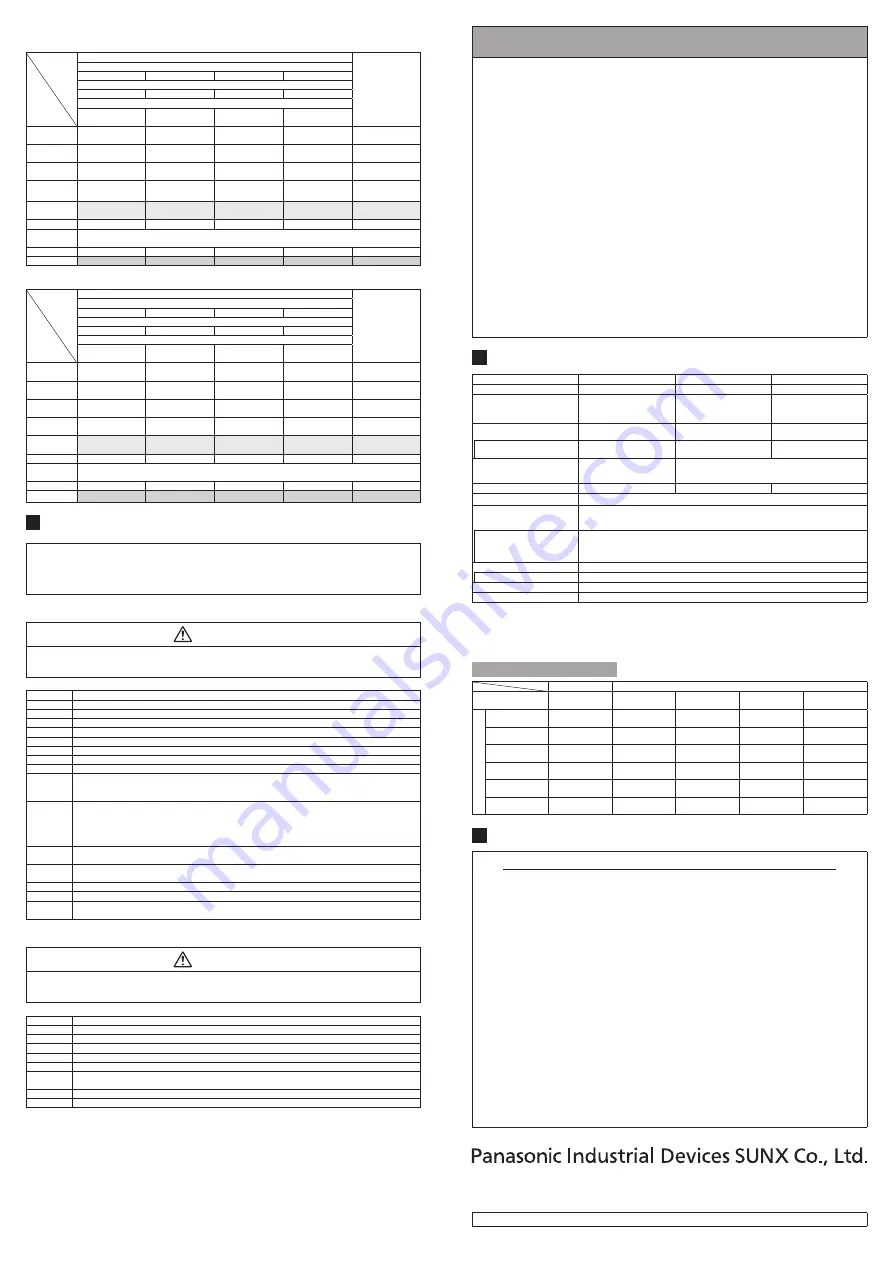
<Conditions: Line synchronization, Test input function invalid, Interlock function invalid>
●
Emitter indicator operation when error occurs
Light blocked state
Light received state
(all beam channels)
Top end beam channel
Light blocked
Light received
Light blocked
Light received
Bottom end beam channel
Light blocked
Light blocked
Light received
Light received
Other beam channels
Light received /
Light blocked
Light received /
Light blocked
Light received /
Light blocked
Light blocked
Control output
(OSSD 1 / 2)
OFF
OFF
OFF
OFF
OFF
Upper application
indicator
Turns OFF
Turns OFF
Turns OFF
Turns OFF
Turns OFF
Lower application
indicator
Turns OFF
Turns OFF
Turns OFF
Turns OFF
Turns OFF
Stable light
reception indicator
Turns OFF
Turns OFF
Turns OFF
Turns OFF
Turns OFF
Digital indicator Blinking or lights
yellow number
Blinking or lights
yellow number
Blinking or lights
yellow number
Blinking or lights
yellow number
Blinking or lights
yellow number
Frequency indicator
Turns OFF
Turns OFF
Turns OFF
Turns OFF
Turns OFF
Light emission intensity
control indicator
When short mode is selected by DIP switch: Lights orange
Test indicator
Turns OFF
Turns OFF
Turns OFF
Turns OFF
Turns OFF
Operation indicator
Lights red
Lights red
Lights red
Lights red
Lights red
●
Receiver indicator operation when error occurs
Light blocked state
Light received state
(all beam channels)
Top end beam channel
Light blocked
Light received
Light blocked
Light received
Bottom end beam channel
Light blocked
Light blocked
Light received
Light received
Other beam channels
Light received /
Light blocked
Light received /
Light blocked
Light received /
Light blocked
Light blocked
Control output
(OSSD 1 / 2)
OFF
OFF
OFF
OFF
OFF
Upper application
indicator
Turns OFF
Turns OFF
Turns OFF
Turns OFF
Turns OFF
Lower application
indicator
Turns OFF
Turns OFF
Turns OFF
Turns OFF
Turns OFF
Stable light
reception indicator
Turns OFF
Turns OFF
Turns OFF
Turns OFF
Turns OFF
