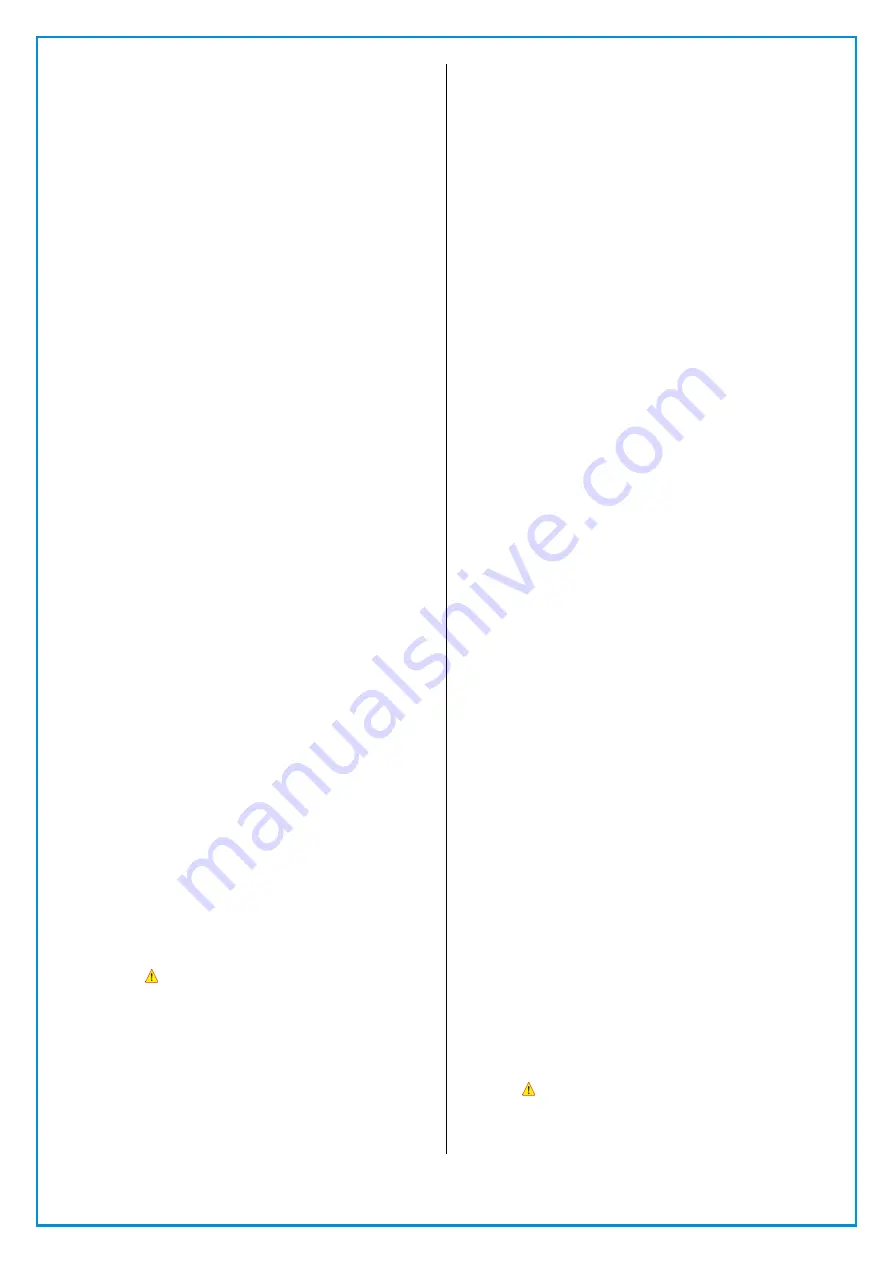
- 2 -
ZVP-PC-0227-00-R0
CONNECTIONS MUST BE OF THE
APPROPRIATE PRESSURE RATING.
2.5
The compressed air supply must also be clean
and dry for the blast cabinet to operate
effectively.
2.6
Connect a suitably sized electrical power supply.
If the electrical supply is being hard wired into
an existing power supply, this must only be
done by a suitably qualified and registered
electrical tradesman.
NOTE: THE RECOMMENDED ELECTRICAL
SUPPLY IS 415VAC 3 PHASE 10AMP.
