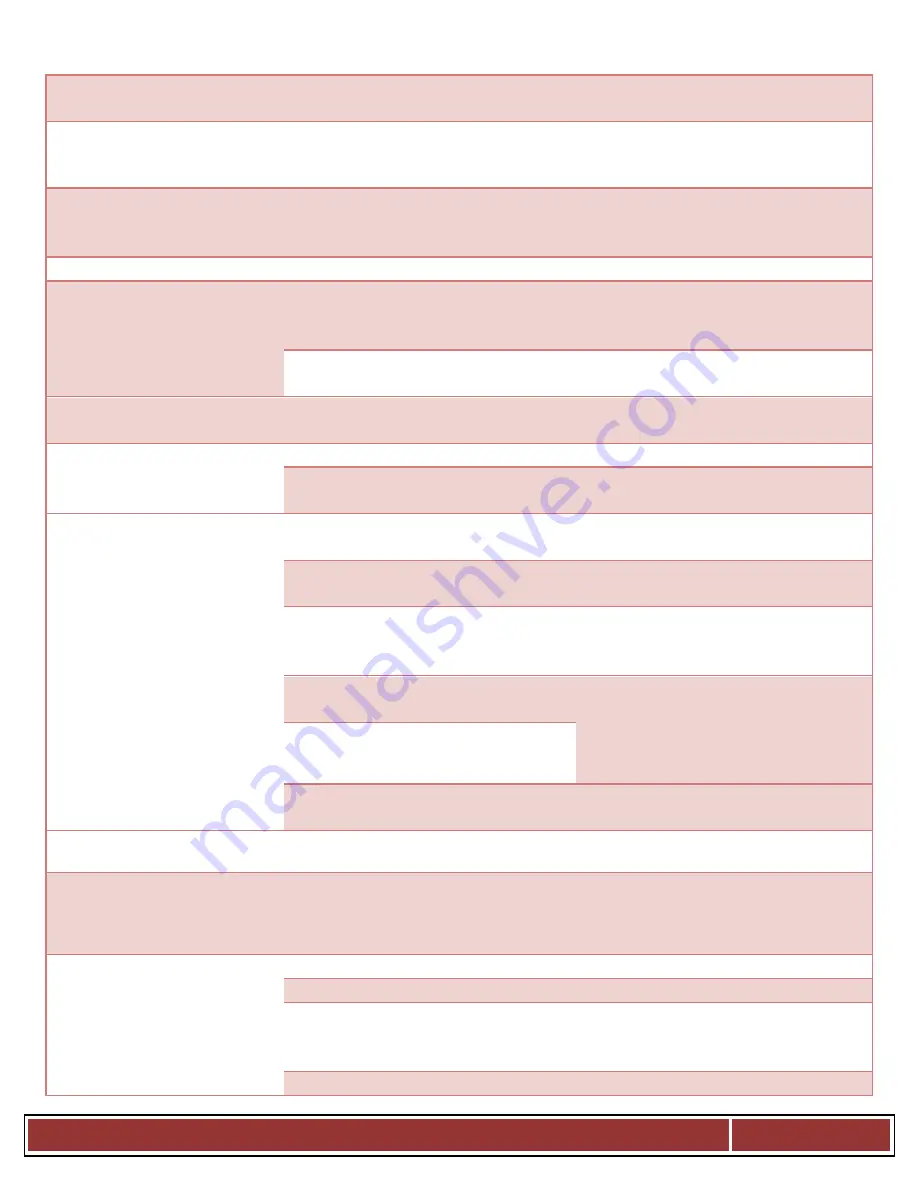
F o r m X X X X : R e v i s e d A u g u s t , 2 0 1 5
Page 22
F_cFt
Forced Translation fault An EPM from an old drive put into a new
drive
Press [M] (mode button) twice to reset
F_dbF
Dynamic Braking fault
Dynamic braking resistors are
overheating
Increase active decel time (P105, P126,
P127), Check main voltage and P107
F_EF
External fault
P121-P124 = 21 and that digital input
has been opened, P121-P124 = 22 and
that digital input has been closed
Correct the external fault condition,
Make sure digital input is set properly for
NC or NO circuit
F_F1
EPM fault
EPM missing or defective
Power down and replace EPM
F_Fnr
Control Configuration
fault
The drive is setup for REMOTE KEYPAD
control (P100 = 2 or 5) but is not set up
for network communication
Set P400 = 1 or P600 = 1
4-20mA signal (at TB-25) drops below
the value set in P164
Set P400 or P600 to a valid network
communications protocol selection
F_GF
OEM Defaults data fault
Drive is powered up with P199 = 1 and
OEM settings in the EPM are not valid
Install an EPM containing valid OEM
defaults data or change P199 to 0
F_HF
High DC Bus Voltage
fault
Mains voltage is too high
Check main voltage and P107
Decel time is too short, or too much
regen from the motor
Increase decel time (P105, P126, P127) or
install Dynamic Braking option
F_IL
Digital Input
Configuration fault
(P121-P124)
More than one digital input set for the
same function
Each setting can only be used once
(except setting 0 and 3)
Only one digital input configured for
MOP function (up, Down)
One input must be set to MOP up,
another must be set to MOP down
PID mode is entered with set point
reference and feedback source set to the
same analog signal
Change PID set point reference (P121-
P124 or feedback source (P201)
One of the digital inputs (P121-P124) is
set to 10 and another is set to 11-14
Reconfigure digital inputs
One of the digital inputs (P121-P124) is
set to 11 or 12 and another is set to 13-
14
PID enabled in Vector Torque mode
(P200 = 1 or 2 and P300 = 5)
PID cannot be used in Vector Torque
mode
F_LF
Low DC Bus Voltage
fault
Main voltage is too low
Check main voltage
F_nId
No Motor ID fault
An attempt was made to start the drive
in Vector or Enhanced V/Hz mode prior
to performing the Motor Auto-
Calibration
Refer to parameters P300-P399 for Drive
Mode setup and calibration
F_OF
Output fault: Transistor
fault
Output short circuit
Check motor/motor cable
Acceleration time too short
Increase P104, P125
Severe motor overload due to:
Mechanical problem, Drive/motor too
small for application
Check machine/system, Verify
drive/motor are proper size for
application
Boost values too high
Decrease P168, P169
Summary of Contents for PR4,6/SS49
Page 11: ...F o r m X X X X R e v i s e d A u g u s t 2 0 1 5 Page 11 ...
Page 12: ...F o r m X X X X R e v i s e d A u g u s t 2 0 1 5 Page 12 ...
Page 14: ...F o r m X X X X R e v i s e d A u g u s t 2 0 1 5 Page 14 ...
Page 15: ...F o r m X X X X R e v i s e d A u g u s t 2 0 1 5 Page 15 ...
Page 16: ...F o r m X X X X R e v i s e d A u g u s t 2 0 1 5 Page 16 ...
Page 17: ...F o r m X X X X R e v i s e d A u g u s t 2 0 1 5 Page 17 ...
Page 18: ...F o r m X X X X R e v i s e d A u g u s t 2 0 1 5 Page 18 ...
Page 19: ...F o r m X X X X R e v i s e d A u g u s t 2 0 1 5 Page 19 ...