Digital indicator Blinking or lights
yellow number
Blinking or lights
yellow number
Blinking or lights
yellow number
Blinking or lights
yellow number
Blinking or lights
yellow number
Frequency indicator
Turns OFF
Turns OFF
Turns OFF
Turns OFF
Turns OFF
Function setting
indicator
When the blanking function or parallel connection is used: Lights yellow (Applicable model:
SF4D-□
)
When the communication module
SF4D-TM1
(option) is connected: Blinks orange
Interlock indicator
Turns OFF
Turns OFF
Turns OFF
Turns OFF
Turns OFF
OSSD indicator
Lights red
Lights red
Lights red
Lights red
Lights red
10
MAINTENANCE
<Reference>
If you notice an abnormal condition, refer “
our web site:
https://panasonic.net/id/pidsx/global
”.
If you are unsure what action to take, contact our office.
Make a copy of the checklist, enter a checkmark after checking each item, and retain the list.
●
Daily inspection
WARNING
Before starting work, inspect the items below and verify that there are no abnormalities. Risk of death
or serious injury if inspection is neglected or the device is operated with an abnormal condition.
Check column
Inspection item
□
Dangerous parts of the machine cannot be reached without passing through the sensing area of the device.
□
Some part of the operator’s body remains in the sensing area when working with dangerous parts of the machine.
□
The device is installed at a distance that is equal to or greater than the calculated safety distance.
□
No safety guard or protective structure damage.
□
No damaged, defective, or bent wires.
□
All connectors are firmly connected.
□
No dirt or scratches on the light emitting surface.
□
Test rods are not deformed or defective.
□
When no objects are present in the sensing area, the operation indicator (green) of the emitter and the
OSSD indicator (green) of the receiver are lit. The control output (OSSD 1 / 2) is ON. You can check for
effects of external noise in this state. If external noise affects operation, remove the cause and reinspect.
