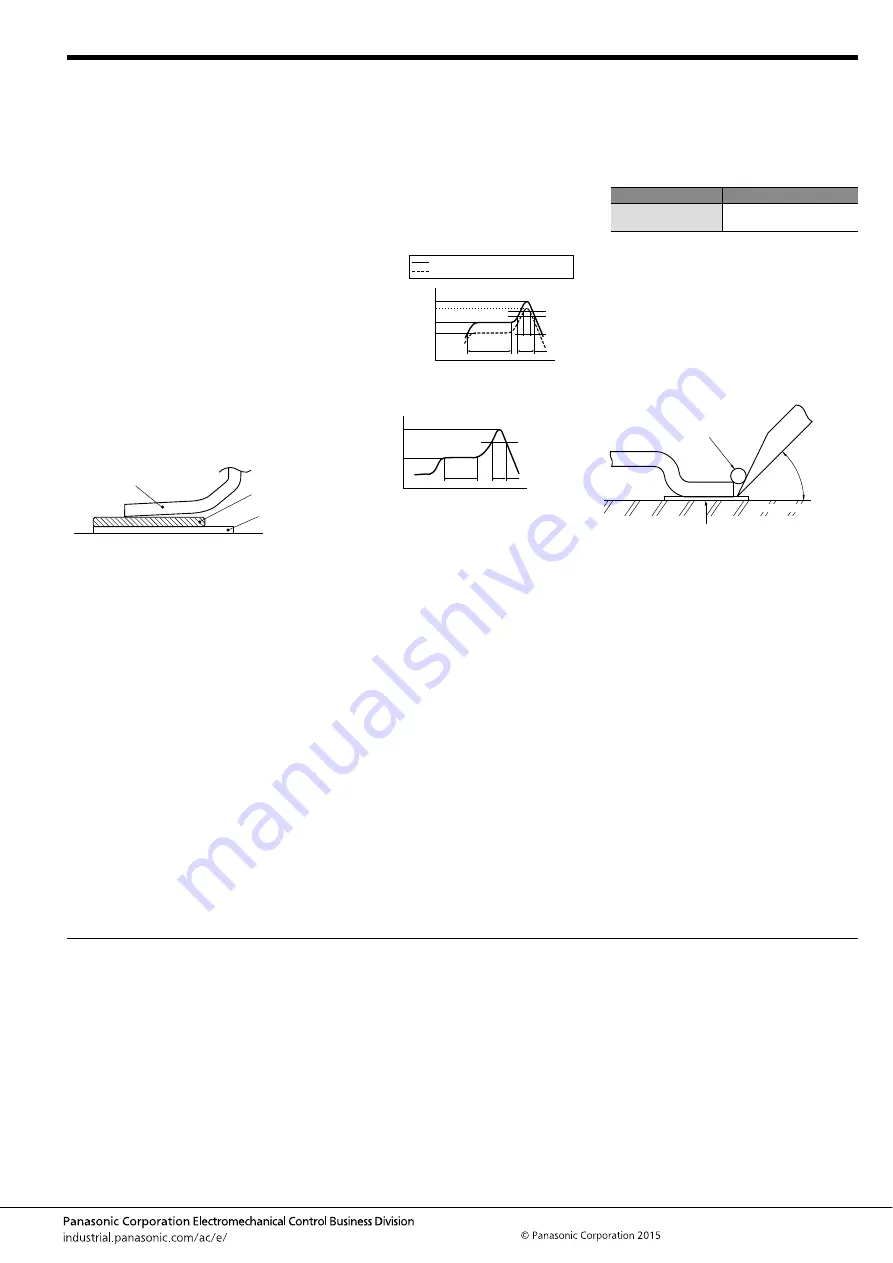
Notes on Using Narrow pitch Connectors/Stacking Connectors for High Current
–7–
ACCTB48E 201503-T
Regarding soldering
Handling Single Components
■
Reflow soldering
1) Measure the recommended profile
temperature for reflow soldering by
placing a sensor on the PC board near
the connector surface or terminals.
