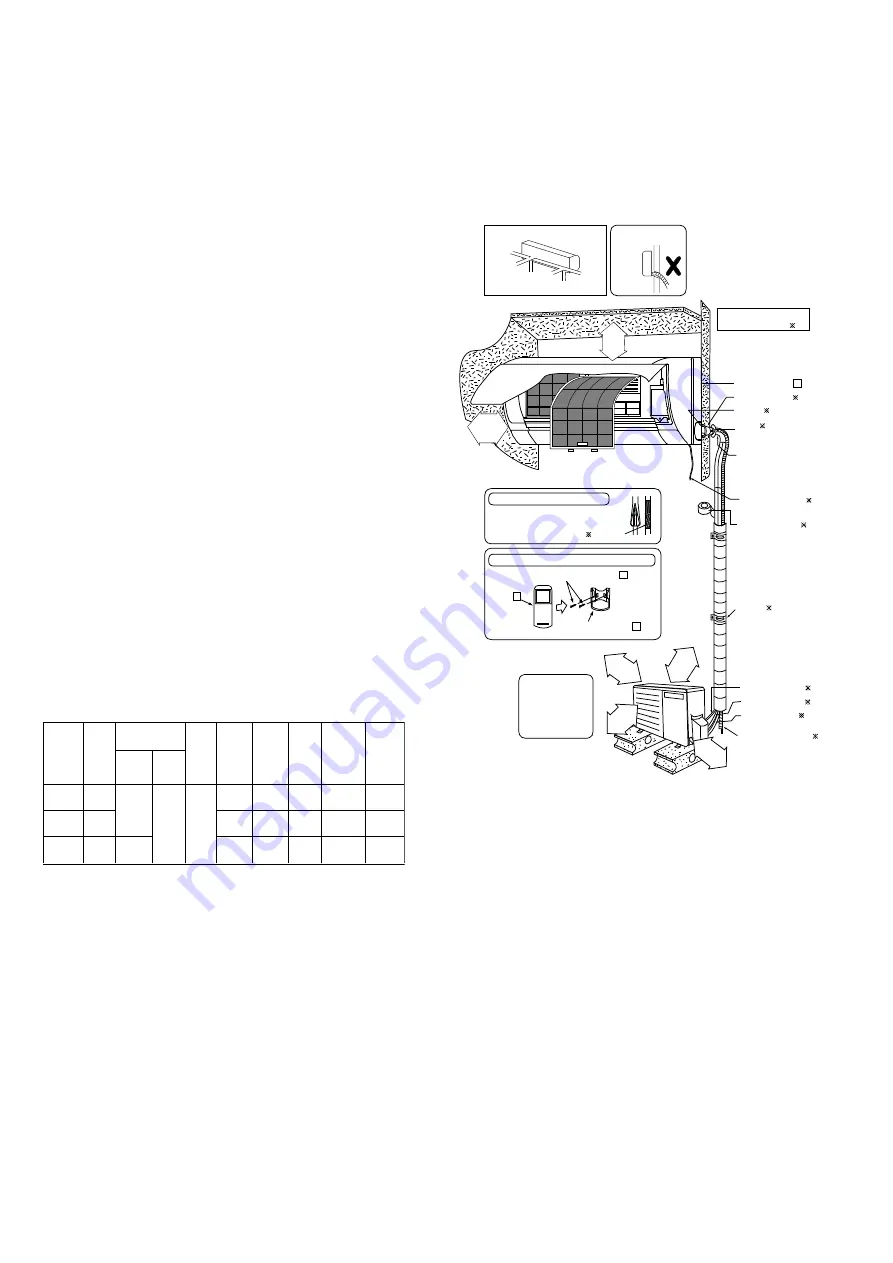
36
11. Installation Instruction
11.1 Select the Best Location
11.1.1 Indoor Unit
Do not install the unit in excessive oil fume area
such as kitchen, workshop and etc.
There should not be any heat source or steam
near the unit.
There should not be any obstacles blocking the air
circulation.
A place where air circulation in the room is good.
A place where drainage can be easily done.
A place where noise prevention is taken into
consideration.
Do not install the unit near the door way.
Ensure the spaces indicated by arrows from the
wall, ceiling, fence or other obstacles.
Recommended installation height for indoor unit
shall be at least 2.5 m.
11.1.2 Outdoor Unit
If an awning is built over the unit to prevent direct
sunlight or rain, be careful that heat radiation from
the condenser is not obstructed.
There should not be any animal or plant which
could be affected by hot air discharged.
Keep the spaces indicated by arrows from wall,
ceiling, fence or other obstacles.
Do not place any obstacles which may cause a
short circuit of the discharged air.
If piping length is over the [piping length for
additional gas], additional refrigerant should be
added as shown in the table.
Model
Horse
Power
(HP)
Piping size
Std.
Length
(m)
Max.
Elevation
(m)
Min.
Piping
Length
(m)
Max.
Piping
Length
(m)
Additional
Refrigerant
(g/m)
Piping
Length
for add.
gas
(m)
Gas
Liquid
UE9***,
PE9***
1.0HP
9.52mm
(3/8") 6.35mm
(1/4")
5
15
3
15
20
7.5
UE12***,
PE12***
5
.
7
0
2
5
1
3
5
1
P
H
5
.
1
UE18*** 2.0HP 12.7mm
(1/2”)
15
3
15
20
7.5
Example: For UE9***
If the unit is installed at 10 m distance, the quantity of
additional refrigerant should be 50 g .... (10-7.5) m ×
20 g/m = 50 g.
11.1.3 Indoor/Outdoor Unit Installation
Diagram
50 mm
or more
65
m
m
or
m
or
e
(Left and right are identical)
Vinyl tape
Remote control holder fixing screws
Remote control holder
5
6
1
3
Remote
control
100
m
m
or m
ore
10
00
m
m
or
m
or
e
10
0
m
m
or
m
or
e
300
m
m
or m
ore
It is advisable to
avoid more than 2
blockage directions.
For better ventilation
& multiple-outdoor
installation, please
consult authorized
dealer/specialist.
Installation plate
Sleeve ( )
Bushing-Sleeve ( )
Bend the pipe as
closely on the wall as
possible, but be careful
that it doesn’t break.
Saddle ( )
Power supply cord ( )
Additional drain hose ( )
Gas side piping ( )
Connection cable ( )
Putty ( )
(Gum Type Sealer)
Installation parts you
should purchase ( )
Vinyl tape (wide) ( )
• Apply after carrying
out a drainage test.
• To carry out the
drainage test,
remove the air filters
and pour water into
the heat exchanger.
Liquid side piping ( )
Piping direction
Attention not to bend
up drain hose
Right
Right
Rear
Right
bottom
Left
Rear
Left bottom
Left
(Front side)
• Carry out insulation after
checking for gas leaks and
secure with vinyl tape.
Attaching the remote control holder to the wall
Insulation of piping connections
This illustration is for explanation purposes only.
The indoor unit will actually face a different way