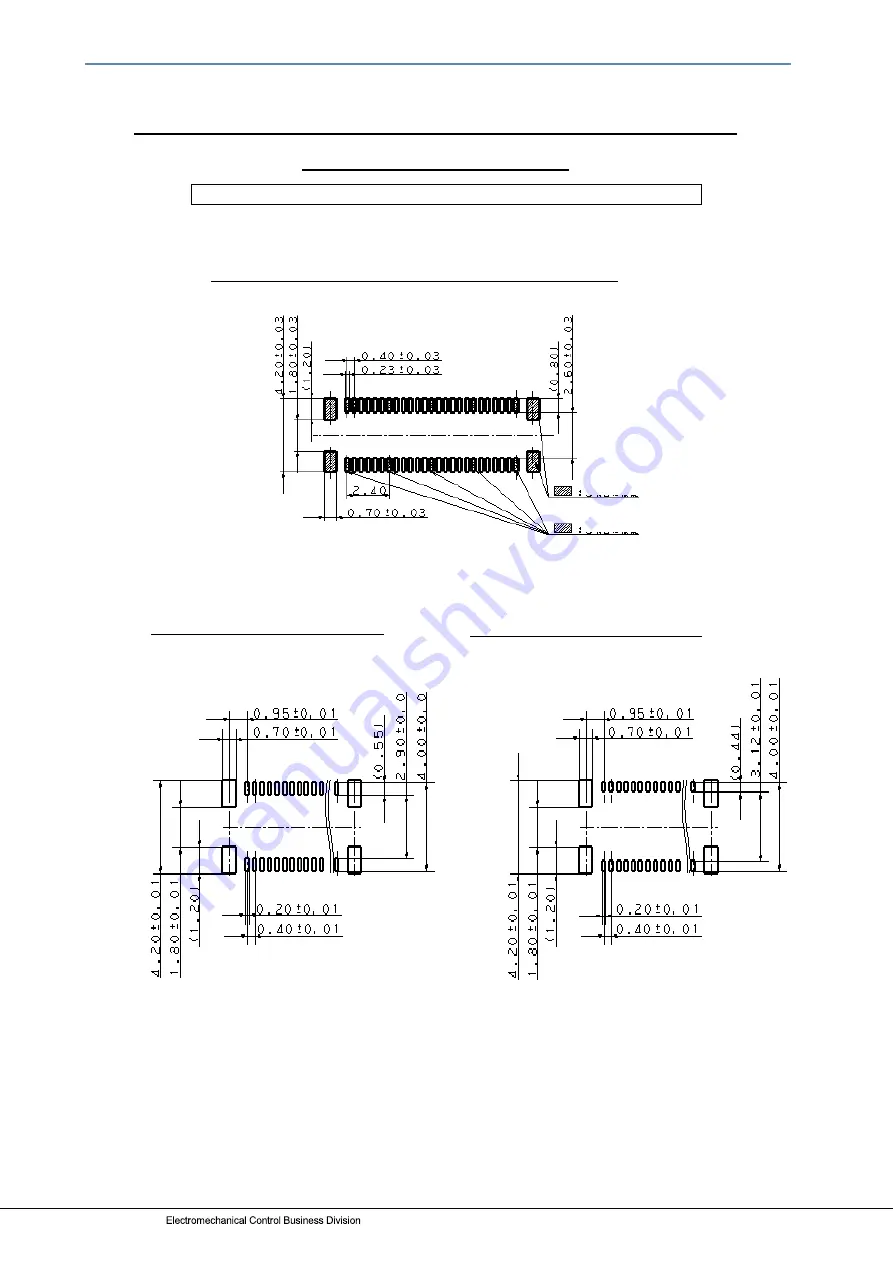
Operation manual for Narrow-pitch connectors P4S Shield type
Panasonic Corporation
industrial.panasonic.com/ac/e/
©
Panasonic Corporation 2017
ACCTF24E-1 201710
14
Recommended specifications of mounting pattern on PC board and
window size of metal masking
Please refer to the latest product specifications when designing your product.
Product: Narrow pitch connector P4S Shield type Socket
Recommended mounting pattern on PC board (Top view)
Thickness of metalmasking:120
μ
m
(Terminal part window ratio:60%)
(Metal bracket part window ratio:100%)
Thickness of metalmasking:150
μ
m
(Terminal part window ratio:48%)
(Metal bracket part window ratio:100%)
Connect to GND
Connect to GND
(2.40 mm pitch)
Summary of Contents for P4S
Page 29: ...ACCTF24E 1 201710 2017 ...