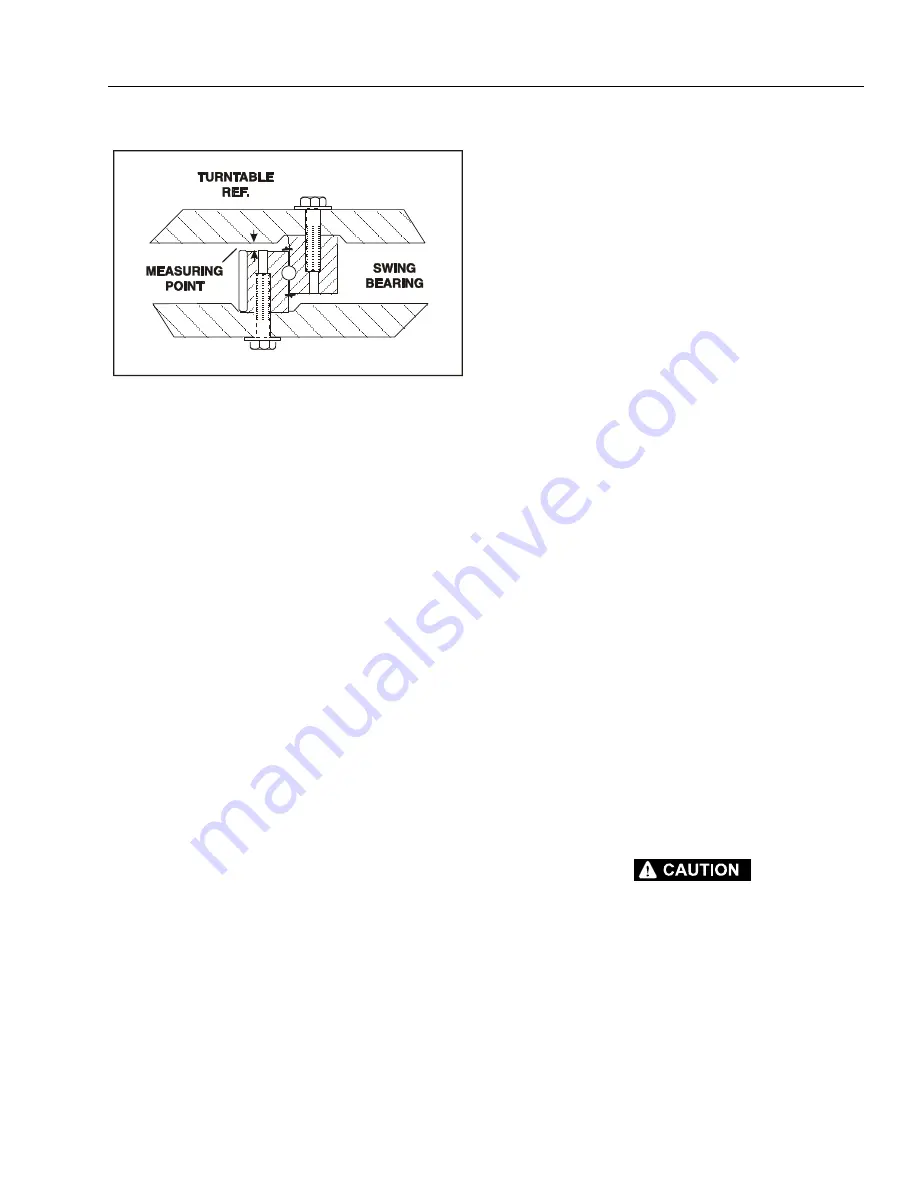
SECTION 3 - CHASSIS & TURNTABLE
3121827
– JLG Lift –
3-41
3.
If a difference greater than 0.057 in. (1.40 mm) is
determined, the swing bearing should be replaced.
4.
If a difference less than 0.057 in. (1.40 mm) is deter-
mined, and any of the following conditions exist, the
bearing should be removed.
a.
Metal particles in the grease.
b.
Increased drive power.
c.
Noise.
d.
Rough rotation.
5.
If bearing inspection shows no defects, reassemble
bearing and return to service.
Replacement of Swing Bearing
1.
Removal.
a.
Attach an adequate support sling to the boom
and draw all slack from sling. Prop or block the
boom if feasible.
b.
Tag and disconnect hydraulic lines running
through center of turntable and frame. Use a
suitable container to retain any residual hydrau-
lic fluid. Cap lines and ports.
c.
Attach suitable overhead lifting equipment to the
base of turntable weldment.
d.
Use a suitable tool to scribe a line on the inner
race of the swing bearing and on the underside
of the turntable. This will aid in aligning the bear-
ing upon installation. Remove bolts, nuts and
washers which attach the turntable to the bear-
ing inner race. Discard nuts and bolts.
e.
