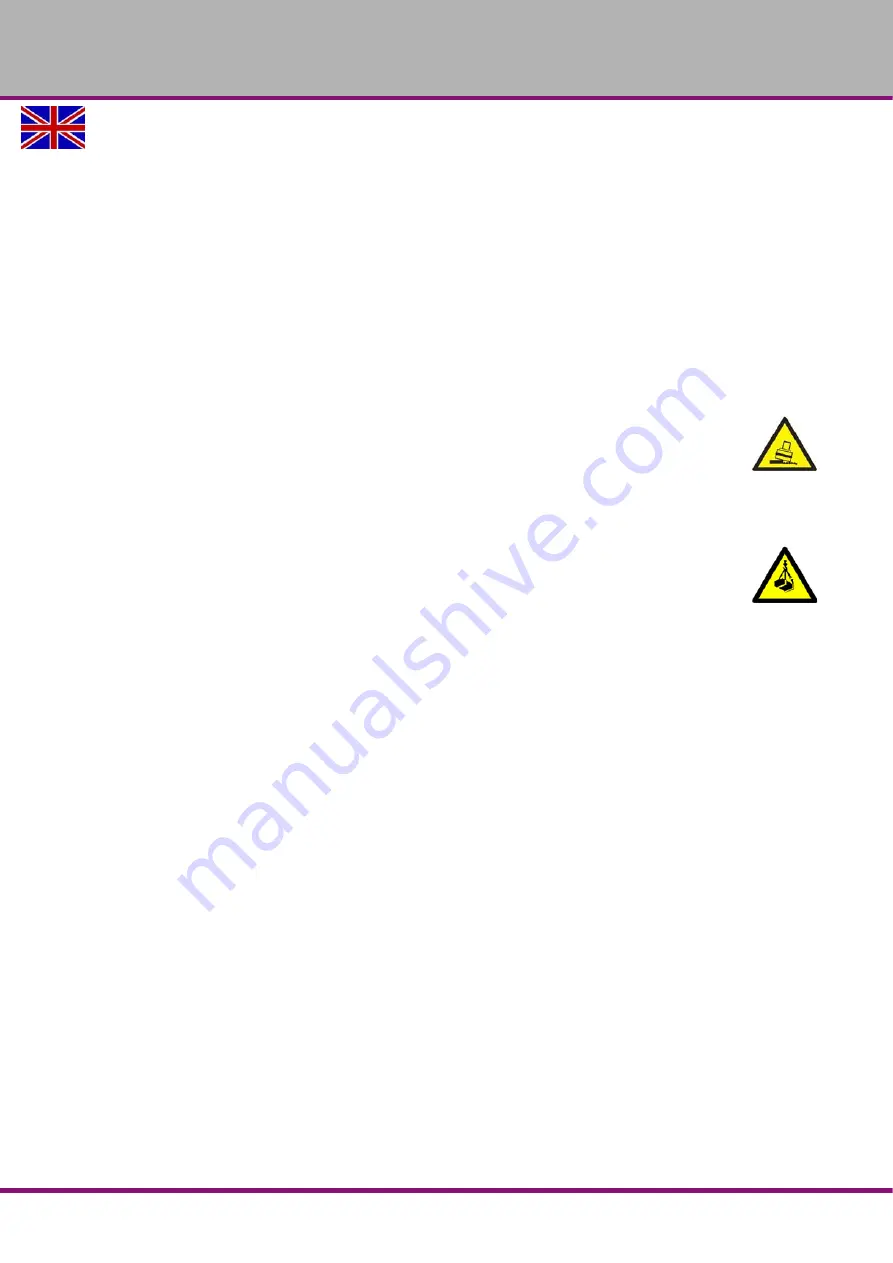
OPTIMUM
M A S C H I N E N - G E R M A N Y
Assembly
Version 1.0 dated 2015-06-18
Page 17
Original operating instructions
S275N | S275NV
GB
3
Assembly
3.1
Unpacking the machine
Transport the metal belt saw in its packing crate to a place near its final installation location with
a forklift before unpacking it.
If the packaging shows signs of possible transport damage, take the necessary precautions not
to damage the machine when unpacking. If any damage is discovered, the carrier and/or ship-
per must immediately be notified of this fact to establish any claim which might arise.
Inspect the machine completely and carefully, making sure that all materials, such as shipping
documents, manuals and accessories supplied with the machine have been received.
Compare the delivery volume with the delivery note.
3.2
Transport
WARNING!
Severe or fatal injuries may occur if parts of the machine tumble or fall down from the
forklift truck or from the transport vehicle. Follow the instructions and information on
the transport box. Note the total weight of the metal belt saw. Use only transport and
load suspension devices that can hold the total weight of the metal belt saw.
WARNING!
The use of unstable lifting and load suspension equipment that might break under load
can cause severe injuries or even death. Check that the lifting and load suspension gear
has sufficient load capacity and that it is in perfect condition. Fasten the loads properly.
Never walk under suspended loads!