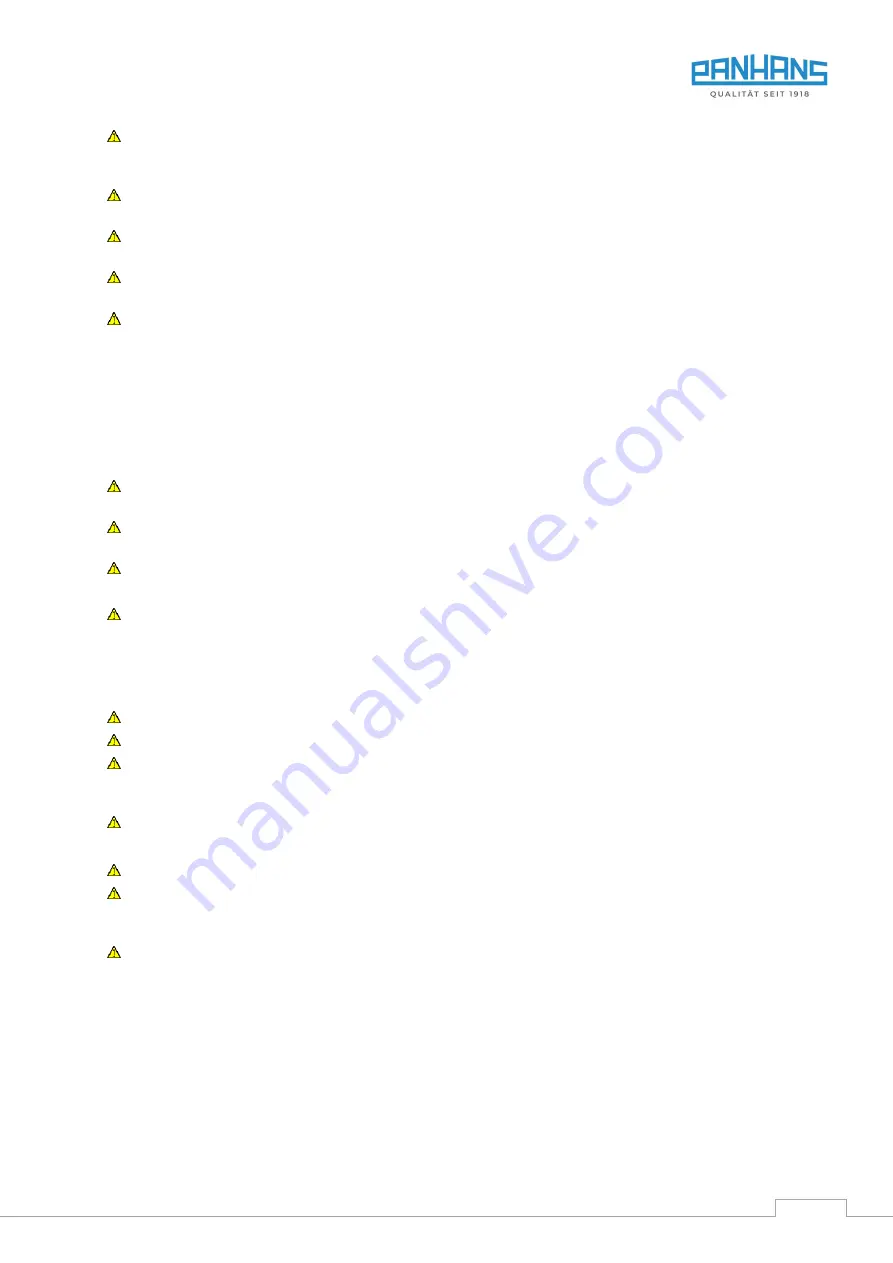
BA_PH_BSB-400-900_EN_44-21.docx
15
Machine condition:
Check the machine for externally visible damage and defects at least once per shift!
Any changes that have occurred (including those in the operating behaviour) must be reported immedi-
ately to the responsible office or person! If necessary, stop and secure the machine immediately!
Extraction:
The machine must be connected to an effective extraction system. This requires a flow velocity
of at least 20 m/s for dry chips and 28 m/s for moist chips (moist 18% or more).
Work area:
An obstacle-free work area around the machine is essential for safe operation. The floor
should be level, well maintained and free from debris such as chips and cut-off workpieces.
Cutting area during operation:
Never try to remove splinters, chips or other parts from the cutting area
while the machine is running! Never remove splinters and chips by hand!
Special tools:
For certain operating phases and operations it is necessary to use special tools for workpiece
feeding (e.g. table fence, push stick, push-block, support bracket etc.).
•
When cutting upright workpieces, secure them against tilting, e.g. by means
of a stop bracket, table fence, push-block.
•
Secure round workpieces with wedge support or similar against twisting.
•
For very short or narrow workpieces use a suitable pushing device.
•
Ensure good workpiece support for long or wide workpieces, e.g. with a table extension.
•
Do not machine unshaped workpieces that do not fit on the machine table.
Work interruptions:
Switch off the machine even during short interruptions! Never leave the machine
running unattended!
When the work is finished:
Release the saw blade tension and provide the machine with a warning sign.
Lower the saw blade guard to table height.
Leaving the machine:
Switch off the control voltage and main switch before leaving the machine. Never
leave the machine unattended in an unsecured state.
Behaviour in the event of a saw blade breakage:
Be sure to wait until all bandsaw wheels have come to a
complete standstill before taking any further action. Only the lower wheel is equipped with a brake!
4.2.3
Special work within the Scope of Maintenance Work as well as Troubleshooting in
the Workflow
Observe maintenance and inspection activities prescribed in the operating manual!
These activities, as well as all other repair work, may only be carried out by qualified personnel!
For all work concerning operation, production adjustment, conversion or setting of the machine and its
safety-related equipment as well as maintenance and repair, observe switch-on and switch-off procedures
according to the operating manual and instructions for maintenance work!
Secure the machine against unexpected restarting during maintenance and repair work.
•
Lock the main switch with a padlock!
Always tighten screw connections that have been loosened during maintenance and repair work!
If it is necessary to dismantle safety equipment during set-up, maintenance and repair, the safety equip-
ment must be reassembled and checked immediately after completion of the maintenance and repair
work!
Ensure safe and environmentally friendly disposal of operating and auxiliary materials (e.g. oils) and re-
placement parts (e.g. electronic components)! Refer to chapter
“Disassembly and Scrapping”.