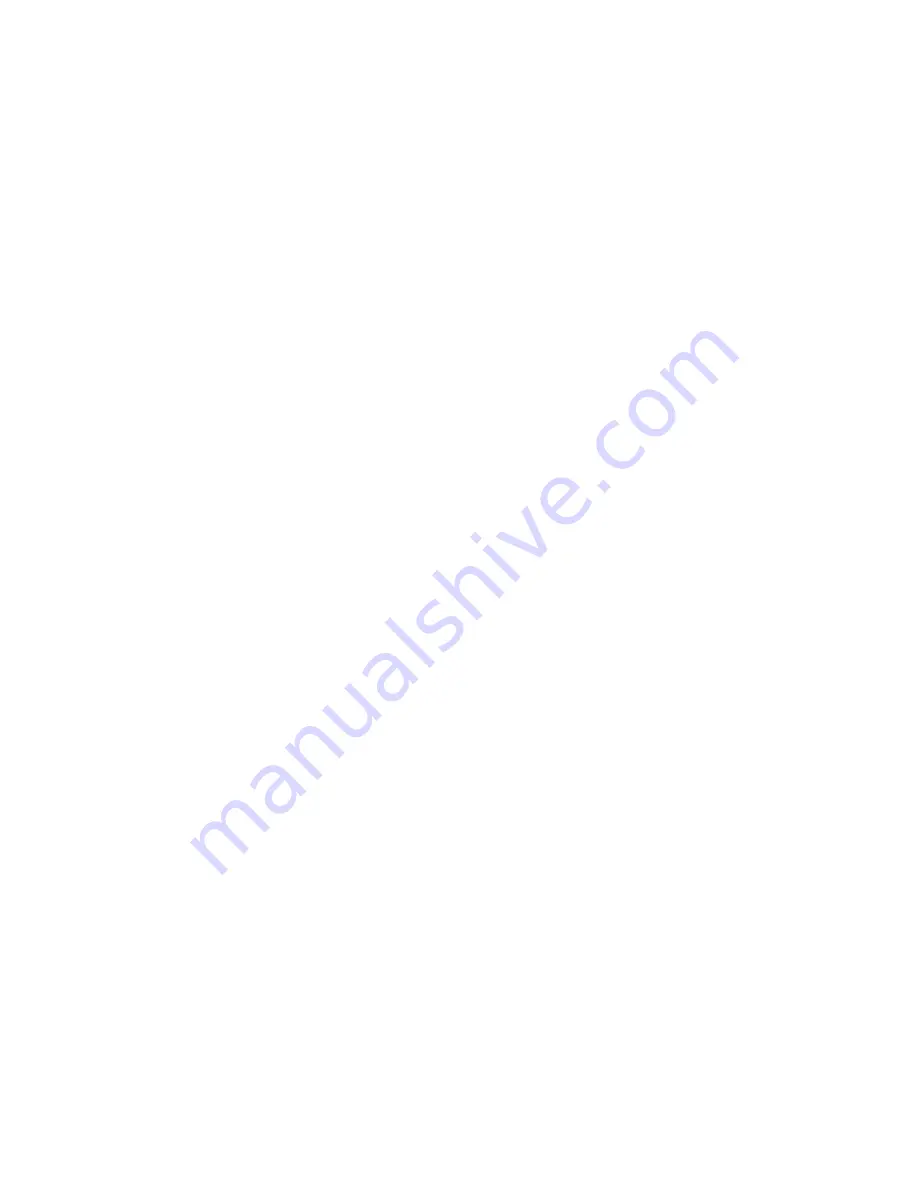
26
WINCH ASSEMBLY
Replace the seals in winch drum and closure and replace
all o-rings
.
The procedure below assumes the planet carrier and
overrunning clutch subassemblies are built. Refer to
planet carrier and overrunning clutch subassembly
instructions if needed
.
