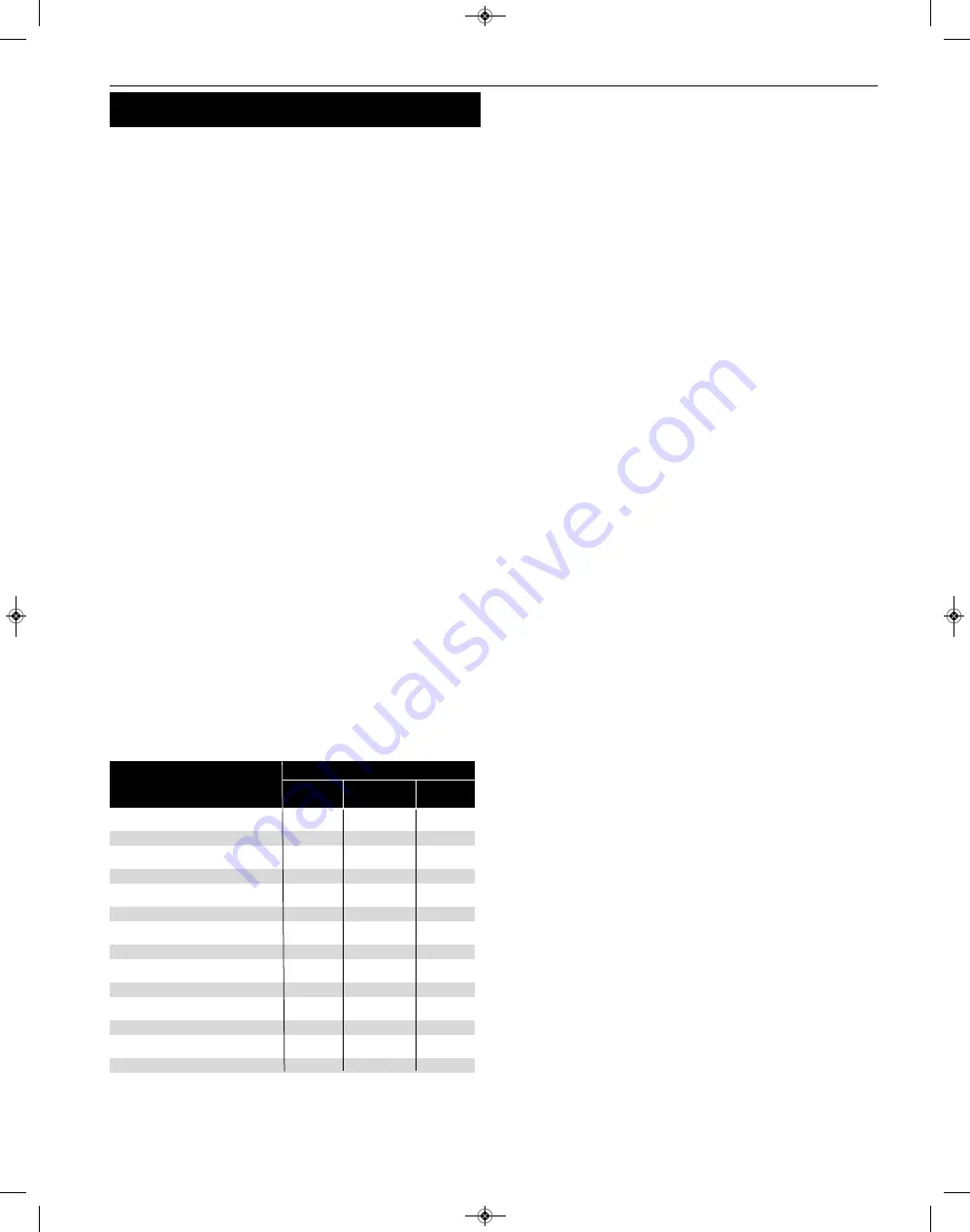
5
Palmgren Operating Manual & Parts List 9683295
OPERATION
• In the event of incorrect operation or dangerous conditions, the
machine may be stopped immediately by pressing the red
emergency shut off button on the operator control panel.
• The casual or voluntary opening of the flywheel covers causes a
safety switch activation that automatically stops all machine
functions. The flywheel cover doors MUST be closed tightly to de-
activate the safety switches.
• Check Coolant: Low coolant level can cause foaming and high
blade temperatures. Dirty or weak coolant can clog pump and
cause crooked cuts, low cutting rate and permanent blade failure.
