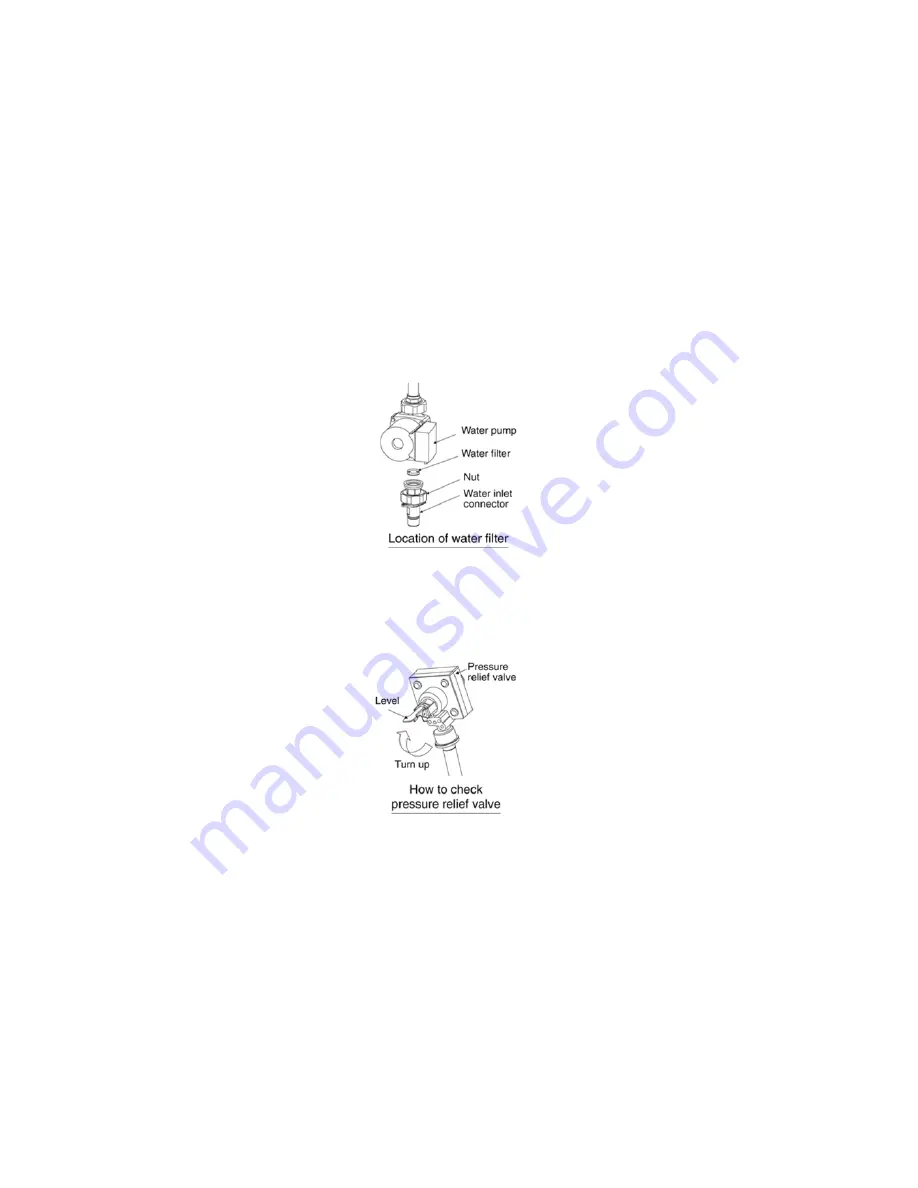
26
13 Maintenance Guide
In order to ensure optimal performance of the unit, checks and inspections on the unit and the field wiring must be carried out
regularly. Please request a licensed technician for carry out maintenance job.
Before carried out any maintenance or repair work, and removing the front plate of heat exchanger unit, always switch off all power
supply (i.e. indoor unit power supply, heater power supply and sanitary tank power supply).
Below checks must be carried out at least once a year.
1. Water pressure
Water pressure should not lower than 0.05 MPa (with inspects the pressure gauge). If necessary add tap water into boiler
tank. Refer to boiler tank installation instruction for details on how to add water.
2. Water filter
Clean the water filter in regularly basic.
• Water filter is located inside the tube connector which is below water pump. (Refer to figure below)
• Use spanner to detach the water pump’s bottom nut.
• Take out the filter carefully so that not deforms it shape.
• Use tap water only to wash the residue on the filter. If necessary, gently use soft brush only to clean the hard dirt.
• After clean, put it back to the original location and tighten the nut connection with torque wrench.
3. Pressure relief valve
• Check for correction operation of pressure relief valve by turn up the level to become horizontal. (Refer to figure below)
• If you do not hear a clacking sound (due to water drainage), contact your local authorized dealer.
• Turn down the level after checking finish.
• In case the water keeps drained out from the unit, switch off the system, and then contact your local authorized dealer.
4. Indoor unit control board area
Thorough visual inspection of the control board and look for defects, i.e. loose connection, melting of wire insulator and etc.
5. RCCB
• Ensure the RCCB set to “ON” condition before check RCCB.
• Push the “TEST” button on the RCCB. The level would turn down and indicate “0” and indicate green colour if it functions
normal.
• Contact authorized dealer if the RCCB malfunction.
• If RCCB functions normal, set the level to “ON” again after testing finish.
Summary of Contents for WH-TX30B9E8
Page 7: ...7 4 Location of Controls and Components 4 1 Tank Unit 4 1 1 Location of Control ...
Page 8: ...8 4 1 2 Main Components ...
Page 9: ...9 5 Dimensions ...
Page 10: ...10 6 Water Cycle Diagram ...
Page 11: ...11 7 Wiring Connection Diagram ...
Page 12: ...12 8 Electronic Circuit Diagram 8 1 Indoor Unit ...
Page 13: ...13 9 Printed Circuit Board 9 1 Tank Unit 9 1 1 Main Printed Circuit Board ...
Page 14: ...14 9 1 2 Surge Printed Circuit Board ...
Page 47: ...47 15 2 Heater Removal Procedures ...
Page 48: ...48 15 3 Main Printed Board Removal Procedures ...
Page 49: ...49 15 4 Control Board Removal Procedure ...
Page 50: ...50 15 5 Pressure Relief Valve Procedures ...
Page 51: ...51 15 6 Flow Switch Removal Procedures 15 7 Water Pump Removal Procedures ...
Page 52: ...52 16 Technical Data 16 1 Pump Characteristic 16 2 Water Tank Sensor Characteristic ...
Page 53: ...53 ...
Page 54: ...54 ...