Use the lifting equipment to carefully lift the com-
plete turntable assembly from the bearing.
Ensure that no damage occurs to the turntable,
bearing or frame mounted components.
f.
Carefully place the turntable on a suitably sup-
ported trestle.
g.
Use a suitable tool to scribe a line on the outer
race of the swing bearing and the frame. This
line will aid in aligning the bearing upon installa-
tion. Remove the bolts and washers which
attach the outer race of the bearing to the frame.
Discard the bolts. Use suitable lifting equipment
to remove the bearing and rotation box assem-
bly from the frame; move to a clean, suitably
supported work area.
h.
Remove the two capscrews securing the bear-
ing to the rotation box to separate the two for
inspection.
2.
Installation.
a.
Install bearing to rotation box with two cap-
screws, so that fill plug of bearing is as close to
gear as bolt pattern will allow. Do not tighten
capscrews.
b.
Line up high spot (blue) of bearing with center
tooth of worm gear. Set backlash to 0.008 -
0.010 inch (0.20 - 0.25 mm). Tighten capscrews
as shown in Figure 3-15., Swing Bearing Torqu-
ing Sequence.
c.
Apply Tribol Molub-Alloy 936 Open Gear Com-
pound to bearing and worm gear teeth.
d.
Grease bearing with Mobilith SHC Bearing
Grease. Grease fitting is on inside wall of inner
race of bearing.
NOTE:
If Tribol Molub-Alloy 936 Open Gear Compound or
Mobilith SHC Bearing Grease are not available,
Multi-Purpose Grease (MPG) can be substituted,
however the service interval will be shorter.
e.
Using suitable lifting equipment, install bearing/
rotation box assembly to frame with soft spot
(red) 90 degree relative to load axis. If reusing
old bearing, ensure that scribed line of outer
race of the bearing aligns with the scribed mark
on the frame.
JLG INDUSTRIES RECOMMENDS THAT ALL REMOVED GRADE 8
BEARING NUTS AND BOLTS BE DISCARDED AND REPLACED
WITH NEW NUTS AND BOLTS. SINCE THE SWING BEARING IS
THE ONLY STRUCTURAL LINK BETWEEN THE FRAME AND TURN-
TABLE, IT IS IMPERATIVE THAT SUCH REPLACEMENT HARD-
WARE MEETS JLG SPECIFICATIONS. USE OF GENUINE JLG
HARDWARE IS HIGHLY RECOMMENDED.
f.
Apply a light coating of Loctite 271 to the new
bearing bolts and loosely install the bolts and
washers through the frame and outer race of
bearing.
Figure 3-14. Swing Bearing Tolerance Measuring Point
Summary of Contents for JLG E400AJP
Page 2: ......
Page 32: ...SECTION 1 SPECIFICATIONS 1 18 JLG Lift 3121827 NOTES...
Page 42: ...SECTION 2 GENERAL 2 10 JLG Lift 3121827 NOTES...
Page 54: ...SECTION 3 CHASSIS TURNTABLE 3 12 JLG Lift 3121827 Figure 3 3 Speed Sensor Orientation...
Page 60: ...SECTION 3 CHASSIS TURNTABLE 3 18 JLG Lift 3121827 Figure 3 7 Steering Components and Spindles...
Page 62: ...SECTION 3 CHASSIS TURNTABLE 3 20 JLG Lift 3121827 Figure 3 9 Tilt Sensor Location...
Page 86: ...SECTION 3 CHASSIS TURNTABLE 3 44 JLG Lift 3121827 Figure 3 16 Swing Components...
Page 88: ...SECTION 3 CHASSIS TURNTABLE 3 46 JLG Lift 3121827 Figure 3 18 Battery Cable Connections...
Page 90: ...SECTION 3 CHASSIS TURNTABLE 3 48 JLG Lift 3121827 Figure 3 20 On Board Generator...
Page 97: ...SECTION 3 CHASSIS TURNTABLE 3121827 JLG Lift 3 55 Figure 3 22 Generator Components...
Page 116: ...SECTION 3 CHASSIS TURNTABLE 3 74 JLG Lift 3121827 NOTES...
Page 127: ...SECTION 4 BOOM PLATFORM 3121827 JLG Lift 4 11 Figure 4 10 Boom Limit Switches...
Page 140: ...SECTION 4 BOOM PLATFORM 4 24 JLG Lift 3121827 Figure 4 13 Rotator Counterbalance Valve...
Page 178: ...SECTION 5 HYDRAULICS 5 24 JLG Lift 3121827 Figure 5 26 HydraForce Cartridge Torque Value Chart...
Page 214: ...SECTION 6 JLG CONTROL SYSTEM 6 34 JLG Lift 3121827 NOTES...
Page 257: ......