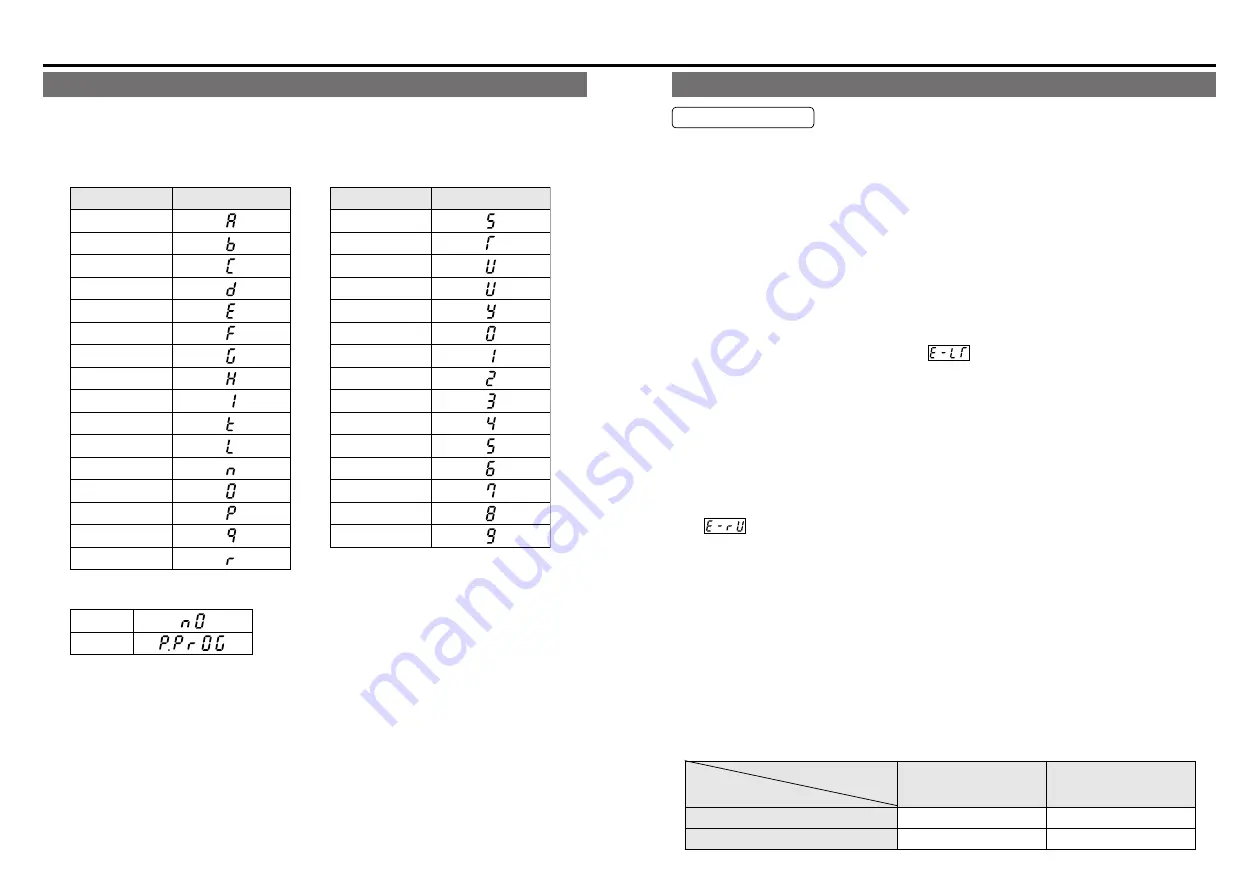
-
47
-
-
46
-
List of parameters
Detail of parameters
List of parameters
Figures displayed on the 7 segment display of the Digital key pad are shown below.
A
B
C
D
E
F
G
H
I
K
L
N
O
P
Q
R
Alphanumeric
LED display
S
T
U
V
Y
0
1
2
3
4
5
6
7
8
9
Alphanumeric
LED display
nO
• Example of LED display
P.PrOG
Detail of parameters
Operation setting
• Positioning operation
This Brushless amplifier can save positioning information for a maximum of 4 points (the
1st to the 4th point), and allows operation by use of I/O interface. Travel distance, speed
setting, acceleration time, deceleration time, and coordinate (relative travel/absolute travel)
can be set for each point. Further, setting block operations allows operation to change
speed setting and position allowing continuous movements of position to position with a
single operation
command.
Homing must be completed for executing positioning operation. (It is possible to make
homing unnecessary by Pr48.) If operation command run such as operation start is input
without homing completed, the run command is ignored. If limit sensor is detected after
completion of homing, hardware limit error
(E-LT) is found. Travel distance is the ad-
dition of rotation number and pulse of motor shaft. One rotation of motor shaft corresponds
to 288 [pulses], therefore the travel distance is the rotation number x 288 + pulse [pulses].
e.g.) When 1 [rotations] and 144 [pulses] are set at the target position, the travel distance
is 432 pulses, this represents a travel distance of 1.5 rotations. Negative values can
also be set on the pulse/value. When 2 [rotations] – 144 [pulses] is set, it also repre-
sents the same travel distance of 1.5 rotations.
Single positioning command allows up to 32767 rotations at the maximum on the motor
shaft. When operation command is above 32767 rot 1 pulse, command execution
error
(E-rU) is found.
This Brushless amplifier is provided with two types of positioning instruction function, i.e.
point designation run and sequential run. Operation to a designated point is executed by
point designation run. In sequential run, point number is automatically updated (such as 1
→
2
→
3
→
1 ...) whenever an run signal is input.
[1] Point designation run (using run start signal and point designation signal)
Set Pr50 to 53 as follows and assign the function of signal input. Of signal inputs 1 to 4 (
I
1
to
I
4), set the parameter used for run start at “8”, the input used for point designation 1 at “6”,
and the input parameter used for point designation 2 at “7”. When point designation is not
assigned to signal input, such signal is always considered to be off. (For example, when
the 3rd and 4th point are not designated, it is not required to assign point designation 2.)
When run start is input after designation of point, the motor moves to any desired point.
Point designation 1
Point designation 2
OFF
ON
OFF
Runs to the 1st point.
Runs to the 2nd point.
ON
Runs to the 3rd point.
Runs to the 4th point.