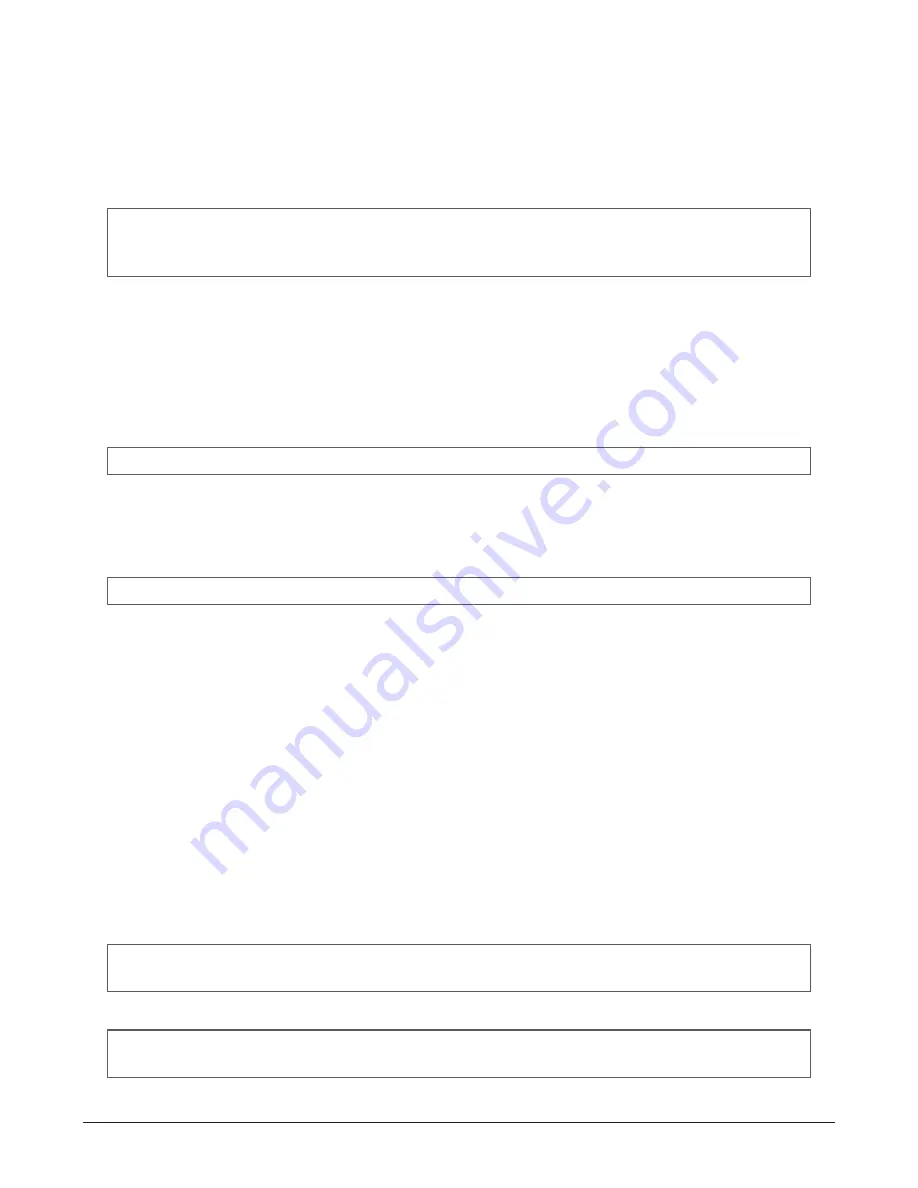
4.2.5 Leveling the machine
1. Ensure that the feed hopper is raised clear of the ground when leveling the machine. The feed hop-
per may be lowered onto the ground only when the machine is properly leveled.
