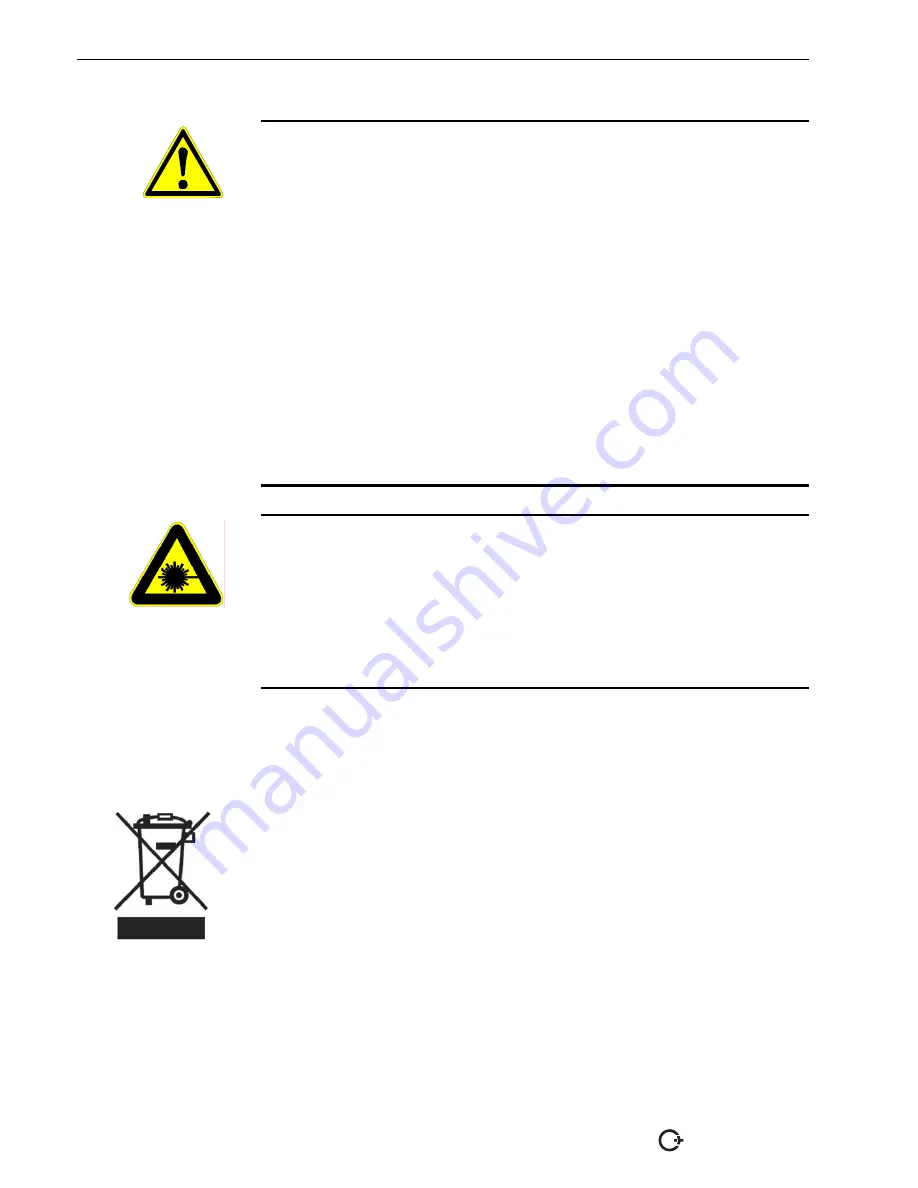
1 Notes on safety
Operating instructions GF 4 (AVM / MVM)
6
(01.08)
MT_GF 4_BA_04_790142762_01.doc
orbitalum tools
gmbh
Danger of death by electric shock
If the mains cable is damaged, live parts may cause death if touched directly.
:
Keep the mains cable of the pipe cutter motor
away
from the saw blade or
bevel cutter.
:
Do
not
let the cut-off pipe piece drop in an uncontrolled way.
X
Secure the falling pipe piece.
:
Do
not
run the machine unattended.
X
During the machining process, always keep an eye on the position of the
mains cable.
Unintended actuation of the ON-OFF switch
X
The machine may only be operated using a fault current (FI) protect switch.
X
Before changing tools, cleaning or performing any maintenance,
adjustment or repair work, pull the mains plug and allow the machine
to run to a stop.
Danger of being injured by laser radiation!
Failure to take due care can result in the retina of the eyes being damaged and
can thereby impair sight.
:
Do
not
look at the laser beam or view using optical instruments.
:
Do
not
point the laser beam in the direction of others.
:
Do
not
misuse the laser pointer and do
not
remove from the pipe cutter.
1.4 Waste
disposal
•
Dispose of chips and used gear lubricant oil according to the regulations.
Discarded electric tools and accessories contain a large share of
valuable raw and synthetic materials, which can be recycled. Therefore:
•
Electrical (electronic) devices that are marked with the symbol to the left,
may not be disposed of with household waste in accordance with EU
regulations.
•
By actively using the offered return and collection systems, you actively
contribute to the reuse, recycling and utilization of electrical (electronic)
devices.
•
Electrical (electronic) used devices contain parts, which must be handled
selectively according to EU regulations. Separate collection and selective
treatment is the basis for environment-friendly disposal and the protection
of human health.
•
Our products that were sold to you after August 13
th
, 2005 are taken back
and disposed of according to legal standards. The customer must however
bear the cost of delivery to Orbitalum Tools.
DANGER
WARNING
(RL 2002/96/EG)
Summary of Contents for GF 4 AVM
Page 51: ......