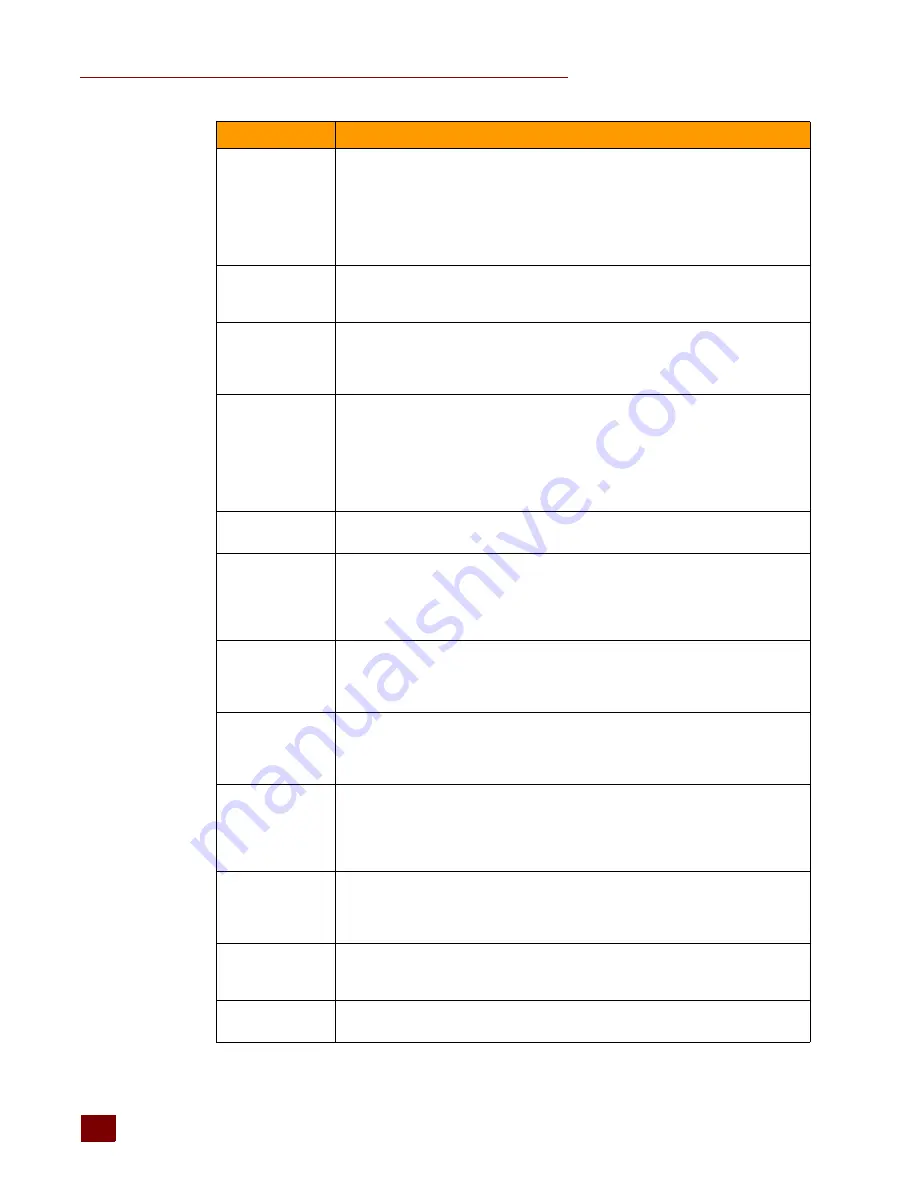
SNAP PAC BRAIN COMPARISON CHART
SNAP PAC Brains User’s Guide
20
Time-proportional
output (TPO)
Time-proportional output varies the duty cycle and the percentage of on time within that
cycle. TPO is often combined with a PID loop and used to control the output, for exam-
ple in a heater or oven.
(Digital output)—Supported by SNAP-PAC-EB1 only; requires PAC Project Pro and a
SNAP PAC controller.
(Analog output)—Both SNAP PAC brains support analog TPO using a SNAP-AOD-29
module.
On-pulse and
off-pulse measure-
ment
(Digital input; requires SNAP-PAC-EB1, PAC Project Pro, and a SNAP PAC control-
ler)—A pulse is a brief on (or off) state, usually repeated at a specific interval. The brain
can measure the first pulse, that is, the amount of time the input stays on (or stays off).
Pulse and square
wave generation
(Digital output; requires SNAP-PAC-EB1, PAC Project Pro and a SNAP PAC control-
ler)—A pulse turns a digital output on (or off) briefly, either once or for a specified num-
ber of times at a specified interval. A digital square wave is a specific pattern of on and
off states, repeated continuously.
Watchdog
(Digital and analog input and output)—A watchdog monitors communication with the PC
or other host device. If the host does not write data to the I/O unit for the length of time
set in the watchdog, the I/O unit automatically sets designated digital and analog output
points to the values you have determined.
If communication fails between the host and the brain controlling a process, a watchdog
makes sure the process is automatically brought to a safe state. For example, a valve
could automatically close to avoid completely emptying a tank.
Scaling
(Analog input and output)—Analog input and output points can be scaled as needed.
For example, you can scale a -5 V to +5 V input point to reflect 0% to 100%
Minimum and
maximum values
(Analog input)—Minimum and maximum values are sometimes called peaks and val-
leys. You can read these values at any time, for example, to record minimum and maxi-
mum temperatures. You can also reset min/max values. For example, if you want to
record the maximum temperature at point 2 in each 24-hour period, you must reset the
values after they are read each day.
Thermocouple lin-
earization
(Analog input)—The brain automatically converts the thermocouple junction's millivolt
values into temperature values, so you don’t have to. Choose the appropriate module
and make sure you configure the point as the correct thermocouple type (E, K, etc.) for
your purpose.
Offset and gain
(Analog input)—Offset and gain calculations are used to calibrate analog points. If a -50
mV to +50 mV input receives signals that are slightly off (not exactly -50 mV at the low-
est point, for example), the offset and gain can be calculated so that values will appear
accurately when read.
Clamping
(Analog output)—Clamping limits values that can be sent to analog output points so
they do not go above or below a specific value. For example, if you are using a 0–10
VDC output module, but the device attached to one of its points can only handle a max-
imum of 5 VDC, you can set an upper clamp of 5 VDC for that point. The values for
upper and lower clamp are set in engineering units.
Ramping
(Analog output; requires SNAP-PAC-EB1, PAC Project Pro, and a SNAP PAC control-
ler)—Some devices attached to analog outputs should not be abruptly stepped up or
down, because a sudden change might damage the equipment or cause other prob-
lems. Instead, you can gradually ramp the device up or down to the desired value.
PID loop control
(Analog points)—Proportional integral derivative (PID) loops are used to drive an input
toward a particular value (the setpoint) and keep the input very close to that value by
controlling an output. PID loops are often used in temperature control.
Average filter
weight
(Analog inputs)—A filter weight smooths analog input signals that are erratic or change
suddenly. See the
PAC Manager User’s Guide
for more details.
Feature
Description