(Please refer to the specification for detail
because the temperature setting differs
by products.)
2) As for cream solder printing, screen
printing is recommended.
3) When setting the screen opening area
and PC board foot pattern area, refer the
recommended PC board pattern and
window size of metal mask on the
specification sheet, and make sure that
the size of board pattern and metal mask
at the base of the terminals are not
increased.
4) Please pay attentions not to provide
too much solder. It makes miss mating
because of interference at soldering
portion when mating.
5) When mounting on both sides of the
PC board and the connector is mounting
on the underside, use adhesives or other
means to ensure the connector is
properly fixed to the PC board. (Double
reflow soldering on the same side is
possible.)
6) The condition of solder or flux rise and
wettability varies depending on the type
of solder and flux. Solder and flux
characteristics should be taken into
consideration and also set the reflow
temperature and oxygen level.
7) Do not use resin-containing solder.
Otherwise, the contacts might be firmly
fixed.
• Soldering conditions
Please use the reflow temperature profile
conditions recommended below for
reflow soldering. Please contact us
before using a temperature profile other
than that described below (e.g. lead-free
solder).
• Narrow pitch connectors
(except P8 type)
• Narrow pitch connector (P8)
For products other than the ones above,
please refer to the latest product
specifications.
8) The temperature profiles given in this
catalog are values measured when using
the connector on a resin-based PC
board. When performed reflow soldering
on a metal board (iron, aluminum, etc.) or
a metal table to mount on a FPC, make
sure there is no deformation or
discoloration of the connector before
mounting.
9) Consult us when using a screen-
printing thickness other than that
recommended.
■
Hand soldering
1) Set the soldering iron so that the tip
temperature is less than that given in the
table below.
Table A
2) Do not allow flux to spread onto the
connector leads or PC board. This may
lead to flux rising up to the connector
inside.
3) Touch the soldering iron to the foot
pattern. After the foot pattern and
connector terminal are heated, apply the
solder wire so it melts at the end of the
connector terminals.
4) Be aware that soldering while applying
a load on the connector terminals may
cause improper operation of the
connector.
5) Thoroughly clean the soldering iron.
6) Flux from the solder wire may get on
the contact surfaces during soldering
operations. After soldering, carefully
check the contact surfaces and clean off
any solder before use.
7) These connector is low profile type. If
too much solder is supplied for hand
soldering, It makes miss mating because
of interference at soldering portion.
Please pay attentions.
■
Solder reworking
1) Finish reworking in one operation.
2) In case of soldering rework of bridges.
Don’t use supplementary solder flux.
Doing so may cause contact problems by
flux.
3) Keep the soldering iron tip temperature
below the temperature given in Table A.
Terminal
Paste
solder
PC board
foot pattern
60 to 120 sec.
Preheating
Peak temperature
200
°
C
220
°
C
Upper limited (Solder heat resistance)
Peak temperature 260
°
C
230
°
C
180
°
C
150
°
C
70 sec.
25 sec.
Lower limited (Solder wettability)
Time
Temperature
60 to 120 sec.
Preheating
Time
Temperature
Peak temperature
200
°
C
155 to 165
°
C
245
°
C max.
Within 30 sec.
Product name
Soldering iron temperature
SMD type connectors
300
°
C within 5 sec.
350
°
C within 3 sec.
Apply the solder
wire here
Terminal
Pattern
PC board
Small angle as
possible up to
45 degrees
Soldering
iron
1) Make sure not to drop or allow parts to
fall from work bench.
2) Excessive force applied to the
terminals could cause warping, come
out, or weaken the adhesive strength of
the solder. Handle with care.
3) Do not insert or remove the connector
when it is not soldered. Forcibly applied
external pressure on the terminals can
weaken the adherence of the terminals to
the molded part or cause the terminals to
lose their evenness.