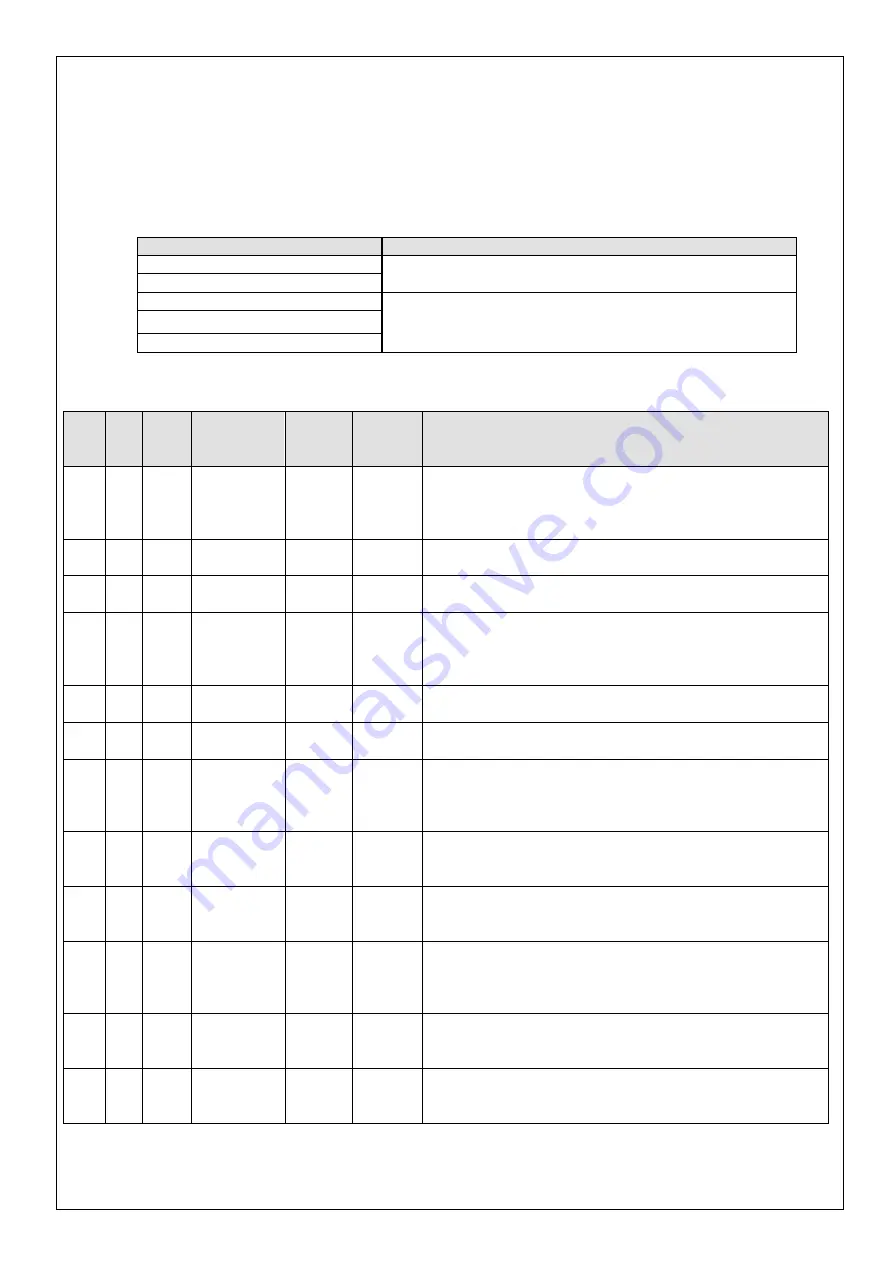
No. SX-DSV02829 -
102-
5-2-5 Notch filter
In case of a low machine stiffness, you cannot set up a higher gain because vibration and noise occur due to oscillation
caused by axis distortion or other causes. By suppressing the resonance peak at the notch filter, higher gain can be
obtained or the level of vibration can be lowered.
1) Limitation
The MINAS-A5BL series has the following limitations.
Cycle time(communication cycle)
Limitation
250μs
Use of 3 notch filters allowed
500μs
1000μs
No limitation (Use of 4 notch filters allowed)
2000μs
4000μs
2)
Parameters
MINAS-A5BL series feature 4 normal notch filters. You can adjust frequency and width and depth.
Class No.
At-
trib-
ute *1)
Title
Range
Unit
Function
2
01
B
1st notch
frequency
50–5000
Hz
Set the center frequency of the 1st notch filter.
The notch filter function will be invalidated by setting up this parameter
to “5000”.
2
02
B
1st notch width
selection
0–20
—
Set the width of notch at the center frequency of the 1st notch filter.
2
03
B
1st notch depth
selection
0–99
—
Set the depth of notch at the center frequency of the 1st notch filter.
2
04
B
2nd notch
frequency
50–5000
Hz
Set the center frequency of the 2nd notch filter.
The notch filter function will be invalidated by setting up this parameter
to “5000”.
2
05
B
2nd notch width
selection
0–20
—
Set the width of notch at the center frequency of the 2nd notch filter.
2
06
B
2nd notch depth
selection
0–99
—
Set the depth of notch at the center frequency of the 2nd notch filter.
2
07
B
3rd notch
frequency
*2)
50–5000
Hz
Set the center frequency of the 3rd notch filter.
The notch filter function will be invalidated by setting up this parameter
to “5000”.
2
08
B
3rd notch width
selection
*2)
0–20
—
Set the width of notch at the center frequency of the 3rd notch filter.
2
09
B
3rd notch depth
selection
*2)
0–99
—
Set the depth of notch at the center frequency of the 3rd notch filter.
2
10
B
4th notch
frequency
*2)
50–5000
Hz
Set the center frequency of the 4th notch filter.
The notch filter function will be invalidated by setting up this parameter
to “5000”.
2
11
B
4th notch width
selection
*2)
0–20
—
Set the width of notch at the center frequency of the 4th notch filter.
2
12
B
4th notch depth
selection
*2)
0–99
—
Set the depth of notch at the center frequency of the 4th notch filter.
*1)
For parameter attribute, refer to Section 9-1.
*2)
When the applicable filtering function is used, parameter value is automatically set.
R1.00
Motor Business Unit, Panasonic Corporation