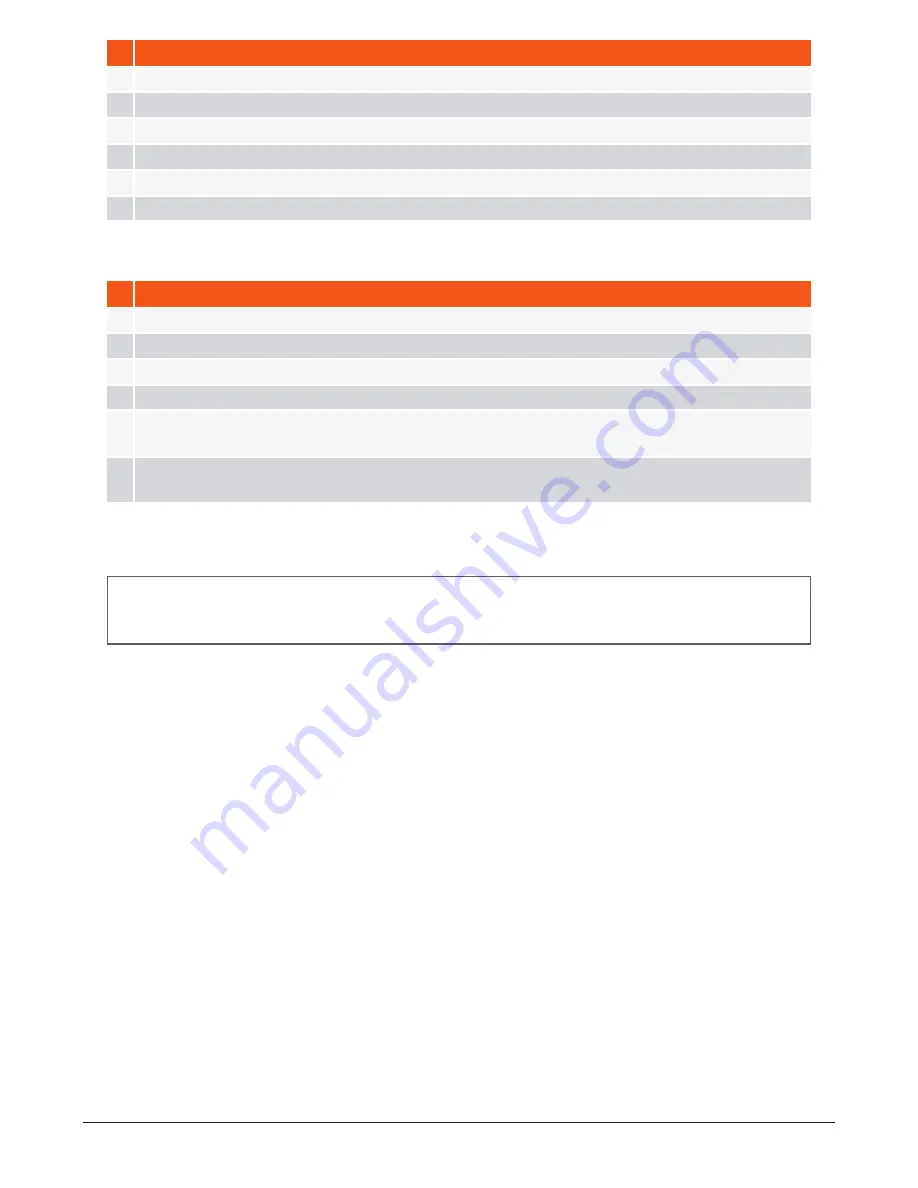
No Checkpoint prior to startup
5
Check the tension of chains, carrier belts, and chamber belts.
6
Check wrapping table sensors and table movement.
7
Leave the wrapping table in its middle position.
8
Look for oil leaks.
9
Check the oil temperature.
10 Check the levelling of the machine.
4.3.2 Checkpoints while baling
No Checkpoint prior to baling
1
Continuously observe all moving parts and functions.
2
Check the tracking of both chamber belts (leveling will affect the tracking).
3
Check the greasing pump function.
4
Check the chain lubrication system (Dry chains?).
5
Check the condition and cleaning of chamber rollers. Too much material on the rollers will affect the track-
ing of the chamber belts.
6
Avoid overfilling of the space between the elevator and sub conveyor. (Easily avoided by controlling the
material amount fed into the elevator).
4.4 BREAK-IN PERIOD
The first 50 hours of operation are considered to be the break-in period.
NOTE: Before the compactor is shipped from the factory, Orkel has performed a thorough quality control and
made a test run. The test run is done without any material. The need of some adjustments during first start
up is to be expected, depending on the material being baled.
4.4.1 Precautions during the break-in period
When the compactor is brand new, there are a couple of things that need special attention from the oper-
ator. The tensioning of the elevator chain must be checked and, if necessary, readjusted during the first
three hours of operation.
4.4.2 After the first 50 hours of operation
Change the oil, and all oil filters.
4 OPERATION
39
Summary of Contents for MP2000-X
Page 14: ...1 6 DECLARATION OF CONFORMITY 1 GENERAL 14...
Page 98: ...8 6 4 Gearbox and gears for hydraulic motors Gear oil Renolin unisyn CLP 220N 8 LUBRICATION 98...
Page 99: ...8 7 MANUAL LUBRICATION CHARTS 8 7 1 The compactor 8 LUBRICATION 99...
Page 100: ...8 7 2 Feed hopper F10 8 LUBRICATION 100...
Page 101: ...8 7 3 Telescopic drawbar 8 LUBRICATION 101...
Page 105: ...10 1 MAIN POWER SUPPLY E STOP SWITCHES AND ELECTRICAL CABINET 10 ELECTRICS 105...
Page 106: ...10 2 ELECTRICAL CABINET POWER SUPPLY RAIL 10 ELECTRICS 106...
Page 107: ...10 3 SENSORS AND MANUAL CONTROLS 10 ELECTRICS 107...
Page 108: ...10 4 VALVES FAN MOTORS AND PUMPS 10 ELECTRICS 108...
Page 120: ...10 9 SENSOR OVERVIEW 10 ELECTRICS 120...
Page 124: ...11 1 1 Complete diagram 11 HYDRAULICS 124...
Page 125: ...11 1 2 Wrapping table chamber and elevator control 11 HYDRAULICS 125...
Page 128: ...11 2 VALVE OVERVIEW 11 2 1 Valve chart for MP2000 X 11 HYDRAULICS 128...
Page 132: ...12 6 3 Dimensional sketch F10 operating mode 12 SPECIFICATIONS 132...
Page 133: ...12 6 4 Dimensional sketch F10 transport mode 12 SPECIFICATIONS 133...
Page 137: ...M Maintenance 13 65 67 INDEX 137...