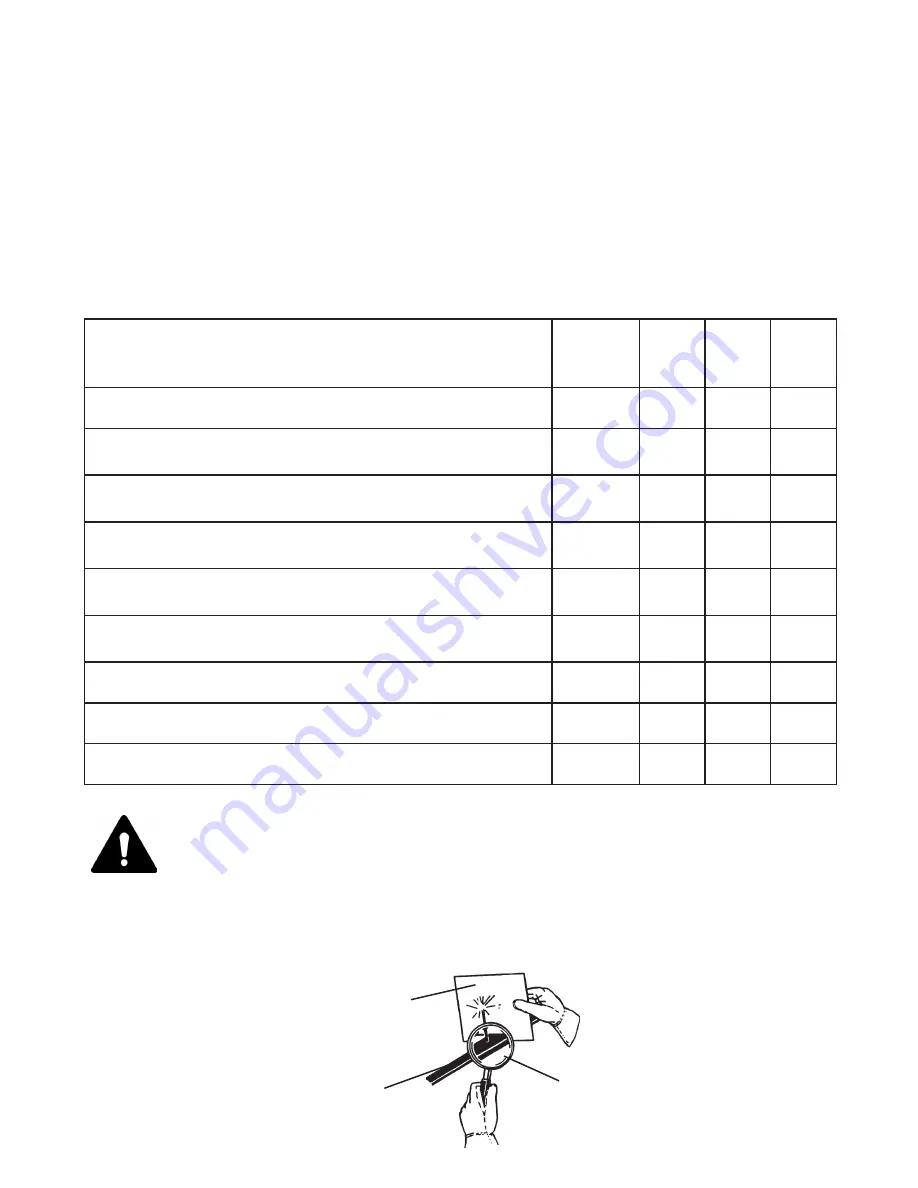
51-4180
26
MAINTENANCE
Procedure
Daily
(Every 8
Hours)
Every
50
Hours
Every
100
Hours
Every
500
Hours
Check brush pattern (See Brush Pattern Adjustment)
Check for missing or loose hardware. Replace or tighten
if necessary. (See Bolt Torque Specifications)
Check for missing or damaged safety decals and replace
as necessary.
Visually inspect the machine for worn parts or cracked
welds, and repair as necessary
Check hydraulic system for leaks and tighten as
necessary. Check for damage and replace as needed.
Check prime mover hydraulic system to ensure an
adequate level and cleanliness of hydraulic oil.
Grease Swing Plate with EP2 or equivalent lubricant.
Change Hydraulic Filter Element.
Change hydraulic oil; Use ISO VG-46 oil.
GENERAL INFORMATION
Regular maintenance is the key to long equipment life and safe operation. Maintenance
requirements have been reduced to the absolute minimum. However, it is very important that
these maintenance functions be performed as described below.
IMPORTANT: When replacing parts, use only factory approved replacement parts.
Manufacturer will not claim responsibility for use of unapproved parts or accessories,
and/or other damages as a result of their use.
WARNING! Escaping hydraulic / diesel fluid under pressure can penetrate the skin
causing serious injury. Fluid escaping from a very small hole can be almost
invisible. Use a piece of cardboard or wood, rather than hands to search for
suspected leaks.
Keep unprotected body parts, such as face, eyes, and arms as far away
as possible from a suspected leak. Flesh injected with hydraulic fluid may
develop gangrene or other permanent disabilities. If injured by injected
fluid, see a doctor at once.
CARDBOARD
HYDRAULIC HOSE
OR FITTING
MAGNIFYING
GLASS