□
When moved at a speed of 1,600mm/sec or less, it should be possible to detect the test rod [ø14mm
for
SF4D-F
□(
-01
), ø25mm for
SF4D-H
□(
-01
),, ø45mm for
SF4D-A
□(
-01
),] directly in front of the emit-
ter, midway between the emitter and the receiver, and directly in front of the receiver (3 positions).
When the test rod is in the sensing area, the OSSD indicator (red) of the receiver and the operation in-
dicator (red) of the emitter remain lit.
□
When the machine is in the operating state, dangerous parts operate normally (do not stop) when no
objects are present in the sensing area.
□
When the machine is in the operating state, dangerous parts stop immediately when the test rod is inserted directly
in front of the emitter, midway between the emitter and the receiver, and directly in front of the receiver (3 positions).
□
Dangerous parts remain stopped as long as the test rod is present in the sensing area.
□
Dangerous parts stop immediately when the power of the device is turned OFF.
□
Be sure to test operation before using the muting function. Check the condition of the muting indicator
(dirt, brightness, etc.).
●
Periodic inspection (every six months)
WARNING
Be sure to inspect the following items every six months and verify that there are no abnormalities. Risk
of death or serious injury if inspection is neglected or the device is operated with an abnormal condition.
Check column
Inspection item
□
The structure of the machine does not obstruct any safety mechanisms for stopping operation.
□
No modification has been made in the machine control system that obstructs the safety mechanisms.
□
Output from the device is correctly detected.
□
Wiring from the device is correct.
□
The response time of the overall system is equal to or less than the calculated value.
□
The current number of operation cycles (time) of parts with a limited service life is less than the num-
ber of service life cycles (time).
□
No screws or connectors related to the device are loose.
□
No objects that scatter or reflect light have been added near the device.
●
Inspection after maintenance
1.
When any parts of the device are replaced.
2.
When an abnormal condition is noticed during operation.
3.
After aligning the beam axes of the emitter and receiver.
4.
When the installation site or environment of the device is changed.
5.
When the wiring method or wiring layout is changed.
6.
When a safety relay unit or external device (forcible guide relay or magnetic con-
tactor) part has been replaced.
7.
When safety controller or safety PLC settings are changed.
When using as a safety device for a press machine in Japan
(Applicable model: SF4D-□-01)
When using as a safety device for a press machine in Japan, press machine work
supervisors and personnel in charge of the matters described in No. 1, No. 2, and
No. 4 of Article 134 of the Occupational Safety and Health Act are required to per-
form inspection prior to the start of work and perform periodic inspection.
Press machine work supervisors, etc. must inspect the items below prior to the
start of work and record/retain the results.
Device emitter
●
Firmness of installation
●
Suitability of installation position
(safe distance and vertical position)
●
Existence of damage
●
Existence of external wire abnormal-
ities
●
Existence of dirt on emitter
●
Certainty of detection states
Device receiver
●
Firmness of installation
●
Suitability of installation position
(safe distance and vertical position)
●
Existence of damage
●
Existence of external wire abnormal-
ities
●
Existence of dirt on emitter
●
Certainty of detection states
Specified control unit
SF-C11
,
SF-C13
●
External wiring
●
Indicator
●
Abnormal operation of switches, etc.
●
Firmness of installation
For details, refer to "Press Machine Safety Device Control Policy" of the Ministry of
Health, Labour and Welfare.
11
SPECIFICATIONS
Type
10mm pitch type
20mm pitch type
40mm pitch type
Model No.
