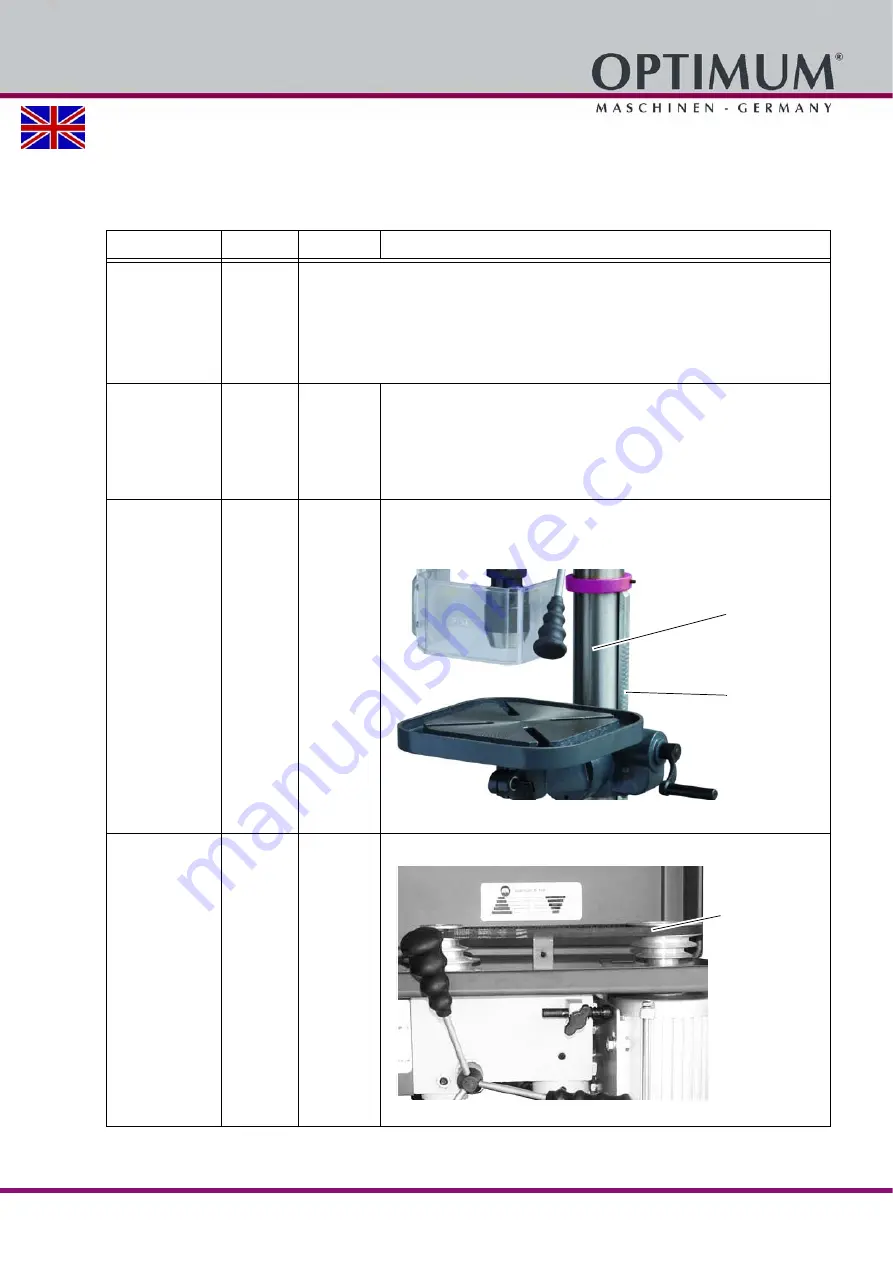
Version 1.0.1 - 2020-07-23
37
Translation of original instruction
B20 | B25 | B32
EN
B20-
B25-
B32_
GB.
fm
5.3
Inspection and maintenance
The type and level of wear depends to a large extent on the individual usage and operating
conditions. Any indicated intervals therefore are only valid for the corresponding approved con-
ditions.
Interval
Where?
What?
How?
Start of shift
After each
maintenance
or repair work
Dri
lli
ng
mach
in
e
weekly
Cla
m
pi
ng
bo
lts
V-
belt ten
s
ion
Check if the attachment screws for the V-belt tension on the
left and right side of the drilling head are well fastened.
Check if the V-belts are well tightened. Checking the tension
of V-belts,
Every month
Dri
ll
co
lu
mn an
d too
the
d rac
k
Oi
li
n
g
Lubricate the drill column regularly with commercial oil.
Lubricate the toothed rod regularly with commercial grease
(e.g. friction bearing grease).
Img.5-1:
B 20
Every 6
months
V-belt
s at
the drill
h
e
ad
Visu
al ins
p
e
c
tio
n
Check whether the V-belts have become porous and worn.
Img.5-2:
V-belt housing
Drill column
Toothed rod
V-belt