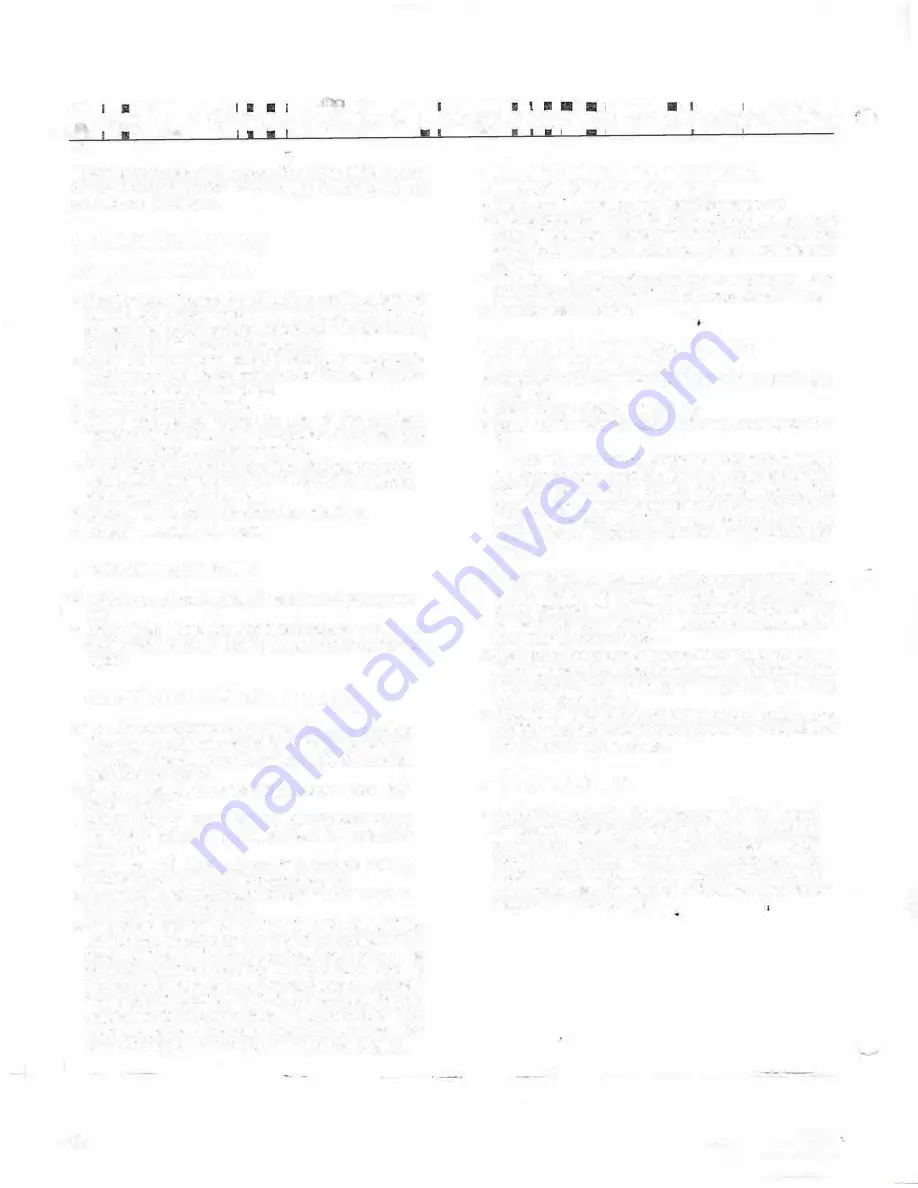
t.i;t•PXUl11=t•X•iiJ:Gii=il
11
:f:IU•ik•);1•l;JW3;•:[;t3Eii
If problems develop in the opera11on of the UPD motor/
driver package. please refer 10 the following list of
symptoms and causes
.
MOTOR FAILS TO TURN
Power Indicator is On:
o
No signal coming to driver. Check lo see if inpul signal
pulses are present and meet the required timing
characteristics. (5V, <25ma. length> 5 microsecond,
pulse rise/fall time < 2 microsecond).
o
Polarity or input signal pulse is wrong
If
the signal ,s
present and has the correct charac1erist1cs. the plus/
minus wires may be switched.
o
The load may be jammed
o
Driver overheated. Check to see if the overheat
indicator light is on If this is the case, the driver has
shut down because of overheating
o
Motor current turned off by a signal being applied to
the AW. OFF terminal. (All WINDINGS OFF.) Remove
signal at A.W, OFF terminal.
o
Run self test function to check for miswiring.
o Driver in wrong Input mode.
Power Indicator is Off:
o AC power not connected. Check the AC power wir
ing.
o Blown fuse. There are two fuses located under the
cover. Contact your local Oriental Motor dealer
tor
repair.
DRIVER OR MOTOR OVERHEATS
o
The U PD motor/driver is a high performance device.
The motor and driver normally run warm. Maximum
internal temperature for the driver is 80
°
C., and
tor
the motor is 130
°
C.
o
Ambient Temperature too high. Move motor 10 a
cooler location.
o
Motor/Driver is not sufficiently heal sinked. Mount
motor and drive to a metal surface to work as a
heat sink.
o
Motor currenl level set too high. Check selling
according to the instructions on page 12.
o
Current Cutback at Standstill Overriden. Turn current
cutback switch (A.C.D.) on.
o
Duty
cycle
too high or running time too long Either
reduce the amount of running lime compared to
stopped
t
i
me
,
or improve cooling Cooling can be
improved by either mounting the driver and motor to
heat conductive metal mounting surfaces, or by apply
ing forced air cooling. II lh1s 1s not possible in your
application, II is recommended thal the next size larger
motor be used. and ltie
motor
should be run at less than
rated running current. See explanation on page 9.
13
MOTOR TURNS ERRATICALLY OR
TURNS WRONG DIRECTION
o
Motor is mis-wired, or has loose connections.
o
Strong electrical noise 1s being picked up by input
signal Imes. Use twisted pair wires. move Input wires
away from electrical noise source. or use shielded
cable
.
o
01rec11on signal is being changed at the same time a
step pulse is being rece
i
ved
.
Change signal tim
i
ng
_
o
Run
self
test function.
MOTOR STOPS OR LOSES STEPS
DURING ACCELERATION:
o
Load requires a greater torque than the motor can
produce
o
Too steep an acceleration ramp.
o
Extreme mis-match of load inertia and motor rotor iner
lta.
For all three of the previous problems, a larger
motor, or a slower acceleration ramp may be needed.
(Some experimentation is often required in designing
acceleration ramps for step motors.) Proper motor load
matching is covered in chapter 4 and 5 of our
"TECHNICAL INFORMATION ON STEP MOTORS"
manual.
o
User-supplied pulse generator frequency
is
not stable
If the pulses are being generated directly from a corn
puler, especially an interrupt driven computer, the
pulse frequency may vary over a wide range causing
the molor to loose steps.
o
A stepping motor can only lose steps in groups of ten.
If the number of lost steps is not evenly divisible by ten,
lhen it is a controller or programming problem - not a
motor/driver problem.
o
In certain unstable, high performance applications, the
add11ton of a magnet damper may be needed to reduce
the chance of losing steps.
MOTOR IS NOISY
o
Motor/driver combination is too powerful for the
toad
being driven. Change to half stepping (remembering
to double the number of steps for each move).
Reduce the running current of the motor down to
match the torque actually require(/ by the load. Add a
magnet damper. Change the ratio of the transmission
between motor and load.
,... ,