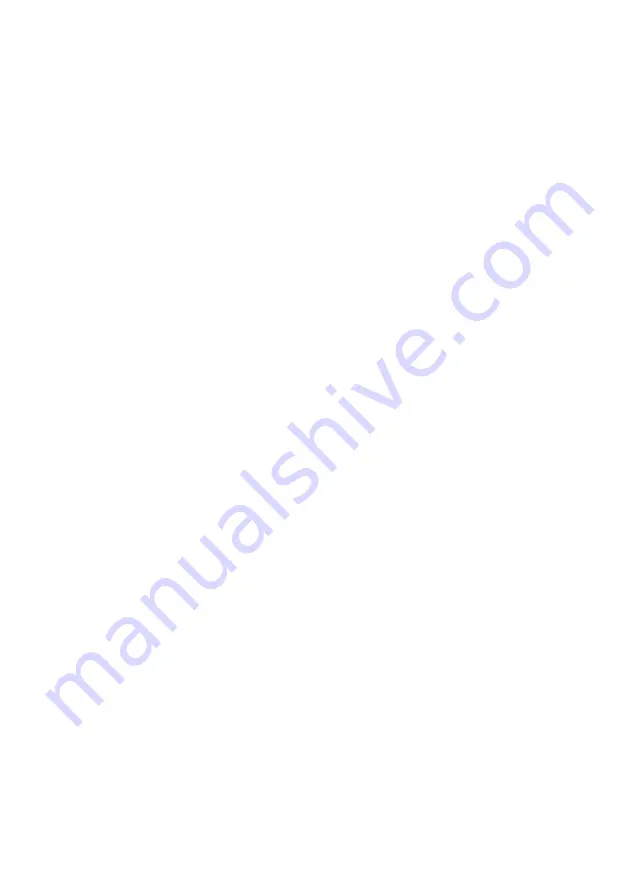
16
5. SAFETY AND SERVICING
Maintenance must be carried out by a compe-
tent person.
5.1 Safety cut out
1. The safety cut-out operates if:
a. Wiring is incorrect.
b. The immersion heater thermostat or
cylinder thermostat fails.
2. Remember before resetting the safety cut-
out or altering the thermostat setting, isolate
electrical supply to the unit prior to removal
of the electrical box lid
3. Reduce thermostat setting an press the re-
set button. After adjustments are completed,
ensure the lid to the electrical box is replaced
correctly and the retaining screw is fitted
4. If still out of operation, contact installer.
5.2 Intermittent or slow discharge from tundish
1. Turn off the electrical supply to the immer-
sion heaters.
2. Turn off cold water supply valve.
3. Open a hot tap.
4. Turn the knob on the Temperature and
Pressure Relief Valve (C) to the left and hold
in this position for 30 seconds
5. Check pre-charge on vessel and adjust
pressure if necessary.
6. Open cold water supply valve.
7. When water flows through open tap, close
tap. Turn on electrical supply to the immer-
sion heaters.
5.3 Continous very hot water discharge from
tundish
This indicates a malfunction of a thermal cut-out,
operating thermostat or the combined tempera-
ture and pressure relief valve. Turn off the electri-
cal supply to the immersion heater and also iso-
late an indirect unit from the boiler. Contact the
installer or competent engineer.
5.4 Expansion vessel maintenance
The expansion vessels do not require annual
maintenance and should not be tampered with
unless an intermittent or slow discharge from the
tundish occurs when water is being heated. In this
situation, maintenance must be carried out by a
competent person and the precharge pressure
must be restored to the original value. An annual
visual inspection is recommended.
Important: to check the precharge the expansion
vessel must be completely empty of water. if the
pressure is different from the value shown on the
label it must be restored to the original value.
Do not remove expansion vessel without depres-
surising the cylinder and draining 10 litres of water
from the drain valve at the base of the cylinder
5.5 Guarantee
Cylinder should be serviced annually (as below)
and logbook should be updated in order to vali-
date guarantee. Logbook and service records act
as guarantee document. For terms of guarantee
see Service logbook at rear of manual.
5.6 Service procedure
The following maintenance work has to be carried
out annually by a competent person:
1. Inspection of pressure/temperature relief
valve and expansion relief valve.
2. Manually operate each valve by twisting the
operating cap, and check if water flows un-
obstructed via the tundish to the discharge
point.
3. Ensure that both valves re-seat satisfactorily.
4. Visual inspection of expansion vessel.
5. If the pressure is below 3.0 bar, top up with
suitable air pressure pump to pressure on
vessel label.
6. Complete the service section of Benchmark/
Cylinder Commissioning Checklist included
in the inside back pages of these instructions.
7. Remove , clean and replace line strainer.
8. The immersion heater element must be
removed for inspection on service after 5
years. The threads must be checked for cor-
rosion. If signs of corrosion are evident, the
element must be replaced. Subsequently
the element must be removed and exam-
ined every 3 years. Failure to do so in ar-
eas of aggressive water may result in the
element separating from the cylinder with
consequential escape of water.
9. Visual inspection of valves, external fittings,
immersion heaters and electrical connec-
tions.
5.7 Combination valve
The combination valve can be separated into two
sections by disconnecting the compression fitting
in the middle. The entire valve can be removed by
unscrewing from the top connection. When refit-