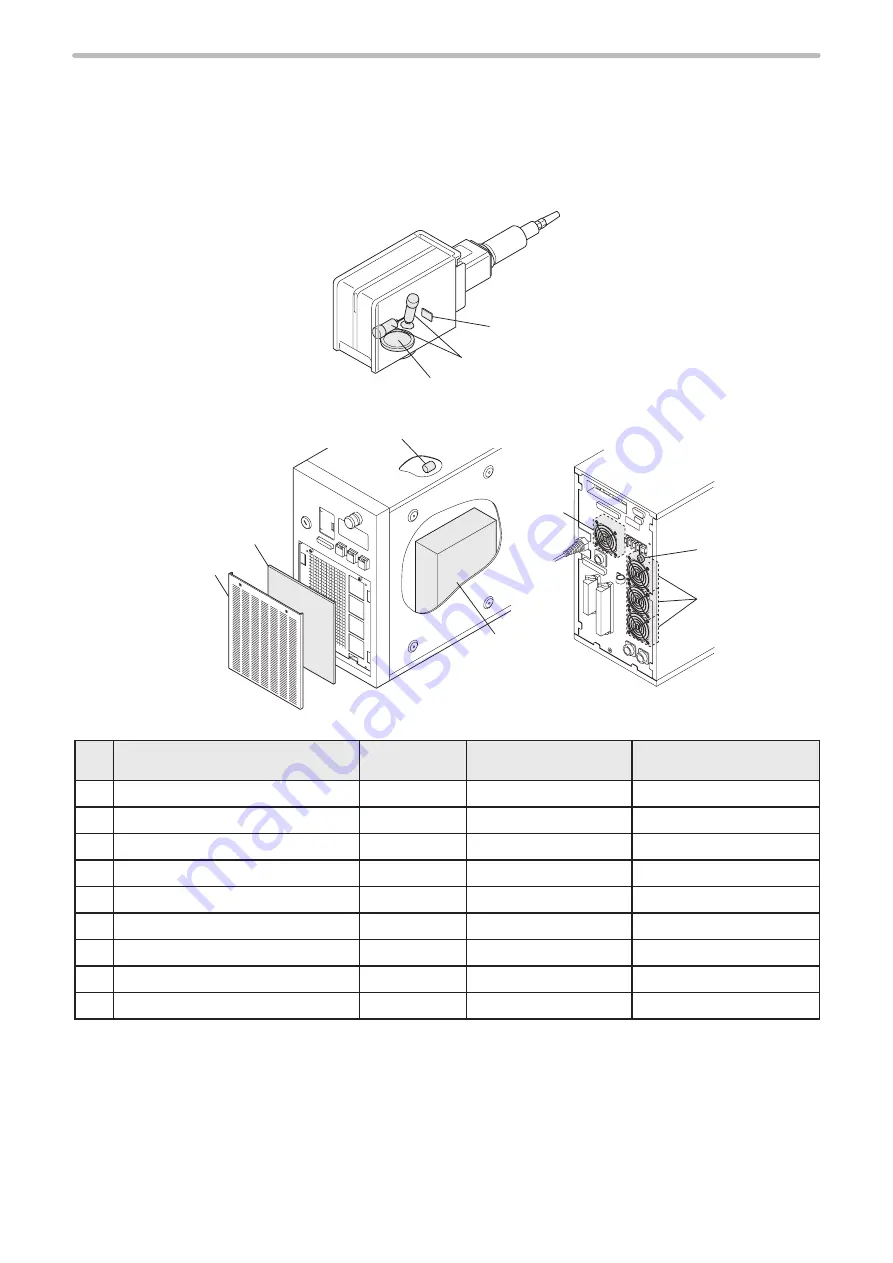
127
4-1 Maintenance Items
Listed below are typical parts that require cleaning or replacement depending on the usage environment or duration of
service of the laser marker. Some parts are maintainable by the customer, and other parts are required to be repaired or
replaced by our service representative, depending on the types of parts and the defects.
For purchasing replacement parts or requesting our service representative to repair or replace parts, contact our sales
agency.
q
w
e
Head
r
t
o
y
Rear
Front
Controller
i
u
u
No. Parts name
Main cause for
degradation
Daily maintenance
Replacement when degraded
or defective
q
Protection glass of laser emission port
Contamination Cleaning
Customer-replaceable
w
Galvano scanner
Aging
―
By our service representative
e
Internal shutter
Aging
―
By our service representative
r
Laser oscillator
Aging
Check output power
By our service representative
t
Air filter
Contamination Cleaning
Customer-replaceable
y
Intake vent
Contamination Cleaning
―
u
Air-cooling fan
Contamination Cleaning
By our service representative
i
Fuse
Blown
―
Customer-replaceable
o
Battery inside the controller
Aging
―
By our service representative
ME-LPS-SSM-8
Summary of Contents for LP-S Series
Page 15: ...15 MEMO ME LPS SSM 8 ...
Page 26: ...26 Chapter 1 Specification ME LPS SSM 8 ...
Page 41: ...41 Chapter 2 Preparation ME LPS SSM 8 ...
Page 78: ...Chapter 3 Connection for External Control ME LPS SSM 8 ...
Page 126: ...Chapter 4 Maintenance ME LPS SSM 8 ...
Page 148: ...Troubleshooting ME LPS SSM 8 ...
Page 169: ...Index ME LPS SSM 8 ...
Page 172: ...172 MEMO No 9000 0066 16V ME LPS SSM 8 ...
Page 173: ...No 9000 0066 16V ...