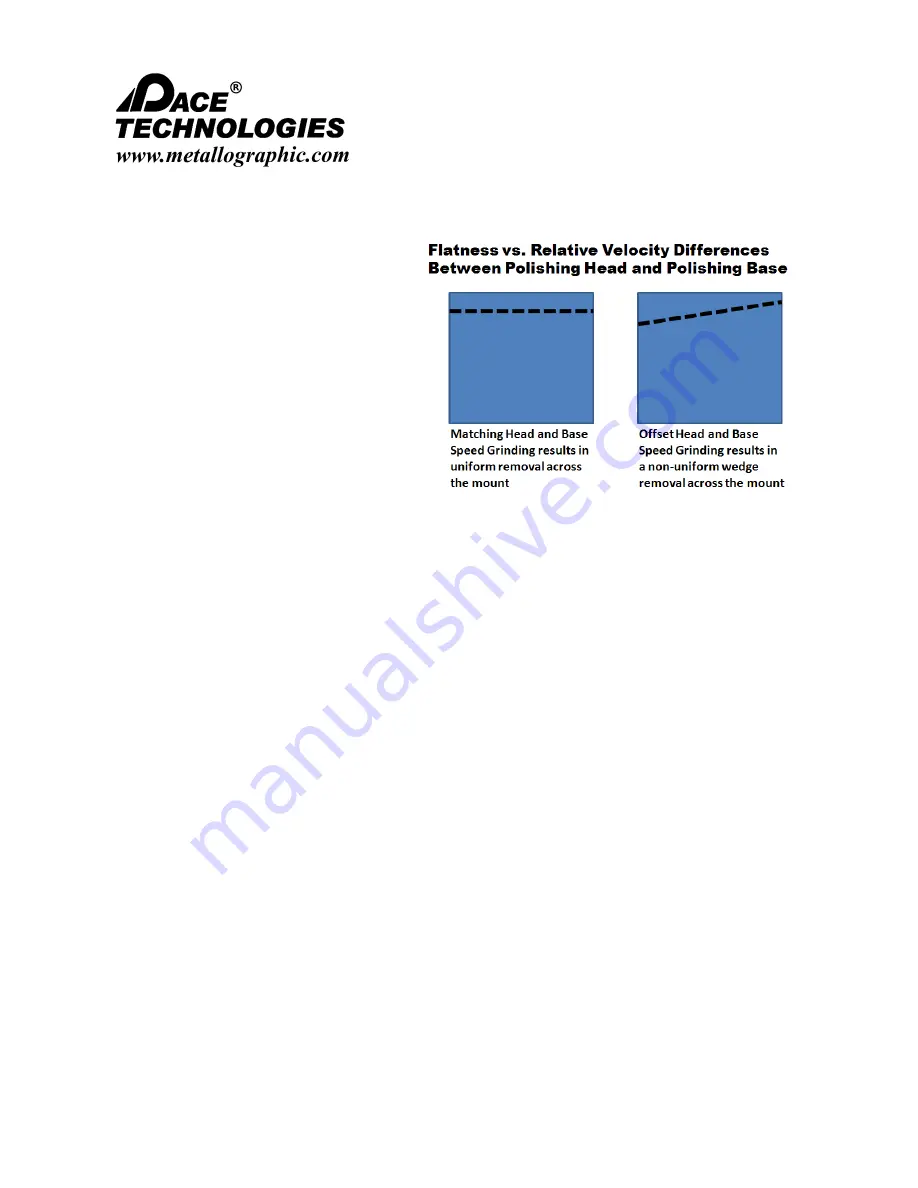
- - - - - - - - - - - - - - - - - - - - - - - - - - - - - - - - - - - - - - - - - - - - - - - - - - ▲
I
NSTRUCTION
M
ANUAL
3601 E. 34th St. Tucson, AZ 85713 USA Tel. +1 520-882-6598 Fax +1 520-882-6599 email: pace@metallographic.com Web: http://www.metallographic.com
31
Please read this instruction manual carefully and follow all installation, operating and safety guidelines.
NANO 1000T / FEMTO 1500
Polishing Head
can control the aggressiveness of the
grinding/ polishing operation.
It is also very important for polishing
machines which use individual force
pistons for applying the polishing force to
run the power head and base at closely
matching speeds and in the
complementary direction. If these
machines are run with significantly different
speeds or direction the mount will have a
tendency to grind with a wedge and
therefore it will not be square.
Grinding Pressure
Grinding / polishing pressure is dependent upon the applied force (pounds or Newton's) and the area
of the specimen and mounting material. Pressure is defined as the Force/Area (psi, N/m
2
or Pa). For
specimens significantly harder than the mounting compound, pressure is better defined as the force
divided by the specimen surface area. Thus, for larger hard specimens, higher grinding / polishing
pressures increase stock removal rates. However, higher pressure also increases the amount of
surface and subsurface damage produced in the specimen.
Note regarding SiC grinding papers: as the abrasive grains dull and cut rates decrease, increasing
grinding pressures can extend the life of the SiC paper.
Higher grinding / polishing pressures can also generate additional frictional heat which may be
beneficial for the chemical mechanical polishing (CMP) of ceramics, minerals and composites.
Likewise for extremely friable specimens (such as nodular cast iron), higher pressures and lower
relative velocity distributions can aid in retaining inclusions and secondary phases.
Grinding Direction
The orientation of the specimen can have a significant impact on the preparation results, especially for
specimens with coatings. In general, when grinding and polishing materials with coatings, the brittle
component should be kept in compression. In other words, for brittle coatings, the direction of the
abrasive should be through the coating and into the substrate. Conversely, for brittle substrates with
ductile coatings, the direction of the abrasive should be through the brittle substrate and into the
ductile coating.
Manual Preparation
In order to ensure that the previous rough grinding damage is removed when grinding by hand, the
specimen should be rotated 90 degrees and continually ground until all of the scratches from the
previous grinding direction are removed. When necessary, the abrasive paper should be replaced with
a newer paper to maintain cutting rates.