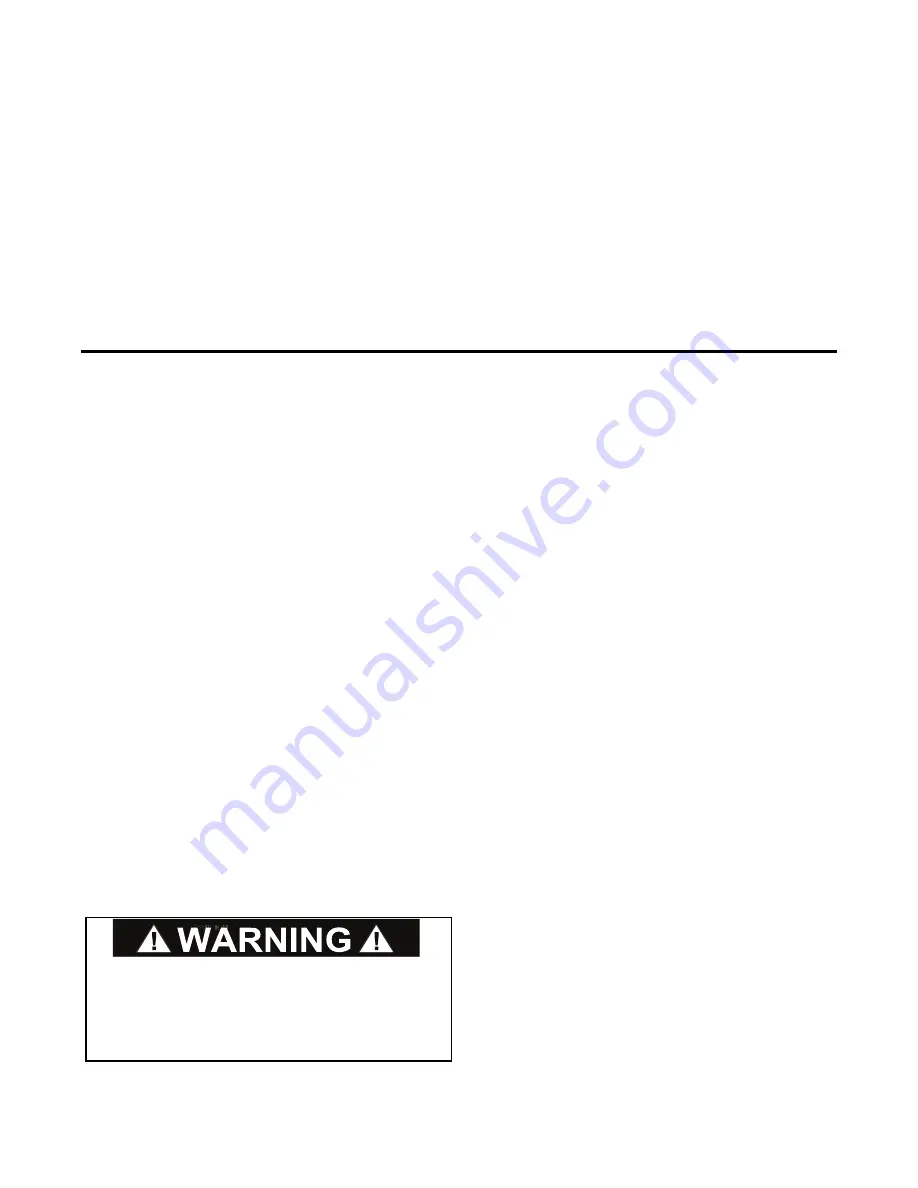
Tear-down Inspection
Any hoist that has not been subjected to regular oil
sample analysis should undergo a tear-down inspection
every 24 months. Also, if a hoist has an unknown histo-
ry of repair and/or maintenance, the hoist should under-
go a tear-down inspection prior to being placed into
service.
A tear-down inspection of the hoist should include the
complete disassembly, cleaning, inspection and
replacement of all worn, cracked, corroded or distorted
parts such as pins, bearings, shafts and brake compo-
nents. All seals and o-rings should be replaced during a
tear-down inspection. Always use new Spirol pins in the
planet gear shafts.
Any deficiency must be corrected immediately.
Before placing the hoist back in service, the rebuilt hoist
must be pull tested to the rated load of the hoist with a
dynamometer or equivalent measuring device. The
hoist should be dynamically tested by rotating the drum
several times, in both raising and lowering directions,
while under load of at least 30% of the hoist rated lifting
capacity. Check for smooth, quiet operation during this
procedure.
15
Proper oil sampling and analysis of the sample, is a
vital part of a comprehensive preventive maintenance
program. Information obtained from the oil analysis is
best utilized in conjunction with a regular program of
preventive maintenance. The early warning of abnor-
mal wear provided by an analysis program allows the
user to substitute preventive maintenance for a far
more costly and dangerous failure that may lead to loss
of load control that could result in property damage,
personal injury or death. Early detection of accelerated
component wear allows the scheduling of corrective
maintenance and can reduce in-operation failures and
costly down time.
Taking a Valid Oil Sample
Prepare the hoist by cleaning the drain area and drain
extension tube in order to obtain an uncontaminated
sample. Operate the hoist in both directions for one to
two minutes and then take the oil sample from the drain
port as soon as possible. Do not take the sample from
the first oil out of the drain port. Take a sample from the
mid-stream flow of the oil to obtain an accurate repre-
sentation of the oil condition. After taking an oil sample,
refill hoist with recommended lubricant.
Analysis
General Guide Lines
(After approximately 250 hours of operation)
Note:
The first oil change usually contains more “wear
metals”. Following the initial break-in period, the wear
metal levels should stabilize at a lower number.
Iron Contaminates
100 to 500 ppm
Normal
501 to 800 ppm
Caution – Abnormal Sample (moni-
tor more frequently), tear-down
inspection may be required.
801 ppm & up
Unacceptable – Abnormal Sample
(tear down inspection required)
In all contaminate monitoring, equally important as the
level of contamination, is the change in the amount of
contamination compared to previous samples.
Moisture contamination will lead to the formation of
acids that damage all internal components. Silica found
in the oil typically indicates “dirt” and contaminated
lubricant supply or poor maintenance practices.
OIL SAMPLING AND ANALYSIS
Hot oil may cause personal injury and/or burns to
unprotected skin. Make certain the oil has cooled to
a safe temperature (less than 110°F or 43°C) before
taking an oil sample, changing oil or servicing the
hoist.