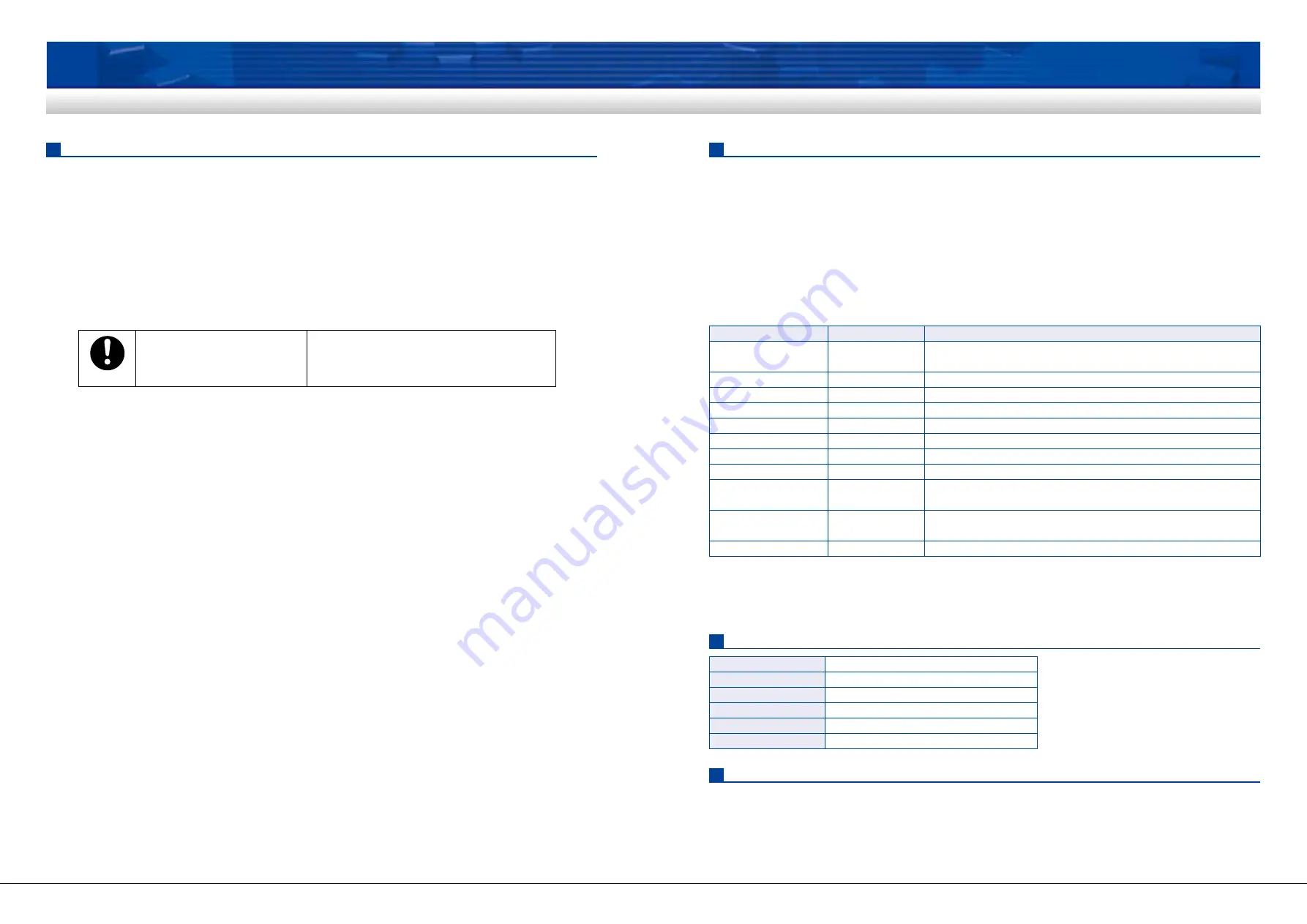
– A-46 –
Panasonic Corporation Electromechanical Control Business Division
industrial.panasonic.com/ac/e/
©
Panasonic Corporation 2018
AQCTB02E 201806-E
– A-47 –
Panasonic Corporation Electromechanical Control Business Division
industrial.panasonic.com/ac/e/
©
Panasonic Corporation 2018
AQCTB02E 201806-E
Operating instruction
Inspection and maintenance / Operating conditions / Installation requirements
Handling instructions
Inspection and maintenance
Periodically perform check and maintenance to assure safe and reliable operation.
• Practical considerations for maintenance
• To secure safety during maintenance operation, turning off/on of power supply must be done by the personnel
who is responsible for the current maintenance work.
• Do not touch the motor while it is still running or immediately after it stops. (Motor is hot.)
