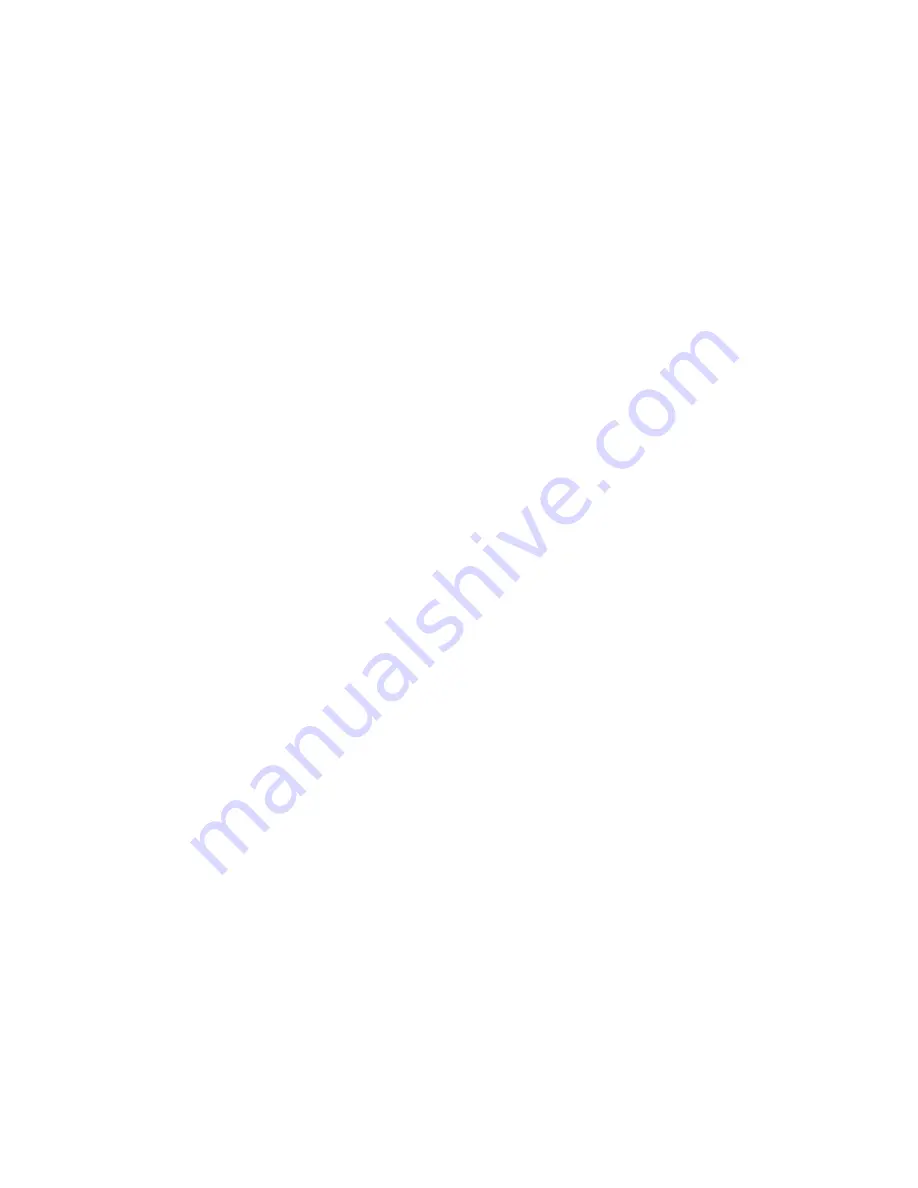
70-PHW-1025 R0.6 023-037X MT-IR Refrigerant Leak Detector spec & Install.doc
10
CALIBRATION
Prior to shipment, all sensors manufactured are factory calibrated. The calibration method will set
the base level (or Zero Level) and the gain (or Slope). As the sensor gets older or the ambient
condition changes drastically, the Zero Level may drift upward or downward. The Gain (Slope) will
not normally change.
An adjustment of the Zero Level is necessary to ensure that the MT-IR is reading accurately. This
should be done every 6 months. This function can be performed by conducting the Calibration Push
button.
PUSH BUTTON 1 -- Located just to the left of the red DIP Switch block.
1) Make sure the unit is properly wired up and all dip switches are in the off position.
2) Allow at least three hours warm up time. The ambient temperature should be stable and within
the desired operating range.
3) Make sure no refrigerant gas is present during calibration.
4) Depress and hold down the push button 1 (located to the left of DIP SW1) for at least 8 seconds
until the calibration LED red light above the push button lights. Release the push button.
5) The LED red light will go off. If not, make sure switch 6 is off. Consult factory if calibration
LED light stays on or keeps flashing after calibration or during normal operation.
NOTE: If the sensor is reading greater than 80, the sensor will not calibrate. Check for gas leak
around the sensor.
MEASURED GAS CALIBRATION
Equipment Required.
1 Refrigerant Sensor Calibration and Test Kit which includes:
a. Flow Regulating Valve - 1 Liter per minute
b. Calibration Gas Canister - 79.1% Nitrogen / 20.9% Oxygen (Zero Gas)
c. Calibration Gas Canister - Nitrogen Balance / Measured quantity of Refrigerant Gas (Span Gas)
d. Vinyl Tubing for IR Sensor.
The measured gas calibration procedure may be used as a double check of sensor accuracy and only
needs to be done if there are questions of whether or not the sensor is working. It is not necessary
to use measured gas to calibrate the infrared sensor. This procedure involves changing the air
currents drastically inside the sensing chamber, so please use the procedure listed below only as a
test. Since the gas is forced into the sensor the reading will not be as accurate as a normal reading. At
the factory we allow for normal airflow that would occur in a real leak when we calibrate the sensor
and set the zero level. So there will be an artificial reading between the zero gas and measured gas
because of the unusual air currents involved.
1) Place the Plastic tubing that comes with the calibration kit over the inlet valve located to the right
of the wiring plug and connect the other end to the calibration gas canister regulator.
2) Run the 20.9% O2 gas into the sensor for about 5 minutes and wait for the reading to settle.
Press the push button on the sensor right above the dipswitch for 10 seconds. This will be the
artificial zero level.
3) Next run the measured refrigerant gas into the sensor for about 5 minutes. The difference
between the artificial measured gas reading and the artificial zero level reading should be close to the