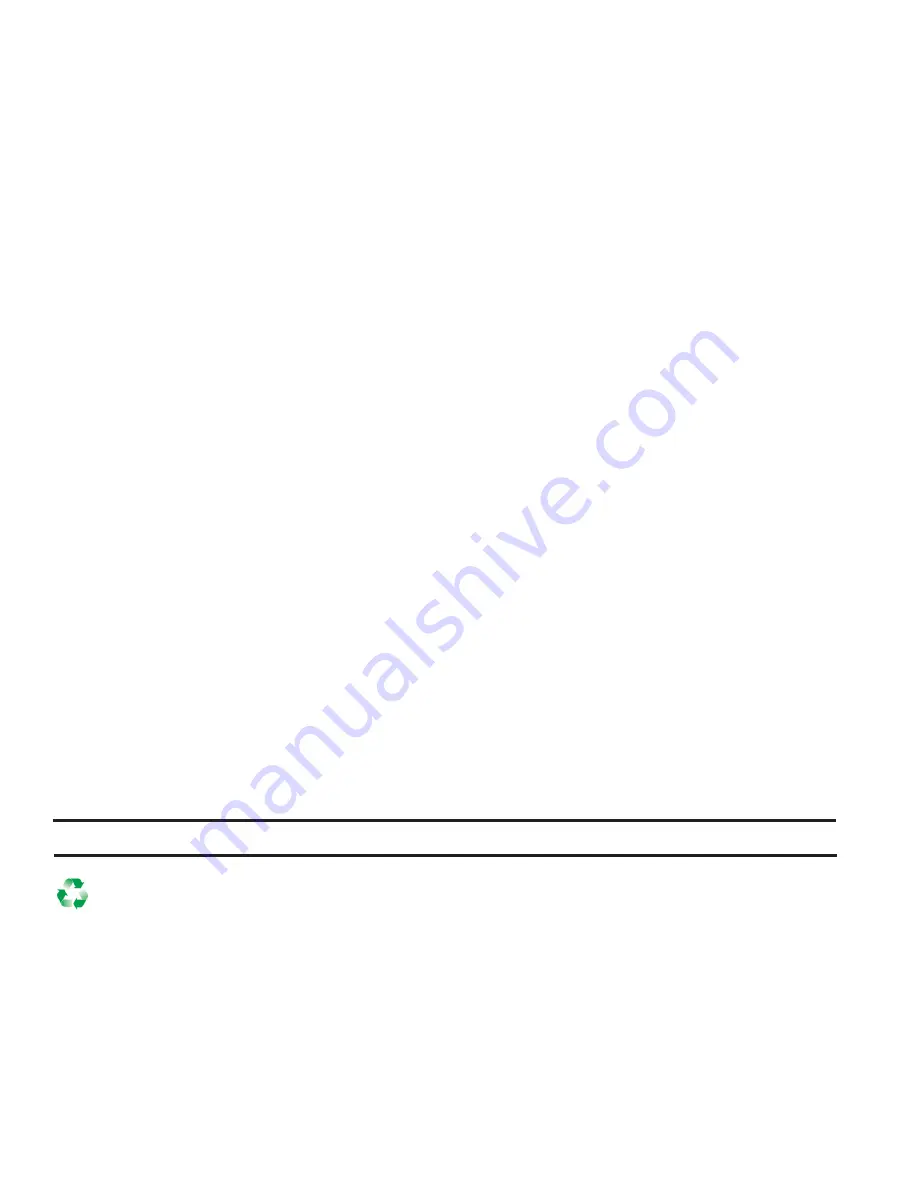
2
Table of Contents
Foreword ..................................................................................................................... 2
Model Identification ..................................................................................................... 3
Explanation of Model Number ..................................................................................... 4
General Safety Recommendations ............................................................................. 4
Theory of Operation .................................................................................................... 6
Preventive Maintenance ............................................................................................ 10
Specifications ............................................................................................................ 11
Recommended Planetary Gear Oil ........................................................................... 12
Wire Rope Installation ............................................................................................... 13
Troubleshooting ......................................................................................................... 14
H200 Major Parts Groups Cross-section .................................................................. 19
H200 Major Parts Groups Components .................................................................... 20
Service Precautions .................................................................................................. 20
Winch Removal and Installation ................................................................................ 21
Winch Disassembly ................................................................................................... 22
Primary Planet Carrier Service .................................................................................. 28
Secondary Planet Carrier Service ............................................................................. 29
Third Planet Carrier Service ...................................................................................... 30
Output Planet Carrier Service ................................................................................... 31
Drum Clutch Assembly Service ................................................................................. 32
Brake Assembly Service ........................................................................................... 34
Brake Assembly Pressure Test ................................................................................. 35
Brake Valve Service .................................................................................................. 36
Overrunning Clutch Service ...................................................................................... 38
Cable Drum Service .................................................................................................. 39
Winch Assembly ........................................................................................................ 41
Brake Cylinder Lifting Fixture .................................................................................... 47
FOREWORD
Managing Waste
PACCAR Winch believes in a life-cycle approach to our products. We encourage best practices regarding “Going
Green” — making environmentally responsible decisions to “reduce, reuse, and recycle.”
• At the end of the winch’s useful life, it is highly recommended to drain and recycle any oil remaining in the equipment.
•
Please use a metal recycler for winch disposal to reduce landfill waste.
The U.S. Environmental Protection Agency has developed required practices, called “management standards,” for busi-
nesses that handle used oil and metal wastes. Specific guidelines are available at the EPA and API Web sites as well
as your state’s environmental agency Web site:
• https://www.epa.gov/
• http://recycleoil.org/