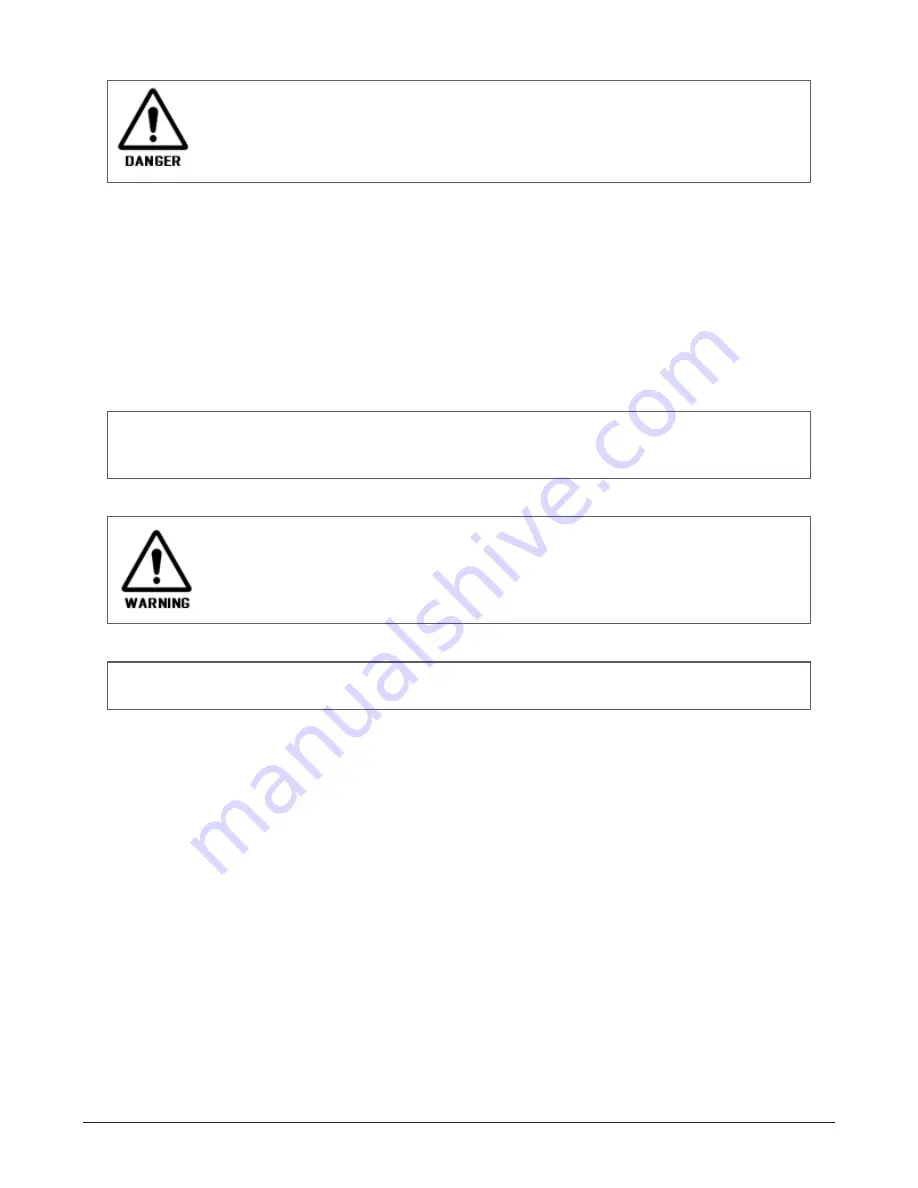
7.8 BALING CHAMBER
All repair and maintenance work inside the chamber is associated with great danger. Secure
the chamber door lifting cylinders, by closing the securing valves on both sides. The machine
must be stopped and PTO disconnected.
7.8.1 Inspection
Chamber - rollers - bearings - belts
The bale chamber must be checked frequently. Before performing a control, the chamber must be properly
cleaned, preferable using a high pressure washer. Check the tracking of the chamber belts and adjust if
needed.
Look for wear on the chamber sidewalls and check the condition of the rollers and rubber belts. The grade
of wear and tear are varying, depending on which material being baled.
Replace damaged rollers and belts if excessively worn. If there is excessive wear on the chamber sidewalls,
Hardox wear plates can be retrofitted on the chamber walls. Contact Orkel AS if relevant.
NOTE: The play in the slide bearings is at the smallest when the compactor is brand new. This may result in
increased temperature in the bearings. The bearings should therefore be checked as they might require addi-
tional lubrication.
During control and manual greasing of bearings and bushings the tractor/motor shall not be
running.
NOTE: In extreme cases of heating, a special filler nipple may be used (force lubricate) after removing the
hose from the bearing. Please contact Orkel if this is necessary.
7.8.2 Adjusting the front chamber belt
All adjustment of the belt tracking is done on the right side of the chamber (upper front roller). See
. The belt tracking should not touch the chamber side walls.
If the belt is tracking towards B (
), the distance C (
) must be increased. If the belt is
tracking against A (
) the distance C (
) must be reduced.
7 MAINTENANCE AND MECHANICAL ADJUSTMENTS
75
Summary of Contents for MP2000-X
Page 14: ...1 6 DECLARATION OF CONFORMITY 1 GENERAL 14...
Page 98: ...8 6 4 Gearbox and gears for hydraulic motors Gear oil Renolin unisyn CLP 220N 8 LUBRICATION 98...
Page 99: ...8 7 MANUAL LUBRICATION CHARTS 8 7 1 The compactor 8 LUBRICATION 99...
Page 100: ...8 7 2 Feed hopper F10 8 LUBRICATION 100...
Page 101: ...8 7 3 Telescopic drawbar 8 LUBRICATION 101...
Page 105: ...10 1 MAIN POWER SUPPLY E STOP SWITCHES AND ELECTRICAL CABINET 10 ELECTRICS 105...
Page 106: ...10 2 ELECTRICAL CABINET POWER SUPPLY RAIL 10 ELECTRICS 106...
Page 107: ...10 3 SENSORS AND MANUAL CONTROLS 10 ELECTRICS 107...
Page 108: ...10 4 VALVES FAN MOTORS AND PUMPS 10 ELECTRICS 108...
Page 120: ...10 9 SENSOR OVERVIEW 10 ELECTRICS 120...
Page 124: ...11 1 1 Complete diagram 11 HYDRAULICS 124...
Page 125: ...11 1 2 Wrapping table chamber and elevator control 11 HYDRAULICS 125...
Page 128: ...11 2 VALVE OVERVIEW 11 2 1 Valve chart for MP2000 X 11 HYDRAULICS 128...
Page 132: ...12 6 3 Dimensional sketch F10 operating mode 12 SPECIFICATIONS 132...
Page 133: ...12 6 4 Dimensional sketch F10 transport mode 12 SPECIFICATIONS 133...
Page 137: ...M Maintenance 13 65 67 INDEX 137...