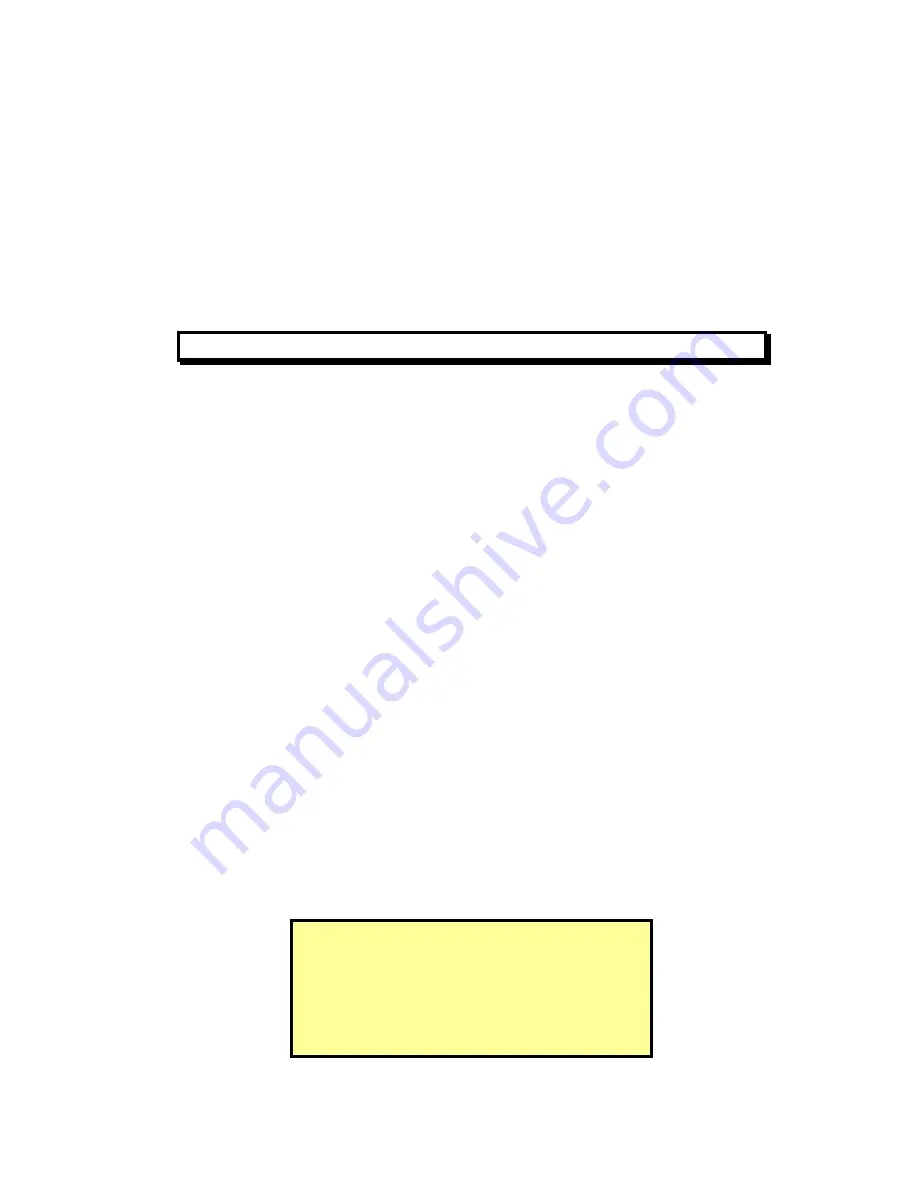
Optical Scientific Inc
OFS 2000CW User’s Guide
P/N 1910-905
Rev. 03/28/13
56
NOTE:
It may be necessary to remove and/or
replace circuit boards.
These boards are NOT "hot swap".
Power to the system must be shut OFF before
removing and/or replacing circuit boards.
11 Troubleshooting
If there is a problem, fault or malfunction, you first have to identify what it is, where it is and then what it is
caused by, before you can correct it. Some of the following sections can help you complete these steps.
11.1 General Troubleshooting Guidelines
If there is a suspected problem with a component and you have spares or a spare system, change out large
components one at a time such as the controller , transmitter, receiver, receiver cable etc, until you have
isolated which component the problem is in. Once isolated to a large component you can continue changing
out smaller and smaller components until you have identified exactly where the problem resides.
OSI strongly recommends the purchase of spare components.
For what seem to be small glitches or lock-ups, cycle the power.
For a quick check to prove the LED is on (and windows clear), remove the receiver module from the mounting
stand and look back through the hole that will be left in the stand, towards the LED
If you cannot see a clear image of the detector board when aiming the LED then it is wise to take the heads
right off to inspect the windows from the other side and the ports for obstruction or dirt buildup.
Sometimes stack/duct gases cool in the nozzles and spool pieces and create fog and mist, which can weaken
the correlation. To see if mist is forming, keep the heads installed and use a small bright Maglite™ or similar
flashlight from the transmitter side and look into the nozzle through the transmitter window by looking at all
possible angles around the LED module. Carefully look from far down the interior of the pipe near the stack
wall location right up to the window. It sometimes takes some patience and time for your eye to adjust and to
get the right angle of the flashlight. If mist formation is noticeable, try increasing the purge to drive it out of the
nozzle.
If there are unusual lock-ups or behavior sometimes it may be a poor connection on the receiver cable. Unplug
the receiver cable, blow out and clean off the connectors and re-connect it
If a problem is very perplexing, take the heads down to a bench and set up the system with the controller on
the bench. Use a small hair dryer for the airflow and test that the system works.
If the air flow is extremely moist / wet, then condensed water will pool in the bottom of the spool piece. In this
case drill a ¼ inch hole at the bottom of the spool piece about 1 inch away from the process side. This weep
hole will allow the water to drain.
If (after consulting with OSI Tech Support) it is determined that there is a problem with a circuit board. You
may order a replacement from OSI. Operating firmware or DSP software are not field replaceable or
upgradeable unless done by OSI or OSI-approved personnel. The circuit boards must be returned to OSI for
this operation to be performed.