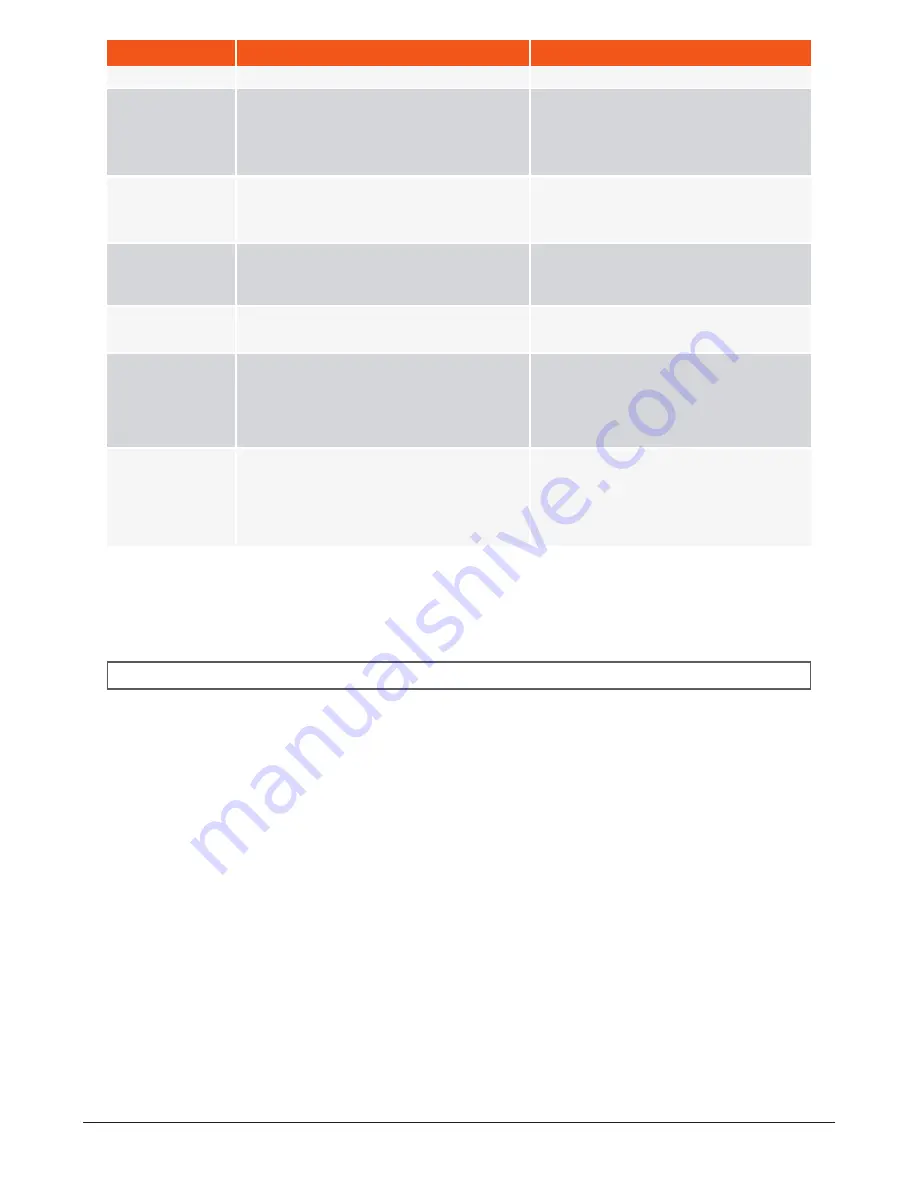
Problems
Cause
Remedy
NOTE: Correct motor mounting
Pump is working
but does not supply
grease
Air pocket in pump
Level in reservoir is too low
Pump element not building up pressure (no
air pocket)
Bleed the pump
Refill the reservoir
Replace the pump element
No grease collar at
all points of lub-
rication
Pump does not work
Clogging somewhere in the system
Refer to pump not working above.
See if grease is present on pressure
relief valve
No grease collar on
multiple bearings
A primary hose between main distributor
and sub distributor is broken
Leakage in fittings
Replace hoses
Retighten fittings or replace
No grease collar on
one bearing
The hose serving the bearing is defective
Leakage in the fitting
Replace hose
Retighten fittings or replace
Reduced pump
speed
High pressure in the system
Low ambient temperature
Conduct a complete system check
Run greaser manually for one minute (1
or 2 times) to lubricate the system. Then
restart machine and verify that the greas-
ing system operates as intended.
Grease on pressure
relief valve
System pressure too high
Main distributor clogged or system clogged
Valve relief spring defective
Check the system
Replace the distributor
Repair clogged bearing (housing)
Replace valve
8.5 OIL TEMPERATURE
ISO-VG system (International Standardization Organization - Viscosity Grade)
ISO standard 3448 splits industrial lubricants in ISO-VG classes. The standard tells which viscocity is good
for different temperatures. Lowest ISO-class equals thinnest oil.
NOTE: The temperature limitations is depending on the applied oil type.
8.6 APPROVED LUBRICANTS
8.6.1 Hydraulics
Recommended:
Titan Transway WB
8.6.2 Chain lubrication
Chain lubrication:
Titan Transway WB
8.6.3 Greasing
Greasing:
Use grease grade NLGI 2 with high pressure additives EP (Extreme pressure)
Recommended grease:
Shell GADUS S3 V220C 2
Statoil seway CAH 92
UNO X Multifak EP 2
8 LUBRICATION
101
Summary of Contents for Dens-X Compactor
Page 14: ...1 6 DECLARATION OF CONFORMITY 1 GENERAL 14...
Page 103: ...8 7 MANUAL LUBRICATION CHARTS 8 7 1 The compactor 8 LUBRICATION 103...
Page 104: ...8 7 2 Feed hopper F25 8 LUBRICATION 104...
Page 105: ...8 7 3 Flexible drawbar 8 LUBRICATION 105...
Page 109: ...10 1 MAIN POWER SUPPLY E STOP SWITCHES AND ELECTRICAL CABINET 10 ELECTRICS 109...
Page 110: ...10 2 ELECTRICAL CABINET POWER SUPPLY RAIL 10 ELECTRICS 110...
Page 111: ...10 3 SENSORS AND MANUAL CONTROLS 10 ELECTRICS 111...
Page 112: ...10 4 VALVES FAN MOTORS AND PUMPS 10 ELECTRICS 112...
Page 124: ...10 9 SENSOR OVERVIEW 10 ELECTRICS 124...
Page 128: ...11 1 1 Complete diagram 11 HYDRAULICS 128...
Page 129: ...11 1 2 Wrapping table chamber and elevator control 11 HYDRAULICS 129...
Page 130: ...11 1 3 Plastic tying unit sub conveyor and feed hopper 11 HYDRAULICS 130...
Page 131: ...11 1 4 Additional feed hopper control for F25 and chamber drive 11 HYDRAULICS 131...
Page 133: ...11 2 VALVE OVERVIEW 11 2 1 Valve chart for Dens X 11 HYDRAULICS 133...
Page 137: ...12 6 3 Dimensional sketch F25 operating mode 12 SPECIFICATIONS 137...
Page 138: ...12 6 4 Dimensional sketch F25 transport mode 12 SPECIFICATIONS 138...
Page 142: ...M Maintenance 13 69 71 INDEX 142...