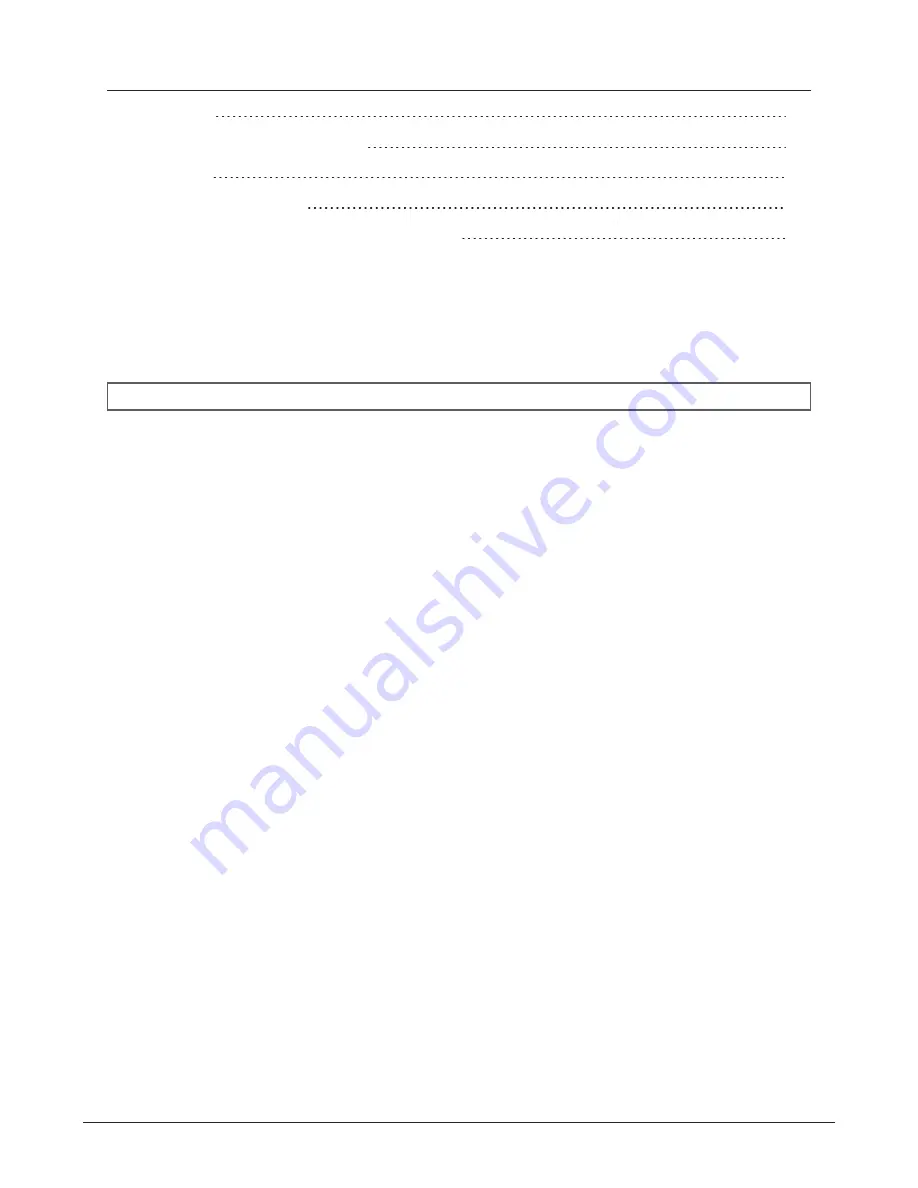
9 Preservation
9.1.1 Using high pressure washer
9.2.2 Oil filling in the grease lubrication storage
9.1 CLEANING
9.1.1 Using high pressure washer
The compactor can be cleaned with a high pressure washer. Avoid directing the beam towards any elec-
trical connections and components.
IMPORTANT: Use hearing protection when cleaning the compactor with a high pressure washer.
9.2 STORAGE
A thorough cleaning and a complete lubrication is recommended prior to long term storage. The control
unit must be kept warm and dry to ensure functionality. The control unit may be detached from the com-
pactor and stored inside during the storage period. Touch-up paint is recommended to avoid corrosion.
9.2.1 Long time storage
If you’re using grease of NLGI class 2 with EP additives (extreme pressure) there’s no need for special pre-
cautions to be made regarding long time or winter storage. Perform a complete lubrication service on the
machine before storage. If you’re using a grease type according to lubrication standards, but not having
the anti-corrosion effect, the system must be filled up with anti-corrosive oil. Regular motor oil is suf-
ficient.
9.2.2 Oil filling in the grease lubrication storage
This operation is easily done with an empty grease gun filled up with motor oil. Remove the piston and the
coil spring in the gun. Insert an empty grease cartridge and fill the grease gun while holding it vertically.
Attach the gun at the inlet on the main distributor and empty the gun into the system (1/2 litre).
9 PRESERVATION
103
Summary of Contents for MP2000-X
Page 14: ...1 6 DECLARATION OF CONFORMITY 1 GENERAL 14...
Page 98: ...8 6 4 Gearbox and gears for hydraulic motors Gear oil Renolin unisyn CLP 220N 8 LUBRICATION 98...
Page 99: ...8 7 MANUAL LUBRICATION CHARTS 8 7 1 The compactor 8 LUBRICATION 99...
Page 100: ...8 7 2 Feed hopper F10 8 LUBRICATION 100...
Page 101: ...8 7 3 Telescopic drawbar 8 LUBRICATION 101...
Page 105: ...10 1 MAIN POWER SUPPLY E STOP SWITCHES AND ELECTRICAL CABINET 10 ELECTRICS 105...
Page 106: ...10 2 ELECTRICAL CABINET POWER SUPPLY RAIL 10 ELECTRICS 106...
Page 107: ...10 3 SENSORS AND MANUAL CONTROLS 10 ELECTRICS 107...
Page 108: ...10 4 VALVES FAN MOTORS AND PUMPS 10 ELECTRICS 108...
Page 120: ...10 9 SENSOR OVERVIEW 10 ELECTRICS 120...
Page 124: ...11 1 1 Complete diagram 11 HYDRAULICS 124...
Page 125: ...11 1 2 Wrapping table chamber and elevator control 11 HYDRAULICS 125...
Page 128: ...11 2 VALVE OVERVIEW 11 2 1 Valve chart for MP2000 X 11 HYDRAULICS 128...
Page 132: ...12 6 3 Dimensional sketch F10 operating mode 12 SPECIFICATIONS 132...
Page 133: ...12 6 4 Dimensional sketch F10 transport mode 12 SPECIFICATIONS 133...
Page 137: ...M Maintenance 13 65 67 INDEX 137...