• Before starting the megger testing of the motor (to measure the insulation resistance), completely disconnect
it from associated devices and components.
Otherwise, the megger tester will damage the devices under test.
• Daily check
• Perform the daily check to prevent potential problems.
• Perform appropriate corrections upon finding any failure or defective.
• Periodic check (once/1 to 2 month)
• Motor: dust accumulation
• Casing: deformation or corrosion
• Insulation resistance: 1 MΩ or more (across frame and leads)
Operating conditions
Ambient temperature
Ambient humidity
Altitude
Vibration
Operating voltage
Operating voltage
–10 ˚C to + 40 ˚C
85 %RH or less
1000 m or lower
4.9 m/s
2
or less
Nameplate rating ±10 %
*
50 Hz or 60 Hz as specified on the nameplate
*
±10 % is not a guaranteed value for continuous
running condition.
Installation requirements
Install the geared motor at the optimal location as described below for prolonged service life.
(1) Indoor free from rain and direct sunlight
(2) Free from vibration 4.9 m/s
2
or more; shock, dust, iron powder or oil mist; splash of water, oil and grinding
fluid; and away from flammable materials, corrosive gas (H
2
S, SO
2
, NO
2
, Cl
2
, etc.) or flammable gas.
(3) Well ventilated dry and clean location containing negligible amount of oil or dust, and away from heat source i.e. oven.
(4) Location that allows easier access for checking and cleaning of the unit.
(5) Don't use the motor in a closed environment where the motor temperature increases, shortening the life.
Check item
Change in voltage
Load curren
Ambient temperature
Temperature rise
Noise
Vibration
Deposition of powder dust
Oil leakage
Insulation resistance
Grease leakage
Foundation bolt
Checking method
Voltmeter
Ammeter
Thermometer
Thermometer
Auditory perception
Vibrometer/feeling
Visual
Visual
Insulating-resistance
tester
Visual
Torque wrench
Description
Rated voltage ±2 % to 3 %. Although the specification assures normal operation
within ±10 % deviation, the motor performance and life are not secured.
As indicated on the nameplate
–10 ˚C to +40 ˚C
90˚C or below on frame surface (ambient temperature 40 ˚C)
No increase in abnormal sound or noise level
No abnormal vibration
Flow of cooling air is not disturbed by dust and powder
No oil or grease from joint to gear head or from output shaft
Connect the 500 V megger across motor lead and earth terminal.
The reading should be 50 MΩ or more.
Check exterior and peripheral of motor and gear head for coat of grease or oil.
If the leakage will affect the application, use cover as necessary for protection.
Check bolts for loosening and retighten as necessary.
Operating instruction
• Before running the motor
Check the following points:
• Correct wiring to the power source?
• Secure grounding to earth?
• Appropriate fuse and circuit breaker?
• No loose connection to the machine? No loose tightening bolts?
• No oil or grease leakage nor blot?
• Trial running
Make a trial run:
(1) Without a load, turn on the motor and gear head to verify the rotational direction and speed, and check for
abnormal state, i.e. vibration, noise, etc. Install the motor and gear head on the machine.
(2) Turn on power and verify that the motor runs smoothly and the bearing and gear head produce no
abnormal sounds.
• While motor is running
Check the load:
• Measure the current flow rate and adjust the load so that the current value is well below the rating described
on the nameplate.
• When the reduction ratio of the gear head is 1/50 or more, the torque will exceed the permissible shaft
torque even if the measured current value is lower than nameplate rating. If this is the case, decrease the
load.
Check the temperature rise of the motor:
• Temperature rise will saturate by 3 hours after starting the motor. For the reversible motor and single-phase
induction motor with electromagnetic brake, observe the time rating of 30 minutes.
• Keep the frame temperature 90 ˚C or below when the ambient temperature is 40 ˚C.
• At power failure:
Immediately turn off main power switch.
• Unexpected accident may occur when the power recovers while the switch is in on position; or the motor
may not start if the load is too heavy and the winding may burn.
• While the motor is running:
• Do not touch the motor since it gets very hot. (Or it may result in burn injury.)
• Turn off the motor as the system shows unexpected behavior. (Consult the local agent as necessary.)
• Other precautions:
Check the starting voltage:
With the geared motor installed on the machine, check the starting voltage of the motor using a variable
transformer and voltmeter. The voltage should be lower than the value shown below.
(1) Reversible motor: 70 % of the rated voltage
(2) Induction motor: 80 % of the rated voltage
• The machine may not start if the voltage fluctuates. The machine may not start because of change in the
static friction torque due to the aging or temperature, or fluctuation of the motor.
Do
Check rotating direction
Unexpected operation or movement will
cause malfunction or personal injury.