decentralized
Periphery)
This variant was optimized for manufacturing automation.
The transfer technology is a RS485 standard with a transfer rate of 12 Mbit/s. It
features a short response time, good diagnosis possibilities, noise-immune
transfer and easy handling.
PROFIBUS
®
PA
(Process Automation)
This version was especially developed for use in process automation. The
transfer technology is MBP with a transfer rate of 31.25 kbit/s. Use in hazardous
locations is possible.
There are two basic PROFIBUS
®
device types:
Master
The master controls data traffic on the bus (e. g. programmable logic controller).
It sends messages without external prompts and is also referred to as an "active
station".
Slave
Slaves are peripherals such as valves, drives, converters and analysis devices.
They shall only acknowledge received messages or transfer messages to the
master after master request. This is why they are also referred to as "passive
stations".
To keep up communication under PROFIBUS
®
, software protocols are
generated. The DP protocol is used for the transport layer between master and
slave. It determines type and speed of data interchange and defines the transfer
protocol of the PROFIBUS
®
system.
There are two DP master classes:
DP class 1 master
Controller of a DP system (e. g. controls, PLC, …).
DP class 2 master
Allows loading programs in controls, diagnosis, parameterization of DP slaves.
A PROFIBUS
®
network must always include at least one class 1 master.