Dirty coolant can cause the growth of bacteria with ensuing skin
irritation.
• Keep vise slides clean and oiled.
• Clean chips from blade wheels and areas around wheels.
• Saw Guide: Keep saw guide properly adjusted. Loose guide will
affect cutting accuracy.
• Saw Blade: Is saw blade sharp?
• Blade Speed: Is blade speed set correctly for workpiece material
and shape?
• Check Blade Tension: Particularly after initial cuts with a new
blade.
BLADE SELECTION
• Never use a blade so coarse that less than 3 consecutive teeth are
engaged in the workpiece at any one time. (Too few teeth will
cause teeth to strip out.)
• Never use a blade finer than required to obtain a satisfactory
surface finish or satisfactory flatness. (Too many teeth engaged in
the workpiece will prevent attainment of a satisfactory sawing rate;
frequently causes premature blade wear; frequently produces
“dished” cuts or cuts which are neither square nor parallel.)
• The chart which follows is not expected to be exactly correct for
all cases. It is intended as a general guide to good sawing
practice. Your blade supplier or factory application engineer
should be your most reliable source of correct information for
operational details of saw blades and their use.
NOTE:
• When standard wall pipe or tubing or thin wall tubing, channel
iron, angles I-beams are cut, a 10 pitch saw blade of “wave” set
type is frequently used to good advantage. Fewer than 10 teeth
per inch of saw will almost never be satisfactory.
• Tubing or structurals with wall thickness or web thickness of 1/2˝
or more can usually use an 8 or 6 pitch blade satisfactorily.
• When rectangular, solid bar is to be sawed, the work should,
whenever possible, be loaded with the thinnest cross section
exposed to the blade teeth. The pitch (or number of teeth per
inch of blade) selected must provide engagement of at least 3
consecutive teeth in the workpiece. Should application of this
rule not be possible because the thinnest cross section is too
thin, the piece must be loaded with the wider dimension
exposed to the saw teeth and a coarser blade selected from the
listing of recommendations for round and square solid bars.
BLADE TEETH PER INCH (TPI)
Choose a blade with the proper number of teeth per in (TPI) for the
material being cut. The following factors should be considered:
• Parts with a thin and/or variable section such as profiles, pipes
and plate, need closely space teeth, so that the number of teeth
used simultaneously in cutting ranges from 3 to 6.
• Parts with large crosscut sections and solid cores need widely
spaced teeth to allow for the greater volume of the shavings and
better tooth penetration.
• Parts made of soft material or plastic (light alloys, mild bronze,
Teflon, wood, etc. also require widely spaced teeth.
• Pieces cut in bundles require combo tooth design.
BLADE STRUCTURE
Bi-metal blades are the most commonly used. They consist of a
silicon-steel blade backer along with a laser welded high speed steel
(HSS) cutting edge. These type of blades are classified by a M2, M42,
M51 designation. They differ from each other because of their
hardness due to the percentage of Cobalt (Cc) and molybdenum
(Mo) contained in the metal alloy.
BLADE TYPE
Blades differ because of their construction characteristics, such as:
• Shape and cutting angle of tooth
• Pitch
• Set shape
• Angle (rake) of the teeth
Probable Pitch/Teeth Per Inch
Workpiece Size
Second
Third
(Solid Bars)
Best
Best
Best
Less than 1˝ Dia. or Sq.
10
1˝ Dia. or 1˝ Sq.
8
10
6
1 ½˝ Dia. or 1 ½˝ Sq.
8
10
6
2˝ Dia. or 2˝ Sq.
8
6
4
2 ½˝ Dia. or 2 ½˝ Sq.
6
8
4
3˝ Dia. or 3˝ Sq.
6
4
3
3 ½˝ Dia. or 3 ½˝ Sq.
6
4
3
4˝ Dia. or 4˝ Sq.
4
3
6
4 ½˝ Dia. or 4 ½˝ Sq.
4
3
6
5˝ Dia. or 5˝ Sq.
4
3
6
6˝ Dia. or 6˝ Sq.
4
3
6
7˝ Dia. or 7˝ Sq.
4
3
6
8˝ Dia. or 8˝ Sq.
4
3
6
9˝ Dia. or 9˝ Sq.
4
3
6
9683295_oipm_En012_9645931.01-0620 __ 07-02-2020 . . . .