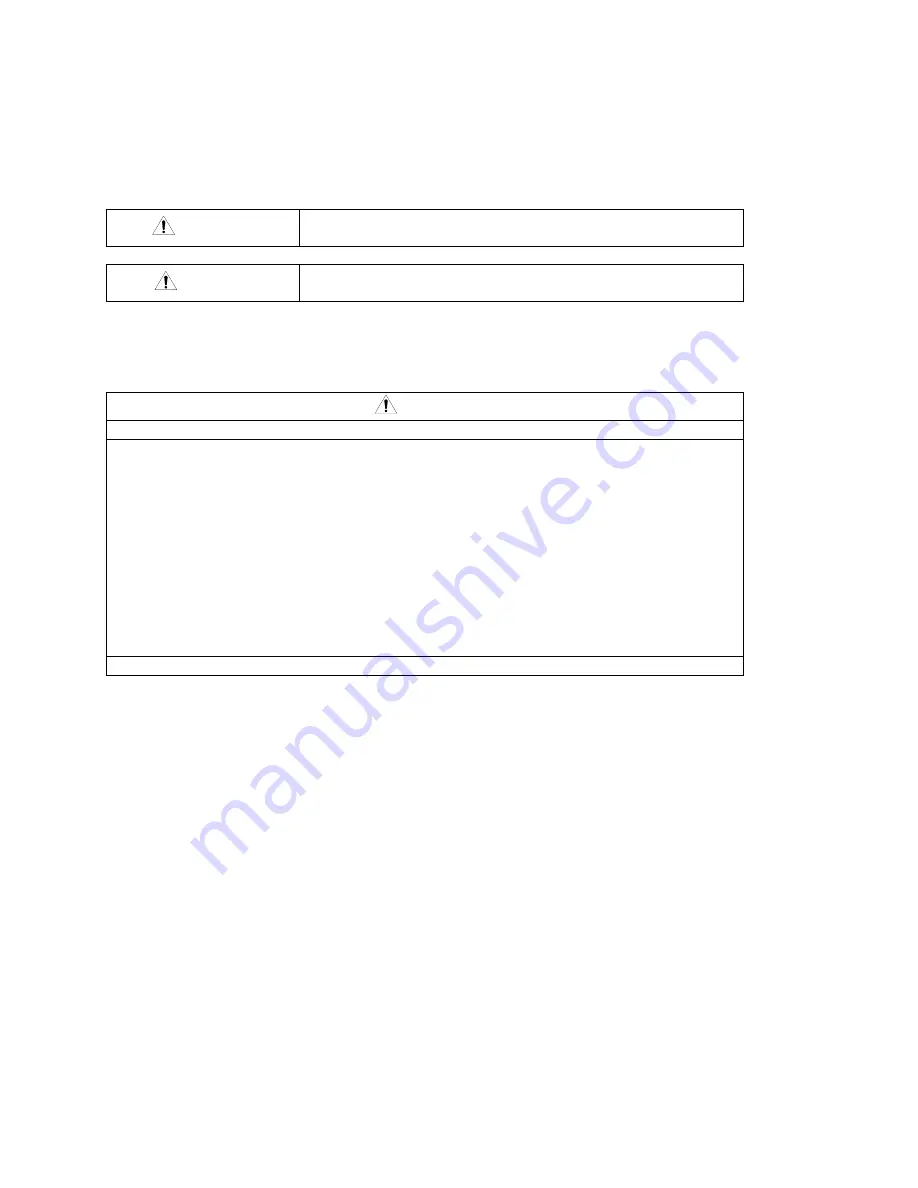
―E2―
1. SAFETY INFORMATION
The following safety alert symbols and signal words are used throughout this manual to identify
various hazards and special instructions.
WARNING
WARNING gives information regarding possible personal injury
or loss of life.
CAUTION
CAUTION refers to minor personal injury or possible equipment
damage.
2. ARC WELDING SAFETY PRECAUTIONS
WARNING
ARC WELDING can be hazardous.
1. PROTECT YOURSELF AND OTHERS FROM POSSIBLE SERIOUS INJURY OR DEATH.
Be sure to:
・
・
・
・
Keep children away.
・
・
・
・
Keep pacemaker wearers away until consulting a doctor.
2. Read and understand the summarized safety information given below and the original
principal information that will be found in the PRINCIPAL SAFETY STANDARDS.
3. Have only trained and experienced persons perform installation, operation, and
maintenance of this equipment.
4. Use only well maintained equipment. Repair or replace damaged parts at once.
ARC WELDING is safe when precautions are taken.