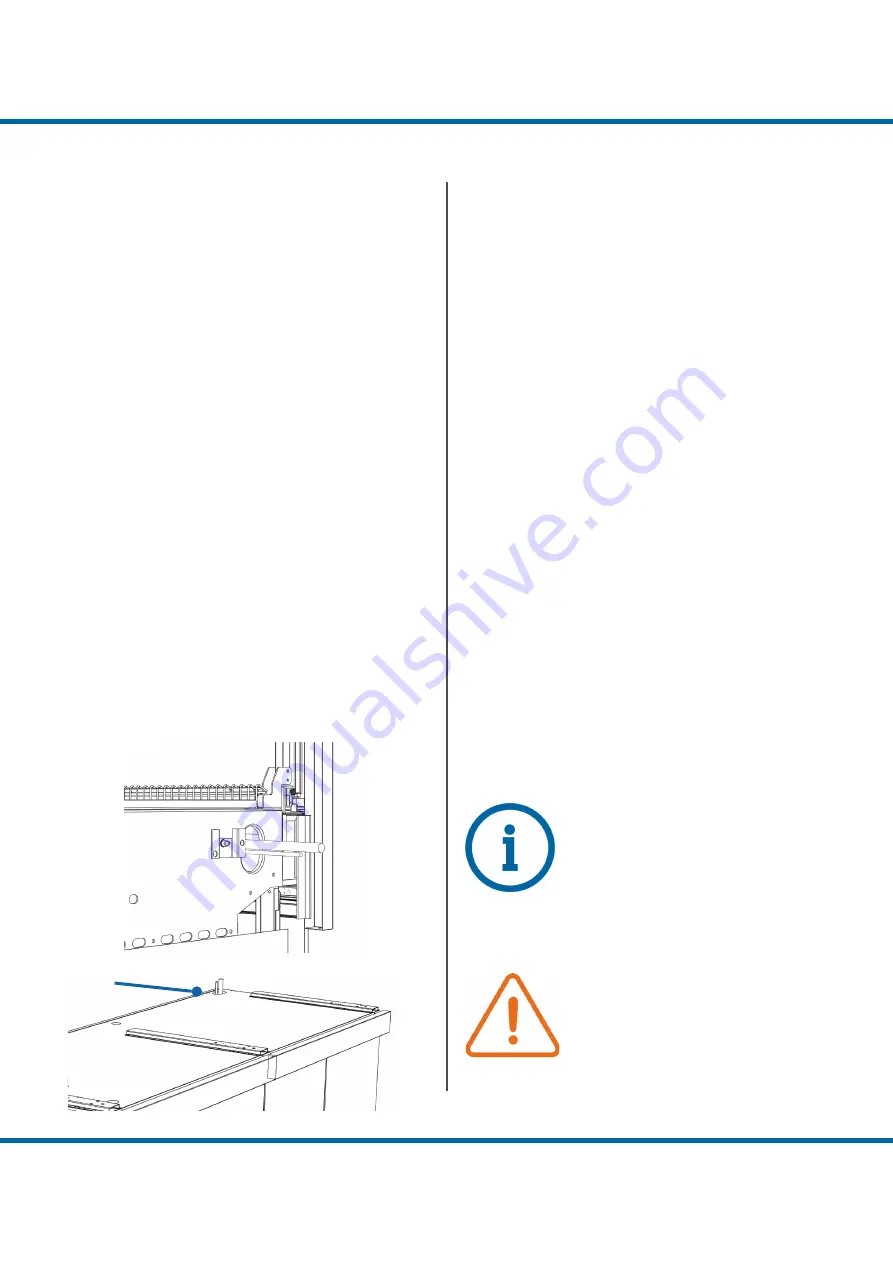
PAGE 24
SMED SEMI VERTICAL - HUSSMANN
Top of the case
CAUTION:
Remove or protect the
expansion (TX) valve feeler bulbs (or
power lead if electronic valve) from
heat. Ensure the power lead is clear of
heat and flame.
NOTE:
All installation works must
be completed by a qualified person
to best trade practices, customer
specifications, relevant AS or ISO
Standards / and any Territorial
Authority requirements or Regulations.
• Connection of refrigeration lines is to be undertaken
by qualified persons only.
• Refrigeration pipes are located under the pan
decks and can be run from case to case through
designated access holes. These are in;
* The end frames
* Base of the case
* Run through to the top of the case.
See
figure 3AA:
service layout for location of the
refrigerant supply line.
• Up to four cases can share one refrigeration supply
line, however, to ensure best performance, it is
recommended that no more than three cases
share an up-stand. Liquid lines must be sized to
supply full head of liquid at all times, and suction
line sizes must consider refrigerant velocities
for proper oil return during both high and low
loads whilst meeting customer specifications for
maximum allowable pressure drop.
• The evaporator coils have been charged with dry
nitrogen in the factory. The holding charge of dry
nitrogen will be stated on a tag on each evaporator
coil. Please check and verify pressure is /- 20
kPa (3 psi) of tag stated pressure before installation
• For all pipe sizes refer to latest Product Engineering
Data Sheet (PED)
To connect refrigeration lines:
1. Use free-flowing dry nitrogen when brazing piping
to ensure internal cleanliness of piping and
eliminate copper oxide debris.
2. Insulate all external pipe work to Standard practice
and Customer specifications. Insulation should be
adequately sized/rated to prevent condensation
forming under any circumstances.
3. Permanent sealing of all penetrations made
in the cabinet panels inside-to-outside is the
responsibility of the Installer.
4. Connect to condensing unit or compressor.
5. Pressure test all welded and fastened connections
to ensure they are free of leaks.
6. Dehydrate the refrigeration system using the triple
evacuation method. Use a vacuum pump to
minimum 1000 microns for the first two evacuations
and minimum 500 microns on the third, or to
the customer’s specific requirements. Break
evacuations 1 and 2 with dry nitrogen, allowing the
pressure to rise above atmospheric pressure each
time.
7. Charge with refrigerant after final (3rd) evacuation.
once the last vacuum has passed holding 500
microns or lower with no rise for 1 hour with the
vacuum pump off and measure at the furthest
feasible point in the system away from the vacuum
pump
3.9
CONNECTING REFRIGERANT LINES
FIGURE 3AA
INSTALLATION