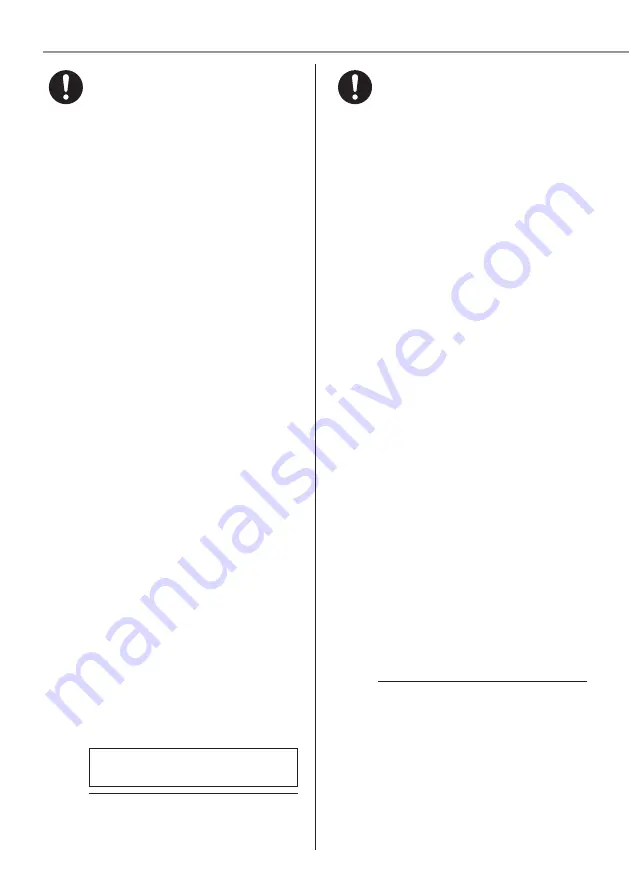
14
Safety precautions
8. Removal and evacuation
• When breaking into the refrigerant
circuit to make repairs – or for
any other purpose – conventional
procedures shall be used. However,
it is important that best practice
is followed since flammability is
a consideration. The following
procedure shall be adhered to:
remove refrigerant -> purge the
circuit with inert gas -> evacuate ->
purge with inert gas -> open the
circuit by cutting or brazing.
• The refrigerant charge shall be
recovered into the correct recovery
cylinders.
• The system shall be purged with
OFN to render the appliance safe.
• This process may need to be
repeated several times.
• Compressed air or oxygen shall not
be used for this task.
• Purging shall be achieved by
breaking the vacuum in the system
with OFN and continuing to fill until
the working pressure is achieved,
then venting to atmosphere, and
finally pulling down to a vacuum.
• This process shall be repeated until
no refrigerant is within the system.
• When the final OFN charge is used,
the system shall be vented down to
atmospheric pressure to enable work
to take place.
• This operation is absolutely vital if
brazing operations on the pipe work
are to take place.
• Ensure that the outlet for the vacuum
pump is not close to any potential
ignition sources and there is
ventilation available.
OFN = oxygen free nitrogen, type of
inert gas.
9. Charging procedures
• In addition to conventional
charging procedures, the following
requirements shall be followed.
-
Ensure that contamination of
different refrigerants does not
occur when using charging
equipment.
-
Hoses or lines shall be as short as
possible to minimize the amount of
refrigerant contained in them.
-
Cylinders shall be kept in an
appropriate position according to
the instructions.
-
Ensure that the refrigerating
system is earthed prior to charging
the system with refrigerant.
-
Label the system when charging is
complete (if not already).
-
Extreme care shall be taken not to
over
fi
ll the refrigerating system.
• Prior to recharging the system it
shall be pressure tested with OFN
(refer to #7).
• The system shall be leak tested on
completion of charging but prior to
commissioning.
• A follow up leak test shall be carried
out prior to leaving the site.
• Electrostatic charge may accumulate
and create a hazardous condition
when charging and discharging the
refrigerant. To avoid fire or explosion,
dissipate static electricity during
transfer by grounding and bonding
containers and equipment before
charging/discharging.