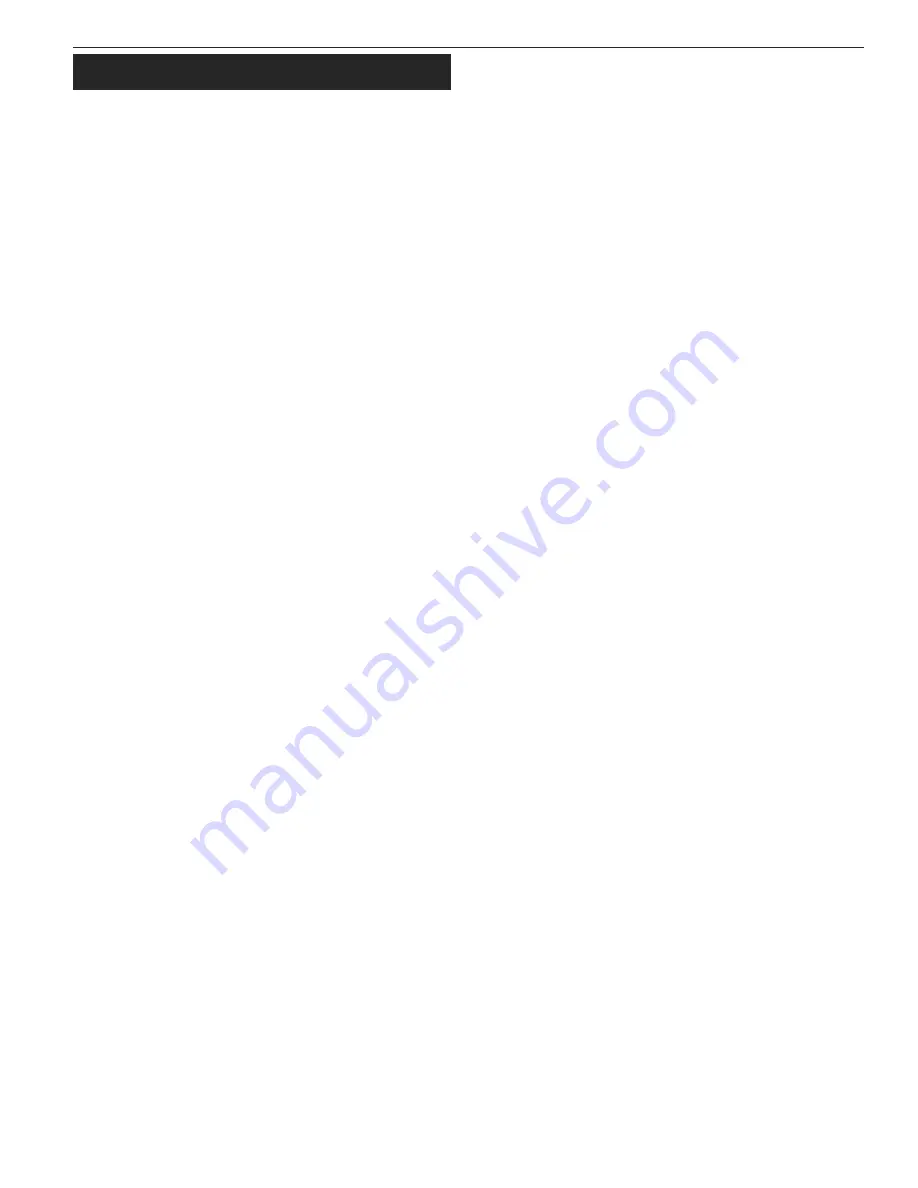
7
Palmgren Operating Manual & Parts List 9683314
OPERATION (CONTINUED)
BLADE GUIDES
Band saw blade has to be twisted relative to the plane in which it
rotates. Blade must be properly positioned relative to the workbed.
Blade guides hold the cutting portion of the blade in a plane which
is perpendicular to both the workbed and the stationary vise and
keeps the blade in line with its natural path around the blade
wheels.
Inner guide bearings on the left and right guide assemblies keep the
blade in line with the blade wheels. Outer guide bearings keep the
blade against the inner bearings.
Entire guide assembly is positioned at the factory to produce the
proper twist and should not need adjustment, however, the position
of blade guides should be checked often.
NOTE:
Since the blade position is related to both bed and the vise
jaws, the relative position of the jaw to the bed is important. When
assembled, the stationary jaw must be perpendicular to the surface
of the workbed.