1. Prepare for installing bearing support (1) into support
end side plate (20) by placing side plate on a work
table and using wood blocks to make clearance for
the bearing support. Lower bearing support into side
plate with the vent at the 12 O’clock position. Install
bolts (22) and lockwashers (30). Torque bolts to 110
± 5 ft-lbs. The bolts can be torqued after the sideplate
is bolted to the base angles if more leverage is need-
ed
.
2. Place base angles on the ground aligned for assem-
bly. The 5/8 tapped holes for the band brake hard-
ware are on the motor end support. Install support
end side plate (20) in the base angles. The guard
bracket will attach at the upper inboard bolt on both
base angles
.
3. Stand support end sideplate and base angles assem-
bly on end with support end side plate down. A 2 x 4
should be placed under the side plate just above the
bearing support to level the assembly
.
4. Install drain plug in the winch drum. Apply general
purpose grease to the bearing support seal and bear-
ing surfaces, and ensure the seal and bearing are
installed in cable drum. Lift the cable drum and lower
slowly onto the bearing support using the clamps
shown (Wes has drawing) taking care not to damage
the seal
.
5. Install the output planet carrier assembly (400) onto
the bearing support shaft. Ensure the carrier splines
engage on the output shaft. Install the output carrier
thrust washer (5), and output sun gear (6)
.
6. Install the ring gear (13). Install the second planet
carrier assembly ensuring the thrust washer (5)
remains in position and the splines engage with the
output sun gear splines
.
7. Install second sun gear (8) and thrust washer (5)
.
8. Install the primary planet carrier assembly again
ensuring the thrust washer (5) remains in position and
the carrier splines engage with the second sun gear
.
9. Install the thrust washer (34) into the primary planet
carrier and install the primary sun gear (7)
.
10. Apply general purpose grease to the drum closure o-
ring (11) and install the drum closure into the winch
drum.
11. Bolt the motor end side plate to base angles. The
guard bracket will attach at the upper inboard bolt on
the base angle.
12. Apply general purpose grease to the bearing and seal
surfaces on the brake cylinder and drum closure.
Slowly lower the brake cylinder into the side plate tak-
ing care not to damage the drum closure seal, and
position with the brake release fitting at the 6 o’clock
position. Apply Loctite 242 to the capscrews (219)
and torque to 110 ± 5 ft•lbs
.
13. Place the spring spacer (210) and twelve brake
springs (203) in the brake cylinder. Place the pres-
sure plate (202) on top of the brake springs
.
14. Install the brake discs on the pressure plate. The
brake plate (204) is first followed by a friction disc
(205) and alternating. There will be four brake plates
and three friction discs
.
15. Install the three brake release pins (221) in the brake
cylinder aligning them with the notches in the brake
plates
.
16. Before installing the sprag clutch, check position for
installation: While holding the outer race, the inner
race should turn freely in the clockwise direction
.
17. Ensure sprag clutch inner race retaining ring is prop-
erly seated and install the sprag clutch aligning inner-
race splines with the sun gear (7) and outer race
splines with the friction plates. Ensure the inner-race
retaining ring is seated against the sun gear (7). After
installing, correct installation should be checked by
turning the inner race in the clockwise direction –
ensure the outer race is not turning
- and observ-
ing the drum turning in the counter-clockwise (hoist)
direction. If the drum turns in the clockwise (lowering)
direction, remove the sprag clutch. Turn the sprag
clutch 180º reinstall and recheck
.
18. Apply general purpose grease to the o-rings on the
brake piston (202). Set the brake piston on the brake
cylinder and tap evenly around the circumference with
a rubber mallet to install
.
19. Set the motor adapter on the brake cylinder and align
bolt holes. Ensure the motor bolt holes are aligned so
the control valve will be at the 12 o’clock position
when the motor is mounted. Apply Loctite 242 to cap-
screws and tighten evenly one turn each in a cross
pattern until the motor adapter is seated. Torque the
capscrews to 110 ± 5 ft-lb
.
Summary of Contents for BRADEN BA5A
Page 2: ......
Page 25: ...23 THIS PAGE INTENTIONALLY LEFT BLANK...
Page 26: ...24 WINCH CROSS SECTION...