2. Operate the valves for the hydraulic jack stands until the machine is properly leveled (See
4.2.3 "Lever/Controls overview"
3. Use the "spirit levels" on the frame during the leveling.
NOTE: The leveling of the compactor may change during time if the surface is not entirely solid. Therefore,
check the leveling regularly. Incorrect leveling may cause machine errors and uneven wear or damage to the
chamber belts.
4.2.6 Power take off
The PTO drive shaft is delivered with its own user manual from the manufacturer. Assemble the shaft
accordingly. Maintain and lubricate the PTO-shaft according to instructions given in the PTO-manual.
Power requirement:
120hp / 90 kW (diesel engine)
90hp / 75 kW (electric motor)
IMPORTANT: If any dangerous situations occur, shut down the PTO right away.
4.2.7 PTO Speed
The machine is designed for a PTO speed of 850 rpm. Ensure that the PTO speed and rotational direction is
correct (counter clockwise rotation when viewed from the tractor is correct).
NOTE: It is important for the machine performance (the hydraulic system) that the PTO speed is steady.
4.2.8 Electrical power source
The machine is equipped with a 24V electrical power system, and is self-supplied through an integrated
generator and a battery pack. The main power switch separates the battery pack from the rest of the sys-
tem, and must always be turned off whenever the machine is parked and during transportation.
4.2.9 Hydraulic connections
The machine has two separate hydraulic systems: The main system includes oil tank, pumps and valves,
and is powered by the PTO drive shaft via the gearbox. This system powers all functions used during baling
and are controlled either automatically or manually from the display unit.
The auxiliary system is connected to the tractors hydraulic system and is powered by this.
l
Feed hopper lifting cylinders, feed hopper halves (IN/OUT), jack stands, film roller storage, and draw-
bar.
All functions are operated through manual levers on the machine. See
section 4.2.3 "Lever/Controls over-
IMPORTANT: Check that all the valves between the oil tank and hydraulic pumps are opened before the PTO is
started.
NOTE: For energy preservation flow rate from tractor should be set no higher than 30 l/min. Oil port should be
turned off when not in use.
4 OPERATION
41
Summary of Contents for Dens-X Compactor
Page 14: ...1 6 DECLARATION OF CONFORMITY 1 GENERAL 14...
Page 103: ...8 7 MANUAL LUBRICATION CHARTS 8 7 1 The compactor 8 LUBRICATION 103...
Page 104: ...8 7 2 Feed hopper F25 8 LUBRICATION 104...
Page 105: ...8 7 3 Flexible drawbar 8 LUBRICATION 105...
Page 109: ...10 1 MAIN POWER SUPPLY E STOP SWITCHES AND ELECTRICAL CABINET 10 ELECTRICS 109...
Page 110: ...10 2 ELECTRICAL CABINET POWER SUPPLY RAIL 10 ELECTRICS 110...
Page 111: ...10 3 SENSORS AND MANUAL CONTROLS 10 ELECTRICS 111...
Page 112: ...10 4 VALVES FAN MOTORS AND PUMPS 10 ELECTRICS 112...
Page 124: ...10 9 SENSOR OVERVIEW 10 ELECTRICS 124...
Page 128: ...11 1 1 Complete diagram 11 HYDRAULICS 128...
Page 129: ...11 1 2 Wrapping table chamber and elevator control 11 HYDRAULICS 129...
Page 130: ...11 1 3 Plastic tying unit sub conveyor and feed hopper 11 HYDRAULICS 130...
Page 131: ...11 1 4 Additional feed hopper control for F25 and chamber drive 11 HYDRAULICS 131...
Page 133: ...11 2 VALVE OVERVIEW 11 2 1 Valve chart for Dens X 11 HYDRAULICS 133...
Page 137: ...12 6 3 Dimensional sketch F25 operating mode 12 SPECIFICATIONS 137...
Page 138: ...12 6 4 Dimensional sketch F25 transport mode 12 SPECIFICATIONS 138...
Page 142: ...M Maintenance 13 69 71 INDEX 142...