CHECKING BLADE GUIDES
Refer to Figure 18.
•
Check that the blade teeth are perpendicular to the base’s
machined surface.
•
Spread the blade guides as far apart as possible.
•
Check that vise jaws are parallel and set for 90° cutoff.
•
Position the vise jaws to have the maximum separation that will
not interfere with the blade guides.
•
With the head in horizontal position, use a square against face of
rear vise jaw and check that jaw is 90° to the side of blade.
•
Check that the blade is in line with drive and tracking wheels
(Ref. Nos. 3 and 30).
•
Raise the head.
•
Look straight on at the cutting edge of the blade.
•
Make sure that the blade sides are parallel to the sides of the
bearings.
•
Make sure the bearings (Ref. No. 9) touch the blades and can still
be rotated by hand.
ADJUSTING GUIDE BEARINGS
Refer to Figure 18.
If the blade is not perpendicular to the bed or not in line with the
blade wheels, adjustment is necessary.
NOTE:
There should be .000-.001” clearance between the blade and
the guide bearings.
The guide bearings are adjusted using an eccentric location system.
The inner guide bearings are fixed and cannot be adjusted. The outer
guide bearings are mounted to eccentric sleeves (Ref. No. 10) and
can be adjusted.
•
Loosen socket head bolt (Ref. No. 6) with a wrench. Rotate the
eccentric shaft to locate bearings in desired positions.
•
Maintain eccentric shaft position and tighten socket head bolt.
CHECKING THRUST BEARINGS
Refer to Figure 18.
The thrust bearings (Ref. No. 20) should be .003-.005” (average
thickness of a piece of paper) away from back of blade.
The thrust bearings are adjusted by moving the guide bracket.
ADJUSTING GUIDE BRACKETS
Refer to Figure 18.
•
If the bearings are positioned properly and the blade is not
square, one or both blade guide brackets (Ref. Nos. 21 and 56)
must be adjusted.
•
Loosen the socket head bolts (Ref. No. 23 and 58).
•
Adjust the bracket to the correct position.
•
Tighten the socket head bolt.
•
Check the guide bearings. Repositioning the blade guide bracket
can alter the previous adjustments. Readjust if necessary.
BLADE SELECTION
Using the proper blade is important for setting up the correct
cutting conditions. Blades are made differently depending on the
specific application intended for the blade. Some simple rules can
still be applied to almost all blades.
•
Always remember to have at least three teeth in contact with the
work during a cut. When three teeth are in contact, the blade
cannot straddle the work. This prevents a tooth that enters the
cut from encountering more material than it can remove.
•
“Shocking” occurs when blade teeth contact too much material.
This can strip the teeth from the blade. When cutting harder
materials, the suggested minimum number of teeth in contact is
six because “shocking” on harder materials has a more
detrimental effect on the blade. Optimum number of teeth in
contact with workpiece distributes blade forces among more
teeth to increase cutting efficiency and reduces blade wear.
•
Optimum range is from 6-12 teeth in contact for soft materials,
up to 12-24 teeth in contact for harder materials.
•
Always have maximum number of teeth in contact with work to
prevent gullets of teeth from being clogged.
•
When choosing a blade, overall size of the work is not as
important as the thickness average. Thickness average is the
average width of material which blade will contact during each
cut. Figure 10 describes how thickness average should be
calculated.
•
Thickness average should be used when choosing a blade for the
optimum number of teeth in contact, however, the three teeth
rule should be applied to the minimum thickness, not thickness
average.
•
Keeping a selection of sharp blades on hand will yield better
cuts. Blades may last longer because they are less likely to be
misused when proper blade is available.
•
Every band saw should have at least one replacement blade of
each type used. Blade breakage is unpredictable. Consult a blade
manufacturer for detailed information about available blades for
specific uses.
REMOVING BLADE
Refer to Figure 17.
WARNING:
Disconnect band saw from power source when
changing or adjusting blades. Wear leather gloves when handling
band saw blades. Never wear gloves when operating saw.
•
Prop open the blade wheel covers.
•
Loosen the outer guide bearings on the left and right guide
assemblies. No other guide bearings should be moved.
•
Remove knobs and blade guard (Ref. Nos. 17 and 18).
•
With one hand, pinch the blade and the tracking wheel together
to protect against the possibility of the blade popping off when
tension is released.
•
Release the tension by slowly revolving the hand wheel (Ref. No.
69) counterclockwise.
•
Remove the blade.