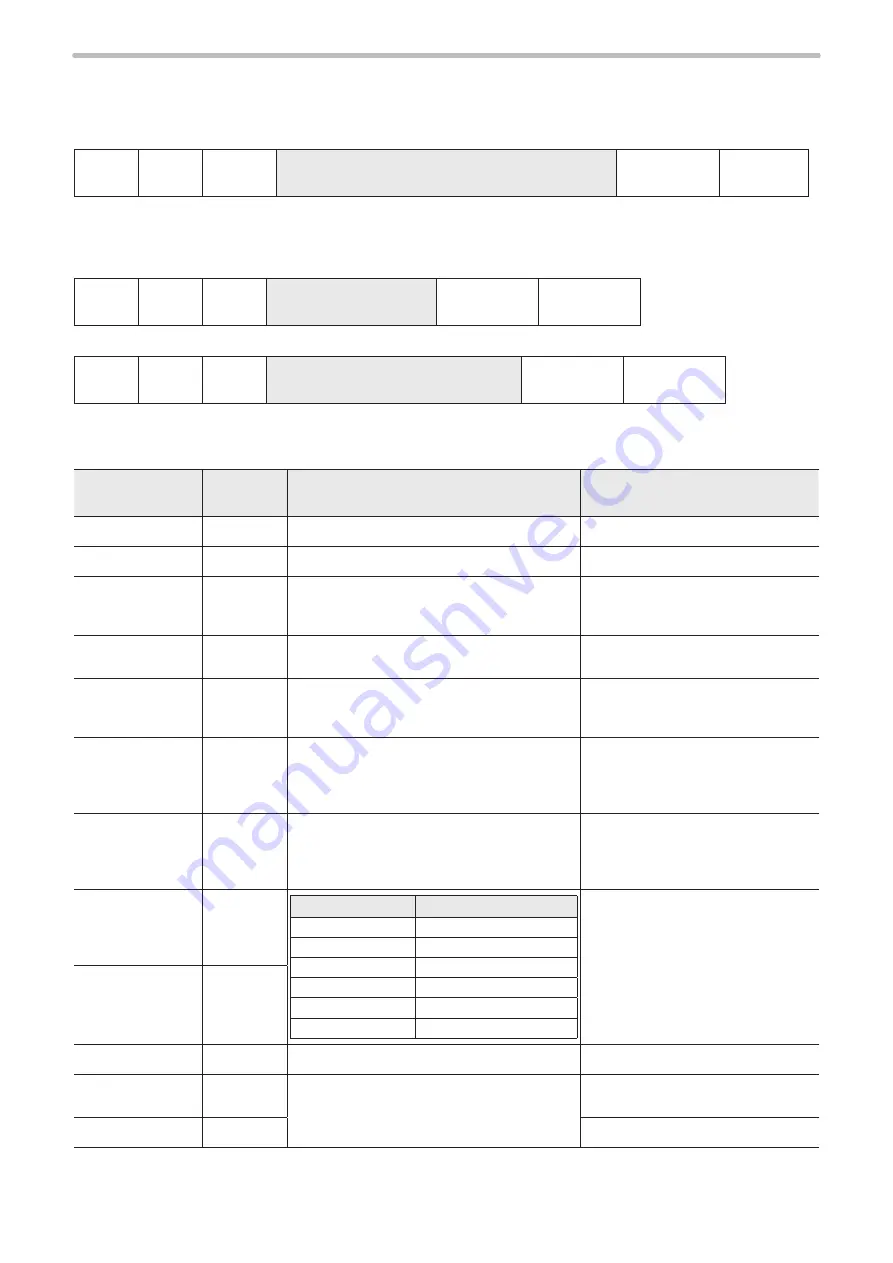
58
■
Bar code marking condition: BRF
Sets the marking condition for bar code and 2D code.
Setting / Readout data of bar code marking condition
STX
BRF
Sub
command
[Bar code No.] [Layer No.] [Code
type]
[Setting data (varies depending on bar code type)]
(Check sum)
Delimiter
Sub command is “S” at the time of setting and “A” for response data at the time of readout.
Readout request of bar code marking condition
When the code type is other than composite:
STX
BRF
R
[Bar code No.]
2-byte
(Check sum)
Delimiter
When the code type is composite:
STX
BRF
R
[Bar code No.] [1D/2D selection]
3-byte
(Check sum)
Delimiter
In [1D/2D Selection] field, specify “1” for readout of 1D side or “2” for readout of 2D side of composite code.
1. QR code (Data length: 44-byte)
Name
Data length
[byte]
Description
Remarks
Bar code No.
2
“00”–“15”
Layer No.
2
“00”–“15”
Code type
2
“10”: Model 1
“11”: Model 2
“12”: Micro QR code
System
reservation
1
“0” fixed
Version
2
Model 1: “00”–“14”
Model 2: “00”–“22”
Micro QR: “00”–“04”
When specifying “00”, it is
automatically specified.
Data input mode
1
“0”: Number
“1”: Alpha (text)
“2”: Binary
“3”: Kanji
Error correction
level
1
“0”: L
“1”: M
“2”: Q
“3”: H
For micro QR, Error Correction
Level “H” cannot be used.
X position
8
Model type*
Setting range [mm]
LP-Sxx0(W)
“-045.000”–“+045.000”
LP-Sxx5(W)
“-080.000”–“+080.000”
LP-Sxx2
“-027.500”–“+027.500”
LP-Mxx0 / LP-Zxx0 “-060.000”–“+060.000”
LP-Mxx5
“-110.000”–“+110.000”
LP-Mxx6/LP-Zxx6
“-165.000”–“+165.000”
Specifies the center coordinate of
the code.
Y position
8
Rotation angle
7
“-180.00”–“+180.00” [°]
Module H.
5
“0.001”–“9.999” [mm]
Interval of module in longitudinal
direction.
Module W.
5
Interval of module in lateral direction
* For the detail of the model type, refer to “Target laser marker” (P.4).
ME-LPMSZ-SR-9
Summary of Contents for LP-M Series
Page 8: ...1 Before External Control ME LPMSZ SR 9...
Page 16: ...2 Basics of Serial Communication RS 232 Ethernet ME LPMSZ SR 9...
Page 34: ...3 Communication Command and Function ME LPMSZ SR 9...
Page 165: ...Troubleshooting ME LPMSZ SR 9...
Page 186: ...Character Code Table ME LPMSZ SR 9...
Page 199: ...Index ME LPMSZ SR 9...
Page 202: ...202 MEMO No 9000 0063 59V ME LPMSZ SR 9...
Page 203: ...No 9000 0063 59V...
Page 204: ...Panasonic Industrial Devices SUNX Co Ltd 2013 2019 March 2019 9000 0063 59V...