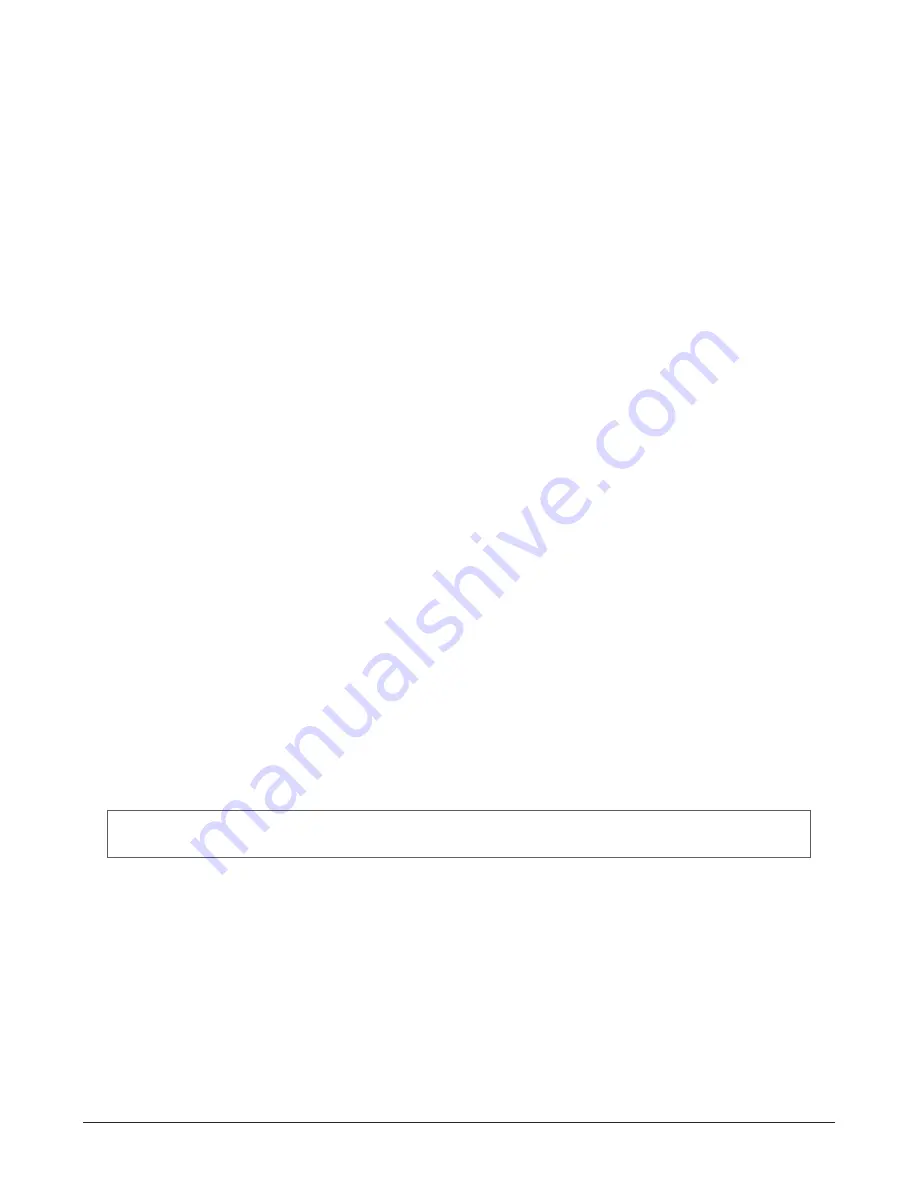
rect relative positioning when fully extended/retracted. In such cases, the sideways movement must be
corrected, using the dual refill check valves (F1, F2, F3 and F4). There are two valves for each side. Both
valves on each side must always be operated pairwise, into one of the two following positions:
l
Operating position: Upper check valve open, lower check valve closed.
l
Refill position: Upper check valve open, lower check valve closed.
There are two possible conditions in which a correction is needed:
Condition 1 - Insufficient fluid between pistons: Lower area of feed hopper not fully extended (lower cyl-
inder not fully extended) or upper area not fully retracted (upper cylinder not fully extended).
Corrective action:
1. Extend feed hopper as far as possible.
2. Switch to refill position.
3. Fully extend feed hopper.
4. Switch back to operating position.
5. Check both fully extended and retracted positions.
Condition 2 - Excessive fluid between pistons: Lower area of feed hopper not fully retracted (lower cylinder
not fully retracted) or upper area not fully extended (upper cylinder not fully retracted).
Corrective action:
1. Retract feed hopper as far as possible.
2. Switch to refill position.
3. Fully retract feed hopper.
4. Switch back to operating position.
5. Check both fully extended and retracted positions.
3.4 ELEVATOR AND SUB CONVEYOR
3.4.1 Settings
The speed of the elevator belt and the sub conveyor may be changed from the display unit, on the machine
settings page.
3.5 CHAMBER
The bale chamber can handle high loads, but the set chamber pressure and the resulting bale density must
be considered and possibly limited according to type of material. When baling certain material, too high
chamber pressures may reduce the bale chamber life time. See
section 6.1.7 "Machine settings"
and
tion 6.1.17 "Settings and explanations"
for how to set the chamber pressure.
NOTE: All references to valves found in this sub chapter can be found in the hydraulic schematic and valve over-
view in
3.5.1 Opening speed settings
Closing speed: Adjusting the bale chamber closing speed is done by turning the K1 valve. Clockwise
decreases the speed. Counterclockwise increases the speed.
Default setting: Close the valve and then open 1/2 turn.
3 SETTINGS AND HYDRAULIC ADJUSTMENTS
26
Summary of Contents for Dens-X Compactor
Page 14: ...1 6 DECLARATION OF CONFORMITY 1 GENERAL 14...
Page 103: ...8 7 MANUAL LUBRICATION CHARTS 8 7 1 The compactor 8 LUBRICATION 103...
Page 104: ...8 7 2 Feed hopper F25 8 LUBRICATION 104...
Page 105: ...8 7 3 Flexible drawbar 8 LUBRICATION 105...
Page 109: ...10 1 MAIN POWER SUPPLY E STOP SWITCHES AND ELECTRICAL CABINET 10 ELECTRICS 109...
Page 110: ...10 2 ELECTRICAL CABINET POWER SUPPLY RAIL 10 ELECTRICS 110...
Page 111: ...10 3 SENSORS AND MANUAL CONTROLS 10 ELECTRICS 111...
Page 112: ...10 4 VALVES FAN MOTORS AND PUMPS 10 ELECTRICS 112...
Page 124: ...10 9 SENSOR OVERVIEW 10 ELECTRICS 124...
Page 128: ...11 1 1 Complete diagram 11 HYDRAULICS 128...
Page 129: ...11 1 2 Wrapping table chamber and elevator control 11 HYDRAULICS 129...
Page 130: ...11 1 3 Plastic tying unit sub conveyor and feed hopper 11 HYDRAULICS 130...
Page 131: ...11 1 4 Additional feed hopper control for F25 and chamber drive 11 HYDRAULICS 131...
Page 133: ...11 2 VALVE OVERVIEW 11 2 1 Valve chart for Dens X 11 HYDRAULICS 133...
Page 137: ...12 6 3 Dimensional sketch F25 operating mode 12 SPECIFICATIONS 137...
Page 138: ...12 6 4 Dimensional sketch F25 transport mode 12 SPECIFICATIONS 138...
Page 142: ...M Maintenance 13 69 71 INDEX 142...