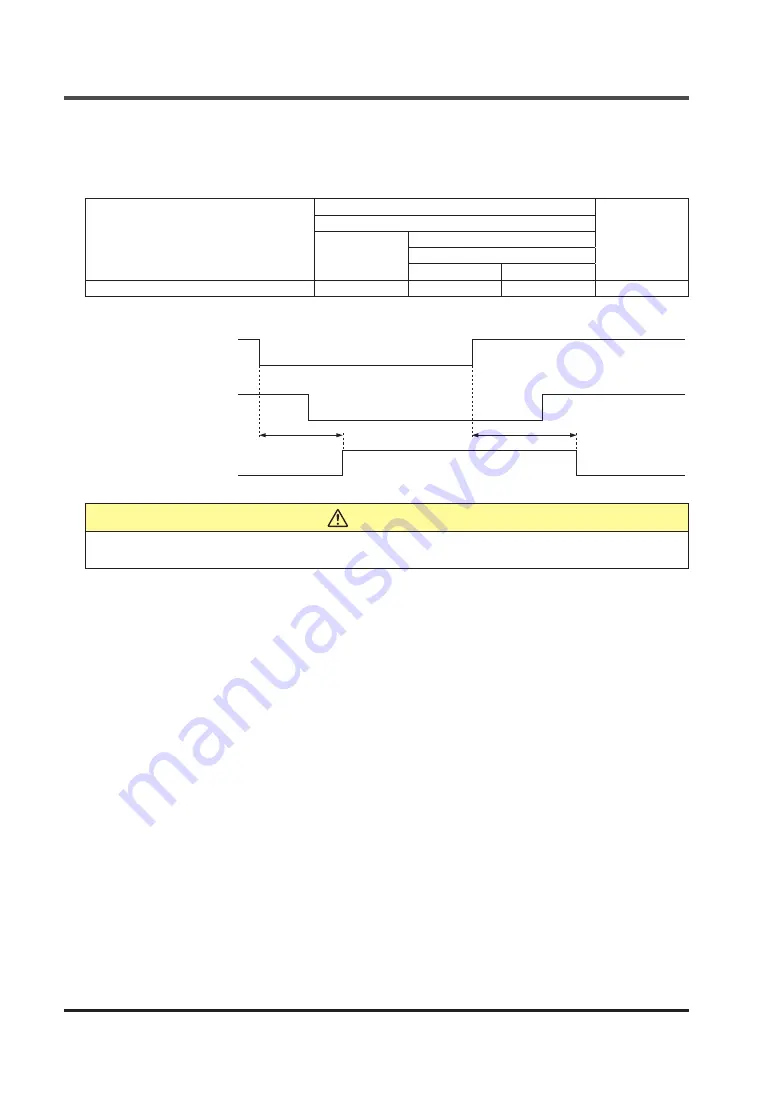
Functions
© Panasonic Industrial Devices SUNX Co., Ltd. 2020
104
3-5 Auxiliary Output (Non-Safety Output) (8-core cable, 12-core cable)
The device is equipped with an auxiliary output for non-safety applications.
The auxiliary output can be used to monitor specific states of the device.
Auxiliary output
Normal operation
Lockout
Test input state
Valid
Invalid
Control output (OSSD 1 / 2) state
ON
OFF
Control output (OSSD 1 / 2) negative logic
ON
OFF
ON
ON
<Timing chart>
ON
ON
OFF
OFF
60ms or less
60ms or less
Light received
Light blocked
Light received
state
Auxiliary output (OSSD
1 / 2 negative logic)
Control output
(OSSD 1 / 2)
WARNING
Do not use the auxiliary output for the purpose of stopping the machine for which the device is in-
stalled. Risk of death or serious injury.
Summary of Contents for SF4D-*-01 Series
Page 2: ... Panasonic Industrial Devices SUNX Co Ltd 2020 2 MEMO ...
Page 6: ... Panasonic Industrial Devices SUNX Co Ltd 2020 6 MEMO ...
Page 120: ...Functions Panasonic Industrial Devices SUNX Co Ltd 2020 120 MEMO ...
Page 134: ...Troubleshooting Panasonic Industrial Devices SUNX Co Ltd 2020 134 MEMO ...
Page 168: ... Panasonic Industrial Devices SUNX Co Ltd 2020 168 MEMO ...