2.7
Position the cabinet foot pedal at the front of
the cabinet in a position, which is comfortable
for the operator to use. On some models, the
foot pedal may be mounted on a frame attached
to the cabinet itself.
2.8
It is recommended that the cabinet foot pedal
be fixed in position with suitably sized fasteners
for added stability and ease of operation during
use.
The blast cabinet is now ready for operation.
3.0
OPERATING INSTRUCTIONS
3.1
Install the blast cabinet as detailed in Section
2.0 of this manual.
3.2
Remove the pot adaptor cover plate by
loosening the two nuts at the pot adaptor.
3.3
Load the abrasive media into the blast pot
through the pot adaptor opening. The abrasive
level should remain below the bottom of the
pop up valve to prevent premature wear to the
remote exhaust valve assembly.
3.4
Refit the pot adaptor cover plate and ensuring
that the two nuts are properly tightened.
3.5
Turn on the compressed air supply, and slowly
open the main ball valve located at the pressure
regulator assembly.
3.6
Lift up the pressure regulator control knob to
release the lock, and adjust the regulator to the
desired blasting pressure. This is done by
winding the adjustment knob clockwise to
increase pressure, and counter clockwise to
decrease pressure.
3.7
The pressure gauge mounted on the front of the
regulator indicates the system air pressure in
both kPa and PSI. Do not set the blast pressure
below 345 kPa (50psi) as the blast system may
not operate correctly (this is to ensure that the
pop up valve will fully close).
! WARNING ! – DO NOT EXCEED THE
MAXIMUM OPERATING PRESSURE OF THE
BLAST POT AT ANY TIME AS THIS COULD
RESULT IN SERIOUS INJURY OR DEATH.
3.8
Open the main cabinet door, and load the
component to be blasted into the main cabinet
area.
3.9
Close the main cabinet door, making sure that
the safety door interlock is properly engaged. It
is a safety feature that the blasting system will
not activate while the cabinet door is open.
3.10
Turn on the main power supply, switch on the
cabinet light at the switch on the front of the
cabinet, and start the dust collector fan by
depressing the on green button located on the
fan starter assembly. The blast cabinet is now
ready for operation.
3.11
The blast cabinet is now ready for operation.
3.12
Depressing the foot pedal will pressurize the
blast pot and blasting will start. Ensure the
nozzle is held in hand before depressing the
foot pedal.
3.13
When the operator is ready to start blasting,
point the blast nozzle at the work piece before
pressing the foot pedal. This will then actuate
the UniFlo remote control valve and start
blasting. Abrasive will not be discharge from the
nozzle if the abrasive valve is not set.
3.14
As there are many different sizes and types of
abrasive blasting media, it is necessary for the
system to be adjusted to allow for each abrasive
type individual performance characteristics.
Most of this adjustment is carried out at the
abrasive valve, located at the bottom of the
blast pot.
3.15
Turn the abrasive valve knob located at the
bottom of blast pot to fully close, and then
slowly open it until the desired abrasive flow
level is achieved. The optimum abrasive flow
level will vary depending on actual operating
conditions and the desired end result, but as a
general rule, the abrasive should appear in the
air stream as a fine mist. Once the desired
abrasive flow rate has been achieved, the
system is now set for ongoing blasting
operations.
3.16
The operator should now manipulate the blast
nozzle to move the blasting action over the
surface of the component being blasted, until
the desired result is achieved. Smooth,
continuous strokes over the component surface
are normally the most effective, with the nozzle
being held approximately 75mm (3") to 125mm
(5") from the component surface.
3.17
To stop the blasting operation, releasing the
foot pedal.
3.18
Allow a few moments for the fan and dust
collector to clear the airborne dust from the
cabinet before opening the cabinet door and
removing the work piece/s
3.19
After removing the work piece, close the door,
shut off the compressed air supply at the main
ball valve.
3.20
Be sure to empty the machine of all abrasive
when shutting down for more than 3-4 hours as
this will reduce the problems associated with
moisture, humidity, etc. when starting a new
day’s operation.
4.0
MAINTENANCE
DAILY SET UP CHECKLIST
! WARNING ! - THE COMPRESSED AIR
SOURCE MUST BE ISOLATED BEFORE
PERFORMING ANY MAINTENANCE WORK.
FAILURE TO DO SO MAY CAUSE SERIOUS
INJURY OR DEATH.