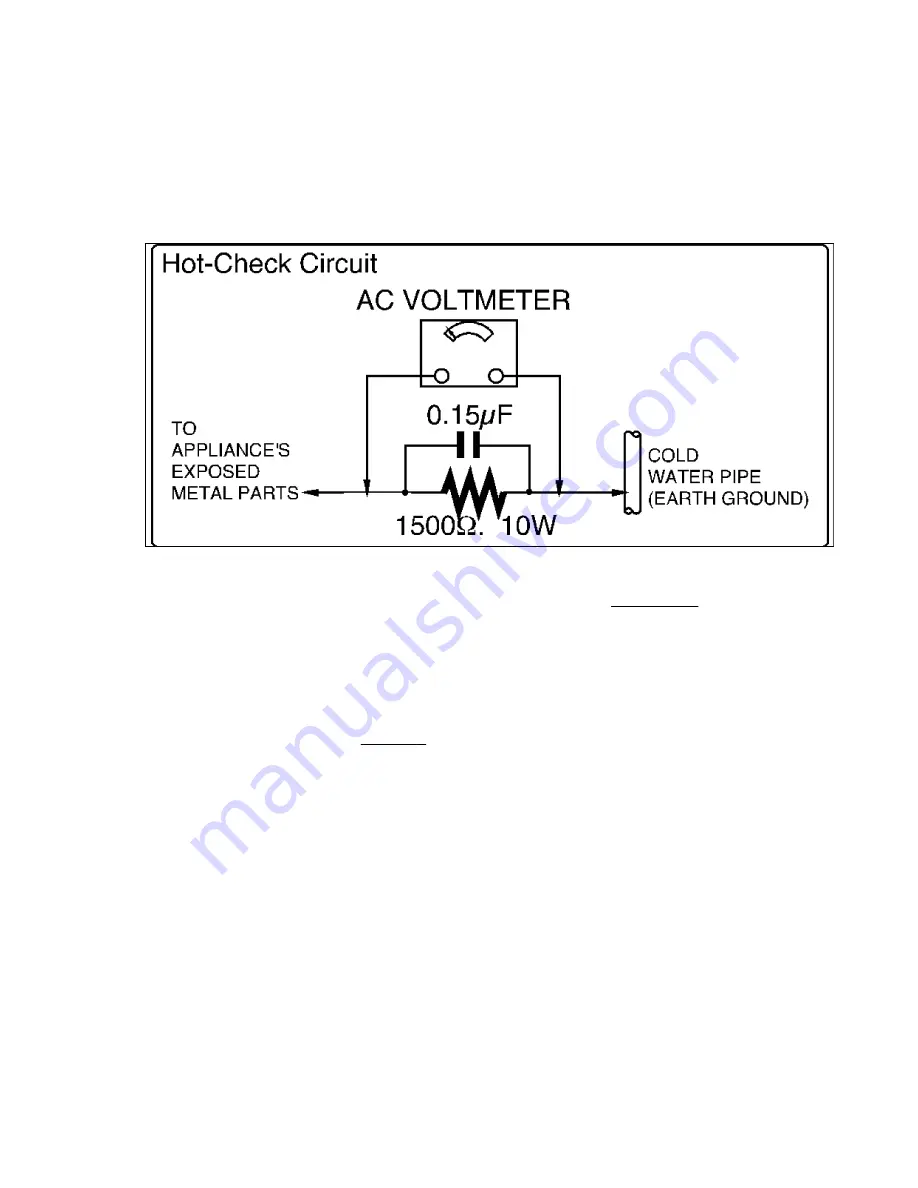
2. Measure the resistance value, with an ohmmeter, between the jumpered AC plug
and each exposed metallic cabinet part on the equipment such as screwheads,
connectors, control shafts, etc. When the exposed metallic part has a return path
to the chassis, the reading should be between 1M ohm and 5.2M ohm. When the
exposed metal does not have a return path to the chassis, the reading must be
∞
∞
∞
∞
Figure 1
1.3. LEAKAGE CURRENT HOT CHECK (See
Figure 1
.)
1. Plug the AC cord directly into the AC outlet. Do not use an isolation transformer for
this check.
2. Connect a 1.5K ohm, 10 watts resistor, in parallel with a 0.15 micro farad capacitor,
between each exposed metallic part on the set and a good earth ground such as a
water pipe, as shown in
Figure 1
.
3. Use an AC voltmeter, with 1000 ohms/volt or more sensitivity, to measure the
potential across the resistor.
4. Check each exposed metallic part, and measure the voltage at each point.
5. Reverse the AC plug in the AC outlet and repeat each of the above measurements.
6. The potential at any point should not exceed 0.75 volts RMS. A leakage current
tester (Simpson Model 229 or equivalent) may be used to make the hot checks,
leakage current must not exceed 1/2 milliamp. In case a measurement is outside of
the limits specified, there is a possibility of a shock hazard, and the equipment
should be repaired and rechecked before it is returned to the customer.
2. PREVENTION OF ELECTRO STATIC DISCHARGE
(ESD) TO ELECTROSTATICALLY SENSITIVE(ES)
5
Summary of Contents for PV-4601 A
Page 14: ...Fig 2 3 14 ...
Page 27: ...Fig 11 1 1 27 ...
Page 40: ...Fig D1 40 ...
Page 42: ...Fig D2 42 ...
Page 43: ...Fig D3 43 ...
Page 44: ...Fig D4 44 ...
Page 45: ...Fig D5 45 ...
Page 46: ...Fig D7 46 ...
Page 47: ...Fig D8 47 ...
Page 51: ...Fig M2 1 Fig M2 2 51 ...
Page 53: ...Fig M4 1 53 ...
Page 77: ...Fig M19 77 ...
Page 84: ...Fig J5 84 ...
Page 85: ...Fig J6 85 ...
Page 87: ...Fig J9 87 ...
Page 88: ...Fig J10 88 ...
Page 89: ...Fig J11 89 ...
Page 90: ...Fig J12 90 ...
Page 91: ...Fig J13 91 ...
Page 92: ...Fig J15 92 ...
Page 93: ...93 ...
Page 96: ...96 ...
Page 102: ...with the holes on the Pinch Lift Cam as shown in Fig A6 102 ...
Page 103: ...103 ...
Page 105: ...Fig K1 105 ...
Page 106: ...Fig K2 106 ...
Page 107: ...Fig K3 107 ...
Page 109: ...Fig B1 109 ...
Page 114: ...Fig E1 4 3 2 HOW TO READ THE ADJUSTMENT PROCEDURES 114 ...
Page 115: ...Fig E2 115 ...
Page 134: ...R6004 ERJ6GEYJ333V MGF CHIP 1 10W 33K 134 ...
Page 136: ...R6085 ERJ6GEYJ223V MGF CHIP 1 10W 22K 136 ...
Page 140: ...C4601 ECEA1CKA100 ELECTROLYTIC 16V 10 140 ...
Page 147: ...R6065 ERJ6GEYJ223V MGF CHIP 1 10W 22K 147 ...
Page 167: ...9 11 Operation Block Diagrams 1 167 ...
Page 178: ......
Page 204: ......
Page 205: ......