SF4D-F
□(
-01
)
SF4D-H
□(
-01
)
SF4D-A
□(
-01
)
Number of beam channels
15/23/31/39/47/55/63/71/
79/95/111/127
8/12/16/20/24/28/32/36/40
/48/56/64/72/80/88/96
4/6/8/10/12/14/16/18/20/
24/28/32/36/40/44/48
Detection width
(protection height)
150 (15 beam channels) to
1,270mm (127 beam channels)
150 (8 beam channels) to
1,910mm (96 beam channels)
150 (4 beam channels) to
1,910mm (48 beam channels)
When using as safety equipment for
press machines in Japan and China
140 (15 beam channels) to
1,260mm (127 beam channels)
140 (8 beam channels) to
1,900mm (96 beam channels)
120 (4 beam channels) to
1,880mm (48 beam channels)
Sensing range (effective)
Short mode: 0.2 to 7m
Long mode: 0.8 to 12m
(selectable by DIP switch)
Short mode: 0.2 to 9m, Long mode: 0.8 to 15m
(selectable by DIP switch)
Minimum sensing object
ø14mm opaque object
ø25mm opaque object
ø45mm opaque object
Supply voltage
24V DC
+20
-30
% (excluding voltage drop due to cable)
Control output (OSSD 1 / 2)
Maximum source (PNP) / sink (NPN) current: 350mA, Residual voltage: 2V or less
Leakage current: 0.2mA or less, Maximum load capacity: 2.2μF
Load wiring resistance: 3Ω or less
Response time
OFF response: 10ms or less (not connected in serial / parallel)
18ms or less (connected in serial / parallel)
(Refer to
<Response time by number of beam channels (OFF response)>
)
ON response: 50ms or less (Note 1, 2)
Auxiliary output (AUX)
Maximum source (PNP) / sink (NPN) current: 60mA, residual voltage: 2V or less
Response time
OFF response: 60ms or less, ON response: 60ms or less
Ambient temperature
−10 to +55°C, Storage: −25 to +60°C
Ambient humidity
30 to 85% RH, storage: 30 to 95% RH
Notes: 1) Because the control output (OSSD 1 / 2) must be OFF for at least 80ms, the ON response will be delayed
more than 50ms when the light blocked time is less than 30ms.
2) When optical synchronization is selected, if the beam axes of both the top end and bottom end are blocked,
the ON response speed decreases by as much as 1 sec.
<Response time by number of beam channels (OFF response)>
Control output (OSSD 1 / 2)
Main sensor
Sub sensor
Number of units in
series connection
1 unit
1 unit
2 units
3 units
4 units
Number of beam channels
4 to 48 beam
channels
6ms
10ms
10ms
12ms
12ms
49 to 96 beam
channels
8ms
10ms
10ms
12ms
12ms
97 to 127 beam
channels
10ms
12ms
12ms
14ms
14ms
128 to 144 beam
channels
−
12ms
12ms
14ms
14ms
145 to 192 beam
channels
−
14ms
14ms
16ms
16ms
193 to 256 beam
channels
−
16ms
16ms
18ms
18ms
12
CE MARKING DECLARATION OF CONFORMITY
Itemized Essentials of EU Declaration of Conformity
Manufacturer’s Name:
Panasonic Industrial Devices SUNX Co., Ltd
Manufacturer’s Address:
2431-1, Ushiyama-cho, Kasugai, Aichi 486-0901, Japan
EU Representative’s Name:
Panasonic Marketing Europe GmbH Panasonic Testing Center
EU Representative’s Address:
Winsbergring 15, 22525 Hamburg,Germany
Product:
Active Opto-electronic Protective Device (Light Curtain)
Model Name: SF4D
Series
Trade Name:
Panasonic
Application of Council Directive:
- 2006/42/EC Machinery Directive
- 2014/30/EU EMC Directive
- 2011/65/EU RoHS Directive
Harmonized standards:
- EN 61496-1
- EN ISO 13849-1
- EN 55011
- EN 61000-6-2
- EN 50581
Type Examination:
Certified by TÜV SÜD Product Service GmbH Ridlerstrasse
65 80339 München Germany
https://panasonic.net/id/pidsx/global
Overseas Sales Division (Head Office)
2431-1 Ushiyama-cho, Kasugai-shi, Aichi, 486-0901, Japan
Phone: +81-568-33-7861 FAX: +81-568-33-8591
For sales network, please visit our website.
PRINTED IN JAPAN
© Panasonic Industrial Devices SUNX Co., Ltd. 2018