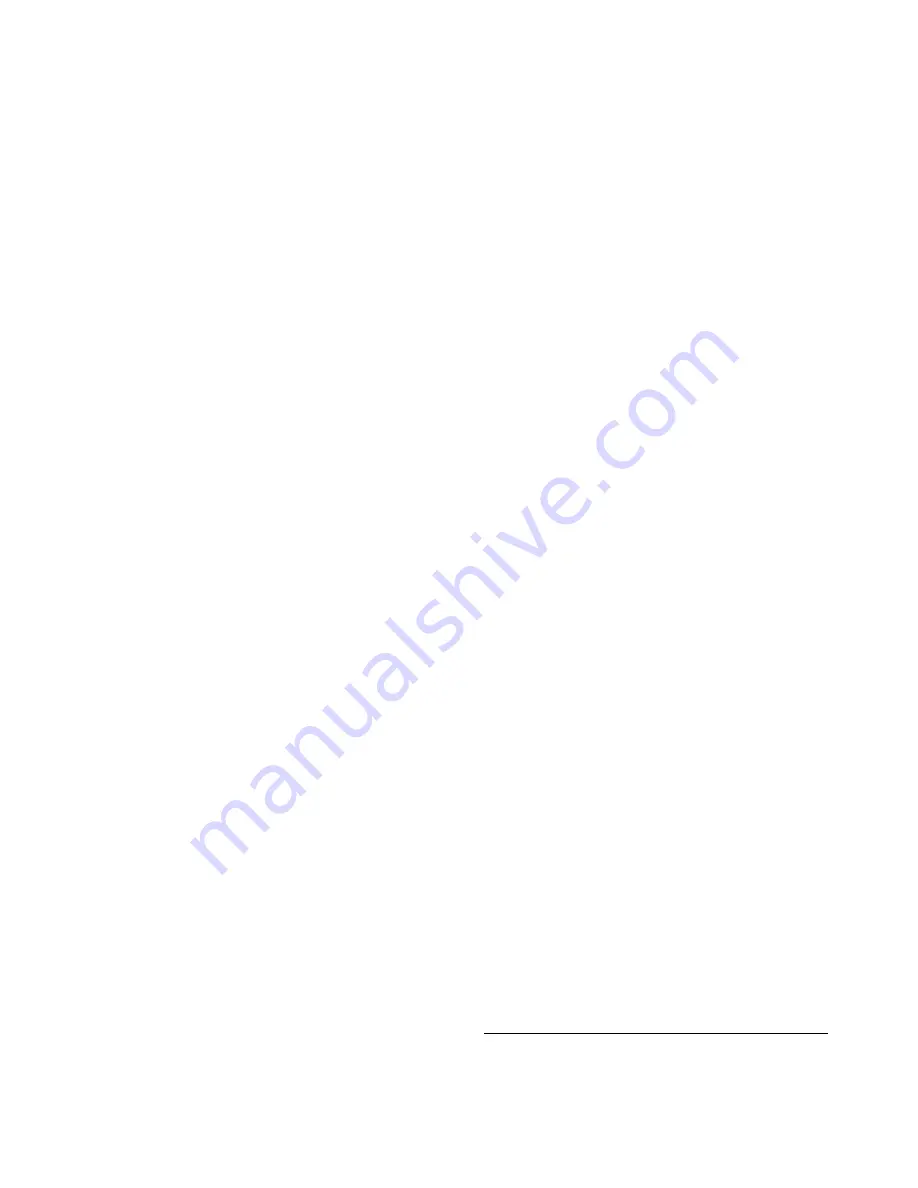
Page 6
should then be run for approx 3 days under load (i.e. turning
the platter) to free it up from vibration and to “bed in” the
bearings.
Like most turntable manufacturers we recommend that you
leave the turntable running between changing records as this
reduces the belt wear that occurs with constant stopping and
starting.
N O T E S O N S P E E D S T A B I L I T Y
If you measure the speed without a needle on the record the speed will
not be perfect. The speed should only be set with the stylus tracking
the record. If you don’t do this, the record will run slow once you put
the stylus on the record.
If you measure the speed within 30 seconds of putting the needle on the
record the speed will not be perfect as it takes a while to settle down.
Some people make the mistake of constantly watching the speed before
the deck has settled down and the needle has been on the record for
a good 2 minutes. Strobes are very accurate and the slightest speed
variation is picked up. 0.03% variation is observable which is over 30
times the accuracy of mid-priced decks on the market.
N O T E S O N M O T O R & S P E E D S E T T I N G
-Do not use the power supply for anything other than the dc
motor or the power supply is highly likely to be irreparably
damaged and you could also damage the equipment you are
plugging it into.
-The motor and main bearing will take at least 4 days to fully
run in and sound it’s best. For this reason it is best to do a final
speed check at the end of this period.
The speed stability of your deck will be excellent once
everything has settled down in a listening session.
When checking speed
- Be aware that the speed is subject
to temperature variation. This is due to oil thickening as the
temperture drops. 1 degree centigrade drop in temperature
results in a 0.1% drop in speed ( a 5 degree drop will be 0.5%
slow). 0.5% speed drift is barely noticable to the average
listner so this is not significant. Rega decks used to run 1% fast
all the time to put things in perspective.
The ear is less tolerant to music running slow than it is to
fast. For this reason it is worth setting the deck to run very
slightly fast at your average room temperature. Most houses
are centraly heated and maintain the temperature such that
significant variations simply do not occure.
Note that the main bearing and oil can take 2 hours to reach
operating temperature if the deck is left in a cold room. The
air in the room may warm up quickly but the metal in the
turntable will take a lot longer. For this reason it is not worth
constantly changing speed settings for absolute accuracy.
It is worth explaining that absolute speed accuracy is easy
to achieve at the expense of sound quality. The ac motors,
common to most decks are not prone to speed drift - however
they do inject a great deal of vibration. This, sadly is never
measured in technical reviews or people would be a lot wiser.
The subjective effect of vibration is highly detrimental to
sound quality when compared to fractional speed drift. For
this reason we prefer to offer superior sound quality rather
than the flawed illusion of technical perfection.
Further to this it is worth adding that we have experimented
with the latest highly sophisticated dc speed controls (£1000
plus trade cost) and found that although they hold speed with
unerring accuracy, the sound and dynamics of the music are
degraded to such a degree that a little speed drift is far more
preferable.
Note that on some flat belts you can get very significant change
in speed just by turning it inside out so mark which side you
use.
F I N A L C H E C K S
Your turntable is now ready to use. The following checks make sure
that you have set up the turntable correctly.
The motor pulley must not foul the underside of the
platter and should be inside the platter rim.
The tonearm should be set up with correct VTA i.e.
the tube should be approx parallel to the surface of the
record – see the tonearm instructions about this as it is
important to get the right sound and is often a matter of
experimentation.
With the tonearm and cartridge mounted, check that the
platter is level – if not, then level it by levelling the table
or surface that the deck stands on. If this is not possible
then use a combination of the height adjuster and cork
disc(s) placed under one of the rubber feet of the deck.
We understand that this may not seem the most elegant
solution but threaded adjusters would sacrifice sound
quality significantly.
Checking the platter
The platter spins freely and does not touch
the motor pulley or anything else.
If the
platter catches on the top of the pulley you
can adjust the height of the bearing house
by unscrewing it and threading it upwards.
This is very rare.
CHECKING THE MOTOR
Check that the motor housing is not
touching the plinth at any point.
Check that the motor is tuned correctly as
above.
Check that the belt is not rubbing on either of the flanges on the
top and bottom of the spindle. If it does try tightening the belt or see motor
tuning.
M A I N T E N A N C E O F T U R N T A B L E
To clean the deck, use a soft lint free cloth and wipe gently – if you have
grease marks etc then you can use a general-purpose anti-smear polish such
as Mr Sheen but only if necessary – wax furniture polish is to be avoided and
if possible use an anti-static type of polish. Do not spray the polish on the
turntable as it may clog up the cartridge etc but rather spray it onto a soft