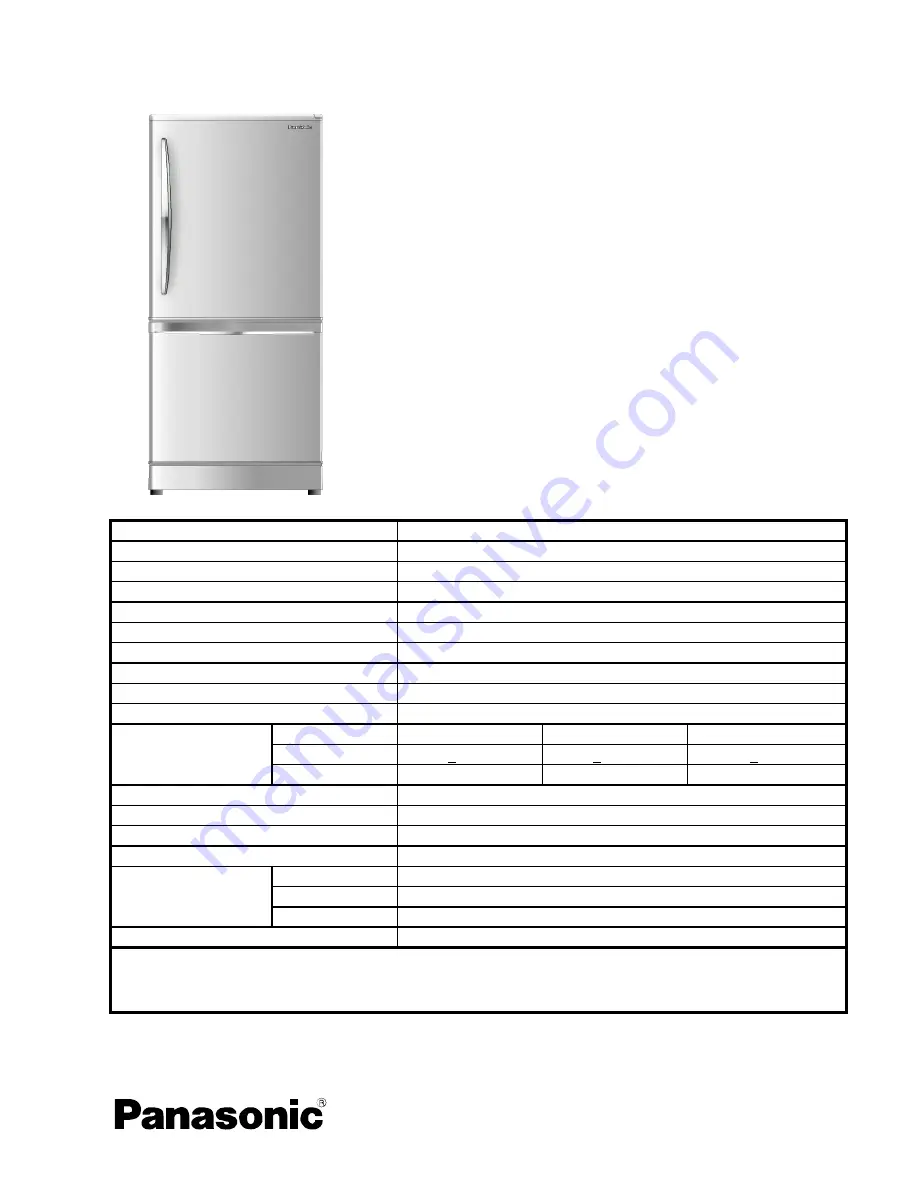
SPECIFICATION *)
Model
Voltage
Frequency
Input
Ampere
Oil Charge
Refrigerant Charge ( NON-CFC)
Temperature Control
Defrosting System
Cooling System ( Evaporator )
Dial Position
FC Room (
o
C)
PC Room (
o
C)
Blowing Agent
Thickness Insulation
Capacity (Litres)
Color
Wide
Depth
Height
Net Weight **)
*) Specification subject to change without prior notice.
**) Weight and dimension are actual condition.
Matsushita Electric Industrial Co., Ltd.
Made in Indonesia
-1-
Destination : Malaysia
NR - B203G-S7
Cabinet Dimension
( External Dimension)
46 kg
50 Hz
207 Liter ( FC = 65 Liter )
Universal Silver
Polyurethane
40 mm
600 mm
642 mm
Cooling Performance
( AT 32
o
C )
0 ± 2.5
3.0 ± 2.5
< -17.0
< -22
< -13.0
5.0 ± 2.5
280 ± 5 cc ( Freol Alpha - 22 )
240 Volt ~
0.48 A
Cold
Colder
Coldest
103 W
NR - B203G-S7
PMIRF0806022AI
Refrigerator
1406 mm
Service Manual
Indirect Cooling ( No Frost )
Auto Defrost - Auto Defrost Stop
Dial Adjustment
120 ± 5 gram ( HFC-134a )
Summary of Contents for NR-B203G-S7
Page 10: ... 9 ...
Page 22: ...1 Part Structure 1 2 LIST OF SPARES PARTS INDICATED SAFETY PART 52 90 91 19 ...
Page 23: ...PMIRF0806022AI 1 2 Part Structure 2 2 20 ...
Page